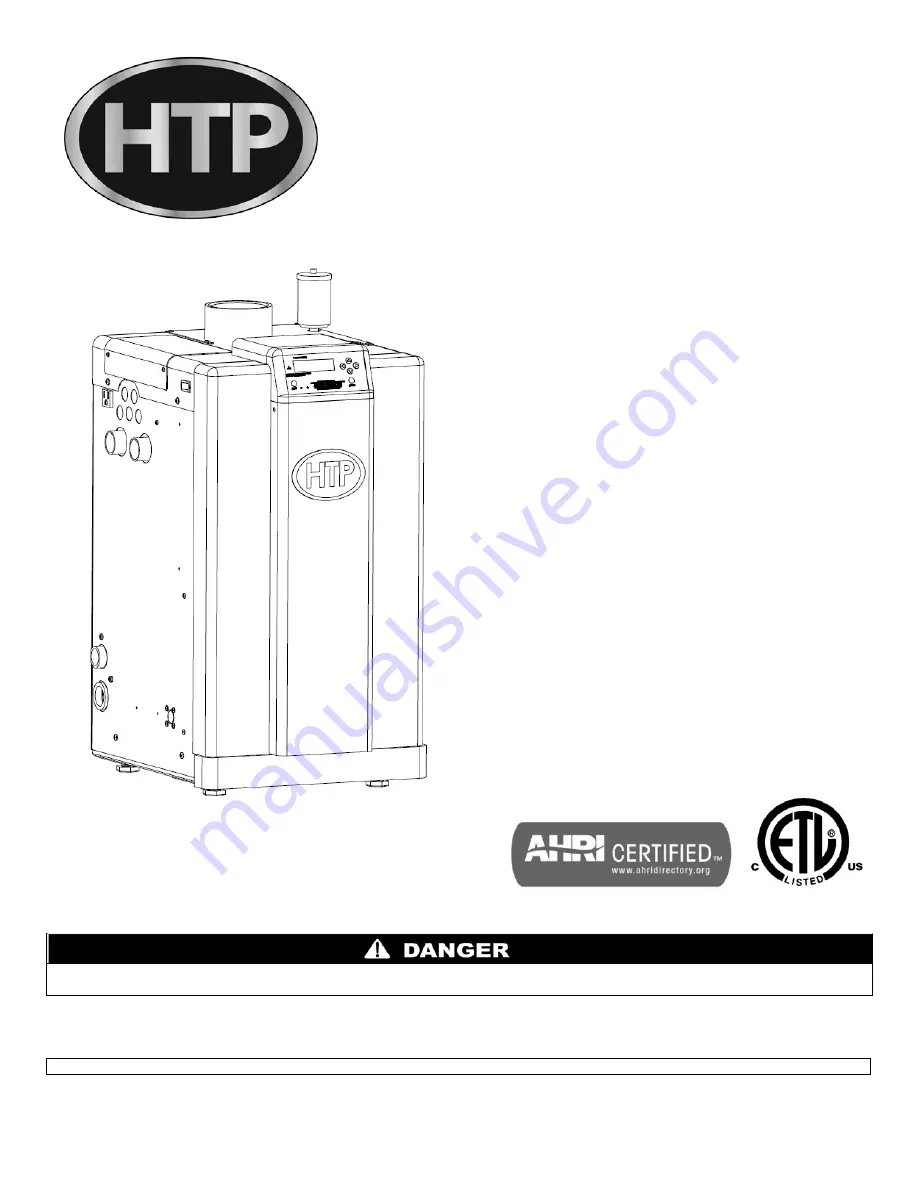
120 Braley Rd. P.O. Box 429
East Freetown, MA 02717-0429
www.htproducts.com
LP-294 REV. 9.2.14
Elite Plus
Heating Boiler
INSTALLATION
START-UP
MAINTENANCE
PARTS
Models
ELP-110 / ELP-199
Heat Exchanger Bears the ASME “H” Stamp
NOTICE: HTP reserves the right to make product changes or updates without notice and will not be held liable for typographical errors
in literature.
NOTE TO CONSUMER: PLEASE KEEP ALL INSTRUCTIONS FOR FUTURE REFERENCE.
This manual must only be used by a qualified heating installer/service technician. Read all instructions in this manual before installing.
Perform steps in the order given. Failure to comply could result in substantial property damage, severe personal injury, or death.
Summary of Contents for ELP-110
Page 48: ...48 LP 294 REV 9 2 14 Figure 27 Single or Cascade Master and Cascade Follower Controls ...
Page 49: ...49 LP 294 REV 9 2 14 Figure 28 ...
Page 76: ...76 LP 294 REV 9 2 14 Figure 32 ...
Page 77: ...77 LP 294 REV 9 2 14 Figure 33 LP 294 B ...
Page 80: ...80 LP 294 REV 9 2 14 ...
Page 81: ...81 LP 294 REV 9 2 14 ...