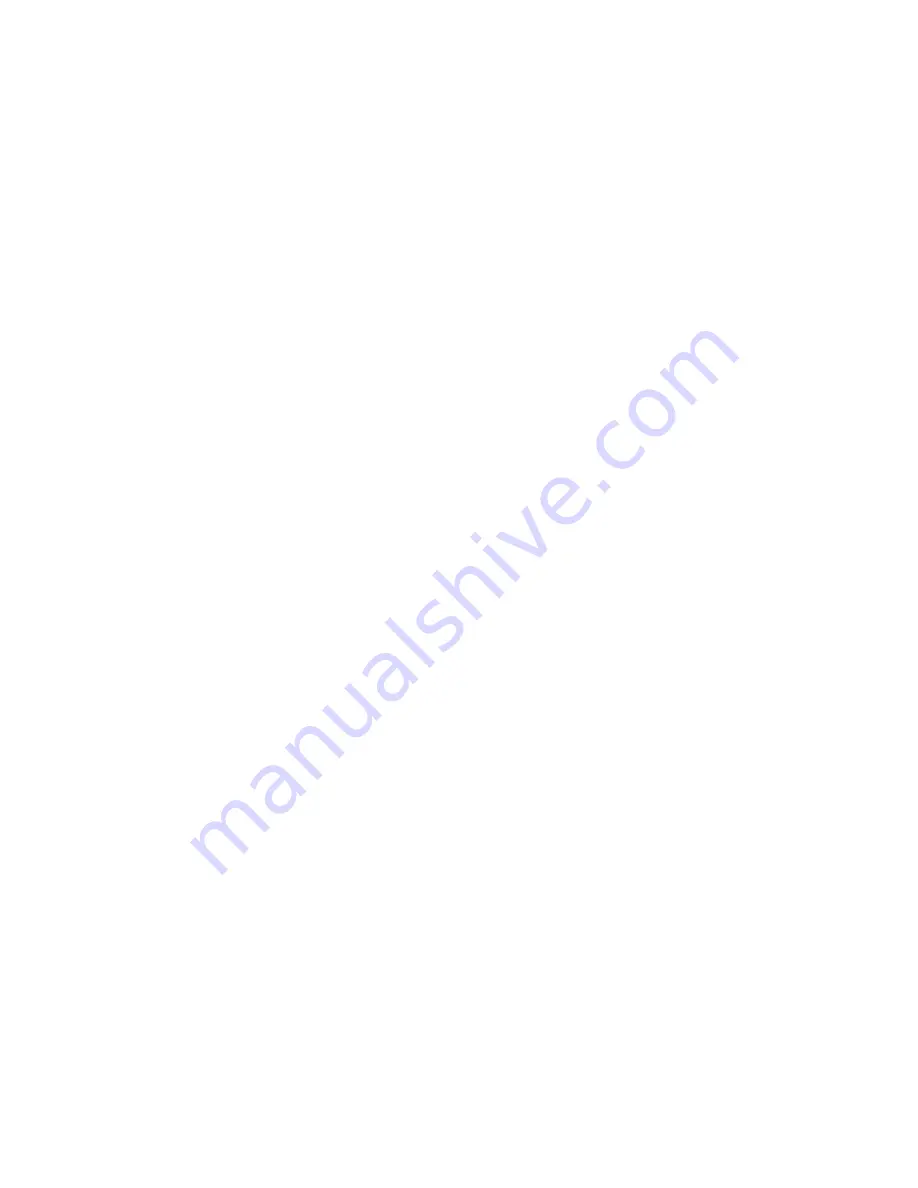
8
Evolution of Stick Welding
Back in the early 1900s, welders would make their own stick electrodes by dipping metal rods in different
chemical solutions to create something similar to the flux coating used on today’s electrodes. The processes
used to make stick electrodes were time consuming and welding with the electrodes often produced
undesirable results. However, the process was refined during the 1940s and 1950s, and welders could
purchase store bought electrodes similar to what we buy and use today. The refined process for creating
stick welding electrodes made a huge difference in the consistency and quality of the rods and the welds
produced using the rods.
The machines used for stick welding also looked and performed differently than they do today. In the
beginning, welders used transformers and generators to produce the welding current. There are two major
kinds of welding current—AC (alternating current) and DC (direct current). Many older welding machines
utilize AC current because welding machines utilizing AC current were easier and cheaper to make. Today,
most stick welding machines utilize DC current because rods are typically designed to run on DC, and there
are certain advantages to DC welding that prompted much of the industry go that route. Not much changed
about stick welding equipment from the early 1900s to the 1980s—even companies who have been in
business for 100+ years build the same model engine driven welding machines over and over with minimal
changes.
In the last couple of decades, however, stick welding technology has undergone some major advancements.
New inverters were introduced to the market, and 200 amp welding machines now weigh less than 55 lbs.
instead of 800+ lbs. The required input for these machines also went down from around 100 amps to 20 or
30 amps. These are some of the more obvious changes—the real evolution of stick welding technology is
hidden from the operator.
The real evolution came about as inverter technology advanced, making options and adjustments such as
arc force and hot start available at the touch of a dial, and these additions and advancements changed the
volt amp curves. In 2005, an Italian manufacturer even added a pulse feature to a stick welder for the first
time ever.
Setting Up and Operating the Inverarc 200 TLP
The Inverarc 200 TLP is capable of the following processes: SMAW (stick), SMAW-P (pulsed stick),
GTAW (TIG), and GTAW-P (pulsed TIG).
The Inverarc 200 TLP offers two different stick welding options:
1) ARC—The standard welding mode for most welding rod.
2) CEL—The welding mode with enhanced arc characteristics designed especially for electrodes with
cellulosic flux coatings.
The Inverarc 200 TLP also features a DC lift arc TIG mode, which includes a slope down function. The
minimum requirement to TIG weld with the Inverarc 200 TLP is a TIG torch with a gas valve. The Inverarc
can also be operated with a wired remote control, e.g., a foot control or hand control, but a remote control is
not required to TIG weld.
Summary of Contents for Inverarc 200 TLP
Page 4: ...4 Fig 1...