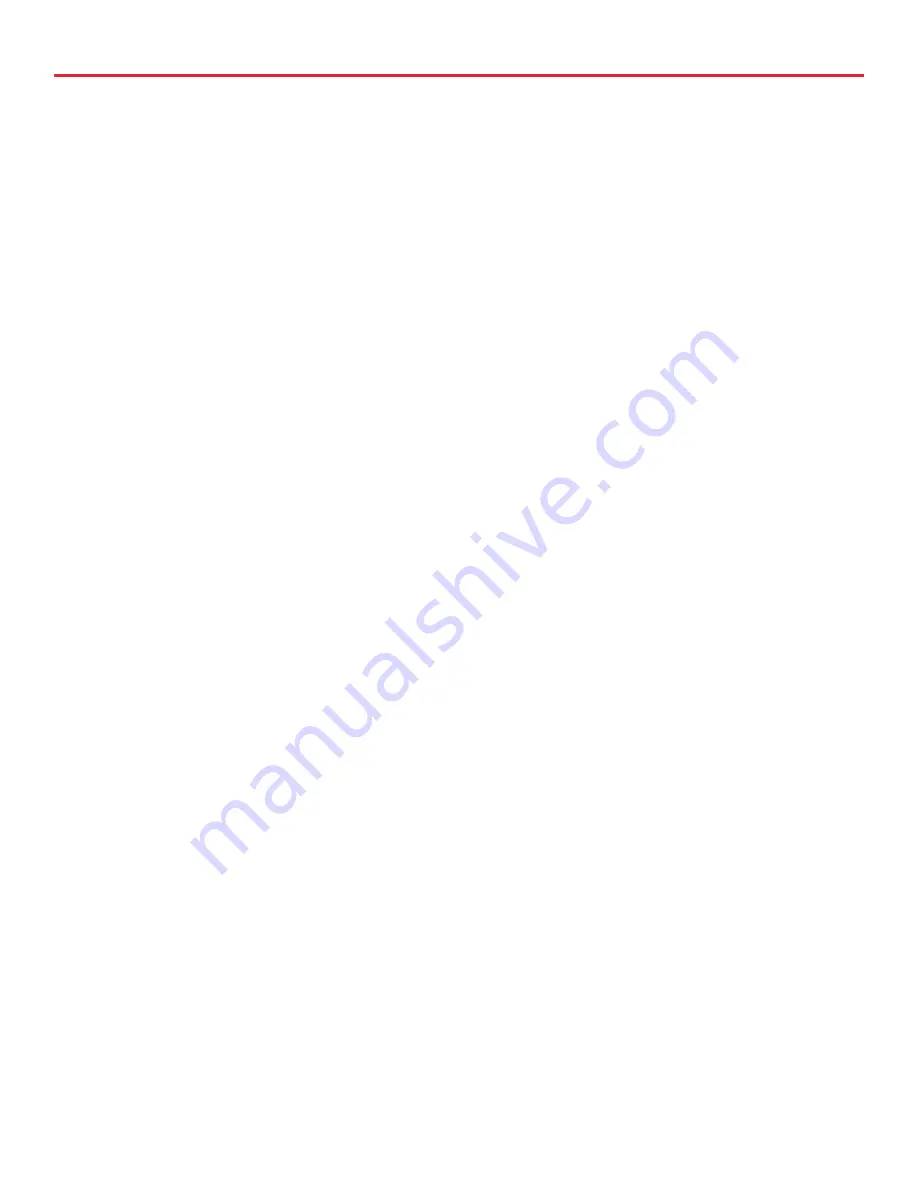
When the welding mode is in the TIG SPOT Mode this button
adjusts the spot welding time from 0.1 sec to 10.0 sec in 0.1 sec
increments. To adjust the “SPOT TIME”, depress and release
the “SLOPE DOWN or SPOT TIME” Button. The “VOLTS”
display will flash “St” for spot time, and the “AMPS” display
will flash and display the spot time in seconds. While both
displays are flashing, adjust the “AMPS” knob (#8) to set the
slope down time.
10. FINAL CURRENT Buttons
Depressing this button allows you to adjust the Final Current.
This is only applicable when your Invertig 201 is set in the
TIG 4T mode, PROGRAM mode, or pulse mode. The final
current is adjustable from 10% to 90% of the base current that
is set by the amperage adjustment knob (#8). For example, if
the amperage adjustment knob is set to 100 amps, and the final
current is set to 15%, the final current will be 15 amps.
To adjust the “FINAL CURRENT” time, depress and release
the “FINAL CURRENT” button. The “VOLTS” display will
flash “FC” for final current, and the “AMPS” display will flash
and display the final current in percent. While both displays are
flashing, adjust the “AMPS” knob (#8) to set final current in
percent of the base current.
11. POST GAS
The post gas flow is adjustable from .5 sec to 30 sec in 0.1 sec
increments. Post gas flow is necessary because after the arc
is extinguished; if the gas stopped flowing immediately, there
is a possibility the molten weld puddle would come in contact
with the atmosphere, causing weld defects. Additionally it
prevents the tungsten from becoming contaminated by the
atmosphere while it is still hot. The gas flow should run long
enough to allow the orange color of the tungsten to disappear.
It is important to remember not to remove the TIG torch
from the weld until the post gas cycle has been completed. A
good starting point for the post gas flow is 5.0 sec. If you are
welding at higher amperages or on more critical alloys it may
be necessary to increase the post gas flow to a higher value.
To adjust the “POST GAS” time, depress and release the
“POST GAS” button. The “VOLTS” display will flash “PG”
for post gas, and the “AMPS” display will flash and display
the post gas time in seconds. While both displays are flashing,
adjust the “AMPS” knob (#8) to set the post gas flow time in
seconds.
12. PULSE ON
By depressing the “PULSE ON” button, the green light will
illuminate indicating your Invertig 201 is in the pulse mode.
At this time the “VOLTS” display will show “dut” for the
pulsing duty cycle. The “AMPS” display will show “FrE” for
the pulsing frequency. Which ever display is flashing is the one
which can be adjusted by the amperage adjustment knob (#8). If
the “dut” is flashing and you want to adjust the frequency, simply
depress and release the “PULSE ON” button and the other
display will begin flashing and you will be able to adjust it.
To adjust the pulse duty cycle, depress and release the “PULSE
ON” button until “dut” which is displayed in the “VOLTS”
display is flashing. While the display is flashing, adjust the
“AMPS” knob (#8) to set the pulse duty cycle. Once the amps
knob is turned, the display will change from “dut” to display the
duty cycle in percent. The duty cycle can be adjusted from 30%
to 65% in increments of 5%.
To adjust the pulse frequency, depress and release the “PULSE
ON" button until “FrE” which is displayed in the “VOLTS”
display is flashing. While the display is flashing, adjust the
“AMPS” knob (#8) to set the pulse frequency. Once the amps
knob is turned, the display will change from “FrE” to display
the frequency in Hz. The frequency can be adjusted from 0.4
to 2.0 Hz in the AC mode, and from 0.4 to 300 Hz in the DC
mode.
To turn off the pulse mode, depress the “PULSE ON” button at
least 3 seconds until the green pulse light goes off.
13. AC Frequency Knob
The AC frequency knob adjusts the length of the AC square
wave. It can be adjusted from 20 Hz to 200 Hz without
any loss in welding output. When the AC is on, and the
“FREQUENCY” knob is adjusted, the amps display flashes and
becomes the frequency display.
Conventional transformer machines have their AC frequency
fixed at 60 Hz. It is beneficial to run the machine at the higher
frequencies (150 to 200hz) for the following reasons:
A) Produces a more focused arc that results in a narrower bead.
B) Heat is more concentrated, minimizing the heat
affected zone.
C) Allows you to weld aluminum with a 2% thoriated,
2% ceriated or 2% lanthanated tungsten sharpened to a point.
Arc is much more stable and is less likely to wander.
14. REMOTE ON
When the remote is on, the green indicator lamp will be
illuminated position, the amperage is infinitely adjustable by
either the foot pedal or the torch mounted amperage control.
It is possible to limit the maximum amperage of your TIG 201.
To limit the maximum amperage of the machine to 100 amps,
for example, with the foot pedal plugged in or torch mounted
amperage control plugged into the 5 pin connection, depress the
“REMOTE ON” button for 5 seconds until the green indicator
lamp turns off. Using the amperage adjustment knob (#8) adjust
the amperage to 100 amps. Depress the "REMOTE ON" button
for 5 seconds until the green indicator lamp turns on. The
digital display panel should read 5 amps. Now, when you fully
depress the foot pedal, the amperage displayed should be 100
amps. This makes the foot pedal less sensitive and makes
it easier to control your puddle.
6