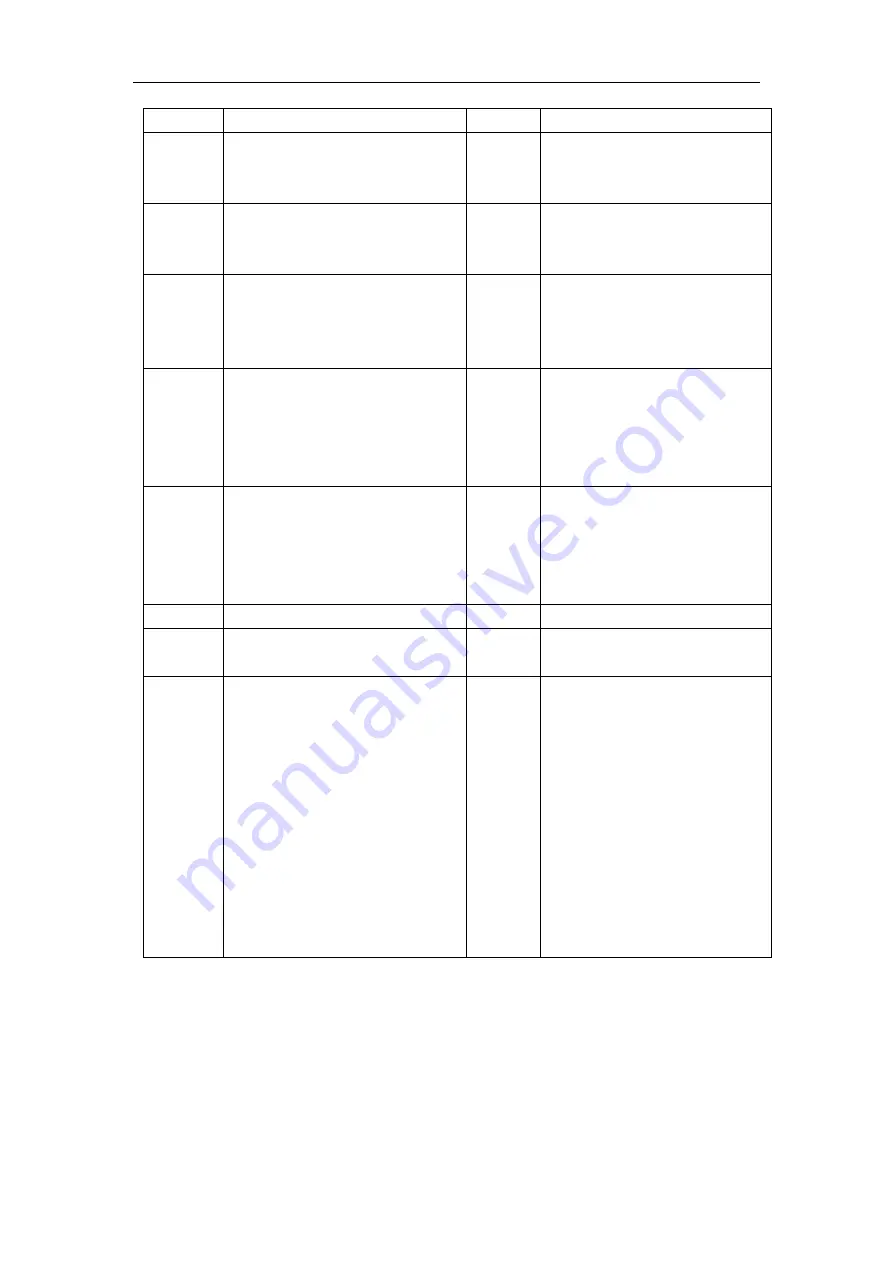
9
Light
Condition
Display
Status/Possible Cause
E01
Over-Current- Check output
diodes, main transformer and
IGBT on the invert board.
Temp
On
E02
Over-Temperature- Stop
cutting, allow machine to
cool down.
E03
No system is established-
Check output diodes, main
transformer and IGBT on the
invert board.
Nozzle
Repetative flashing rate of 3
quick circles, then a 1 second
pause for a 15 second period or
until torch trigger is pressed
again, whichever comes first.
E04
No pilot arc established
possibly due to a loss of
current- Check consumables.
Nozzle
Repetative flashing rate of 3
quick circles, then a 1 second
pause for a 15 second period or
until torch trigger is pressed
again, whichever comes first.
E05
Consumables in torch failed
to separate during pilot arc
possibly due to being stuck-
Check consumables.
E09
No input power.
Cup &
Nozzle
Repetative flashing rate of one
quick circle.
E11
Torch cup is loose or off.
Pressure Repetative flashing rate of 1
quick circle.
E13
E13 means air pressure is out
of range. H means air
pressure has exceeded setting
range. L means air pressure is
under setting range.In
Normal/Grid,the setting
range of air pressure is 4.2-
5.6bar. In Gouging,the
setting range of air pressure
is 2.1-3.5bar. In Marking,the
setting range of air pressure
is 2.1-3.1bar.
Summary of Contents for MicroCut 45 DV
Page 2: ...I...
Page 19: ...14 6 Cutting Guidelines...