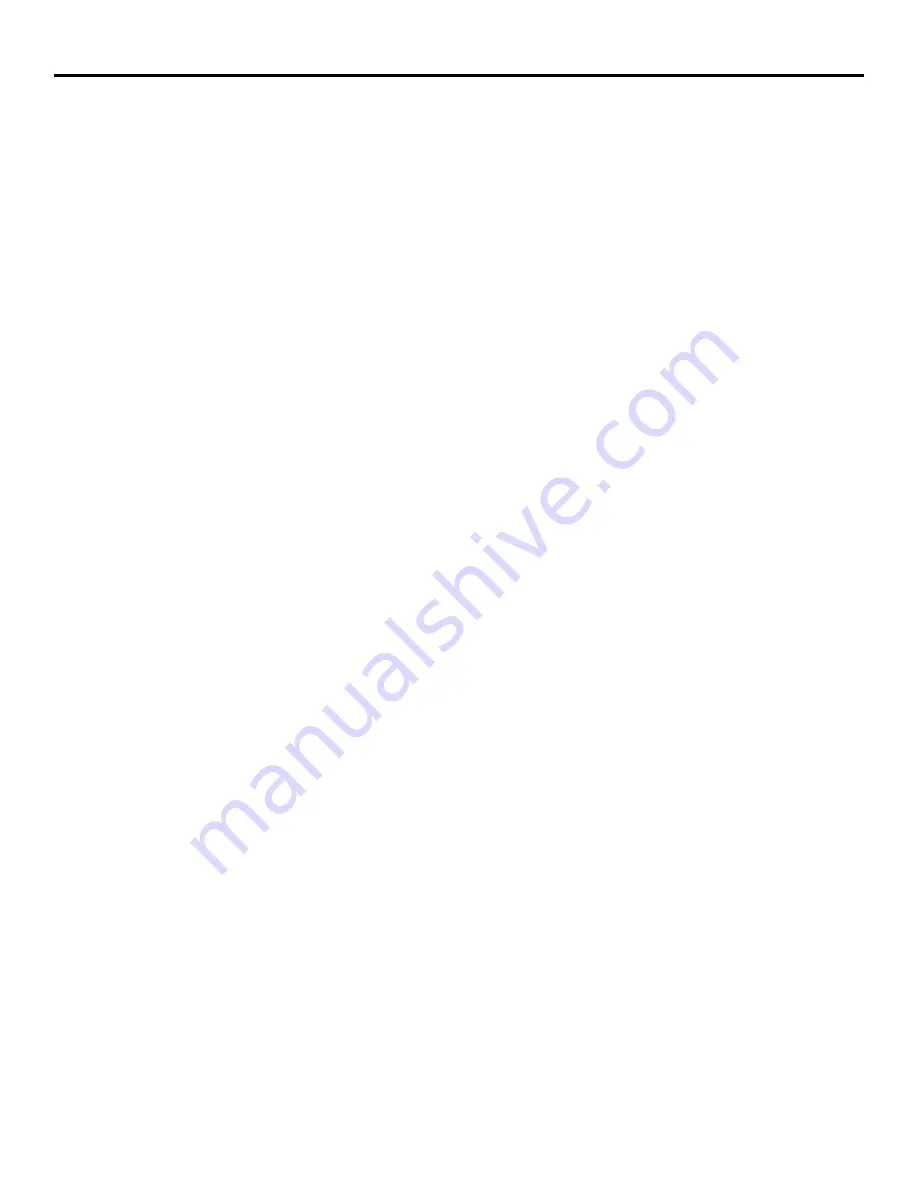
4
5. Welding Mode Switch
The welding mode switch selects the welding mode of your
Invertig 200 AC/DC.
A)
Lift Arc Mode
– the lift arc mode allows you to initiate the
welding arc without high frequency. This is important in any
environment where the high frequency arc will cause
interference with sensitive electrical components or
computers. A good example of this would be stainless steel
or aluminum repair in hospitals. The Lift Arc mode works
for both AC and DC welding.
To TIG Weld using the Lift Arc Mode, simply touch the
tungsten to the workpiece, activate the torch trigger or
depress the foot pedal and lift off. When the tungsten breaks
contact with the work, the arc will start. You can also use
this method for Stick welding with the added benefit of
being able to vary your amperage with the foot pedal.
B)
Spot Welding Mode
– the spot welding mode allows you to
weld for between 0.1 and 10 seconds and then the unit will
automatically stop. This would be a good selection if you
were performing a series of repetitive tack welds.
To select the spot welding time, adjust the T2 buttons up or
down to select a time between 0.1sec and 10.0 sec.
C)
4T mod
e – This is like a lock on trigger on a drill or grinder.
We suggest using this mode with the hand amperage control,
which is mounted on the torch. When you depress the
trigger on the torch, your Invertig 200 will start welding.
When you release the trigger, it will continue to weld until
you depress the trigger again and release it at which time the
arc will extinguish.
When using the hand amperage control, it allows you to
weld without having to keep the trigger depressed, allowing
you to now operate the amperage control.
It is not suggested to use the 4T mode with the foot pedal.
D)
2T mod
e – With the torch trigger or foot pedal depressed,
your Invertig 200 will start the arc. When the trigger is
released, the unit will stop. Select this welding mode for
operation with the foot pedal.
E)
Arc Weldin
g – this mode is used when arc welding. The
electrode will always be hot and the gas solenoid will not
operate.
6. Amperage Adjustment Knob
This knob determines the welding amperage. The amperage
on your Invertig 200 can be adjusted from 5 to 200 amps. The
amperage is displayed in the digital display panel (#4) when the
local/remote switch (#10) is in the local position.
When using a remote amperage control, the amperage
adjustment knob is used to select the maximum amperage for
your particular welding application. For example, when
welding .050" 6061 alloy aluminum, I adjusted the amperage
knob to 100 amps with the local/remote switch in the local
position. This is about 20% more power than I will be welding
the aluminum with. I then placed the local/remote switch in the
remote position and the digital display showed the minimum
amperage of 5 amps. If I were to depress the foot pedal
completely, the maximum amperage would now be 100 amps.
Setting the machine so the maximum amperage is 100 amps vs
the maximum output of the machine of 200 amps, the pedal is
less sensitive. More of a movement in the pedal results in a
smaller variance of the amperage, making it easier to control the
heat and therefore easier to control your puddle.
7. T2 buttons
The T2 buttons are multi-function buttons. The function
depends on which welding mode the welding mode selector
is in.
Lift-Arc, 4T, and 2T Welding Modes
– the T2 buttons controls
the slope down time. The slope down time is adjustable from
0.1 sec to 10.0 sec in 0.1 sec increments. Different slope down
times can be set for each of the three welding modes. For
example, it is possible to have the slope down time set to 0.1 sec
in the 2T mode, 3 sec in the 4T mode and 5 sec in the lift arc
mode. Your Invertig 200 will remember the slope down time
for each welding mode.
If you are using a torch mounted remote amperage control or a
foot pedal, it is advisable to set the slope down time to 0.1 sec,
as you are controlling the slope down manually with your
remote amperage control or foot pedal.
Spot Welding Mode
– the T2 buttons adjust the spot welding
time from 0.1 sec to 10.0 sec in 0.1 sec increments.
Pulse mode on
– depressing the Pulse button when the pulse
mode is on will display the pulsing frequency in Hz. Use the T2
button to adjust the pulse frequency from 0.4 Hz to 2.0 Hz in
the AC mode and from 0.4 Hz to 300 Hz in the DC mode.
Summary of Contents for Invertig 200
Page 14: ...13 HTP Invertig 200 Parts Breakdown...
Page 20: ......