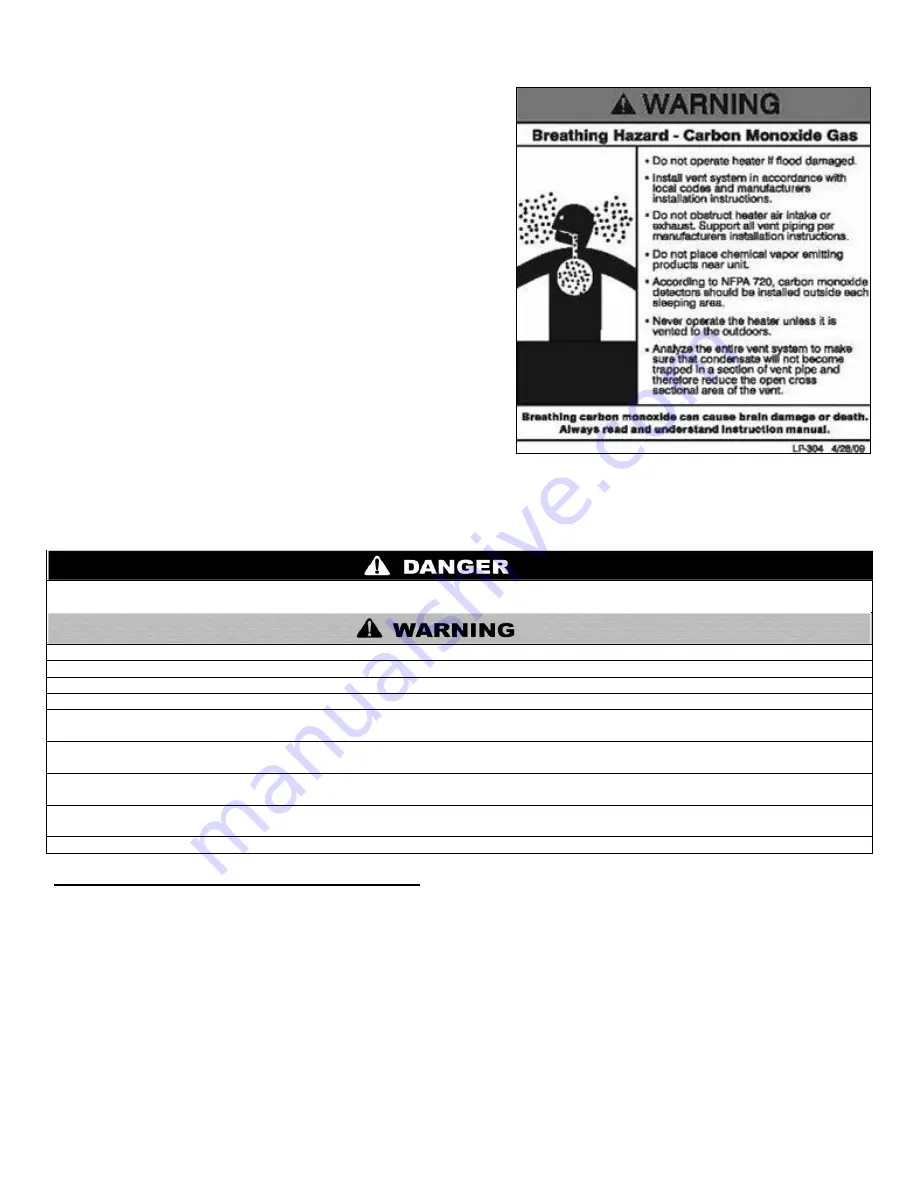
18
LP-496 REV. 11.23.15
3. If practical, close all building doors, windows and all doors between the
common venting system and other spaces in the building. Turn on clothes
dryers and any appliances not connected to the common venting system.
Turn on any exhaust fans, such as range hoods and bathroom exhausts,
at maximum speed. Do not operate a summer exhaust fan. Close all
fireplace dampers.
4. Place in operation the appliance being inspected. Follow the lighting
instructions. Adjust the thermostat so the appliance will operate
continuously.
5. Test for spillage at the draft hood relief opening after 5 minutes of main
burner operation. Use the flame of a match or candle or smoke from a
cigarette.
6. After it has been determined that each appliance remaining connected
to common venting system properly vents when tested as outlined, return
doors, windows, exhaust fans, fireplace dampers and any other gas
burning appliance to their previous condition of use.
7. Any improper operation of the common venting system should be
corrected so the installation conforms to the National Fuel Gas Code,
ANSI Z223.1. When resizing any portion of the common venting system,
the common venting system should be resized to approach the minimum
size as determined using the appropriate tables in Appendix G in the
National Fuel Gas Code, ANSI Z 223.1.
PART 5 – VENTING
Vent this appliance in accordance with these instructions. Failure to do so will result in property damage, severe personal injury, or
death.
DO NOT mix vent systems or materials unless specifically told to do so in this manual.
DO NOT thermally insulate the exhaust vent or intake pipes.
DO NOT use an electric damper, vent damper, or draft hood with this appliance.
DO NOT locate the exhaust vent or intake pipe terminations where exposed to prevailing winds.
Moisture will be produced by the exhaust vent. Take precautions when determining exhaust vent termination. Moisture may fall from the
vent termination to the ground and turn to ice in freezing conditions. Moisture or ice can produce a hazardous condition.
Exhaust condensate is acidic, and could deteriorate the surface below the exhaust vent termination. Ensure this surface is in good
repair (sealed, painted, etc.) to prevent deterioration.
Pitch the exhaust vent pipe ¼” back to the appliance. This ensures that condensate in the exhaust vent returns to the appliance and
drains properly.
For closet and alcove installations: CPVC, polypropylene, or stainless steel venting material MUST BE USED. Failure to follow this
statement could result in product damage, severe personal injury, or death.
Failure to follow these instructions could result in property damage, severe personal injury, or death.
A. INTAKE PIPE AND EXHAUST VENT GUIDELINES
1. Vent system must be installed in accordance with local codes, or, in absence of local codes, the National Fuel Gas Code, ANSI
Z223.1 / NFPA 54 and/or CSA B149.1, Natural Gas and Propane Installation Code.
2.
For installation in Canada
, installer supplied plastic vent piping must comply with CAN/CGA B149.1 and be certified to the
Standard for Type BH Gas Venting Systems, ULC-S636. Components of this listed system must not be interchanged with other vent
systems or unlisted pipes or fittings. All plastic components and specified primers and glues must be from a single system manufacturer
and must not be intermixed with another system manufacturer’s products. Clean and dry all applicable surfaces before applying
cement.
3. This appliance is designed to be installed as a direct vent (sealed combustion) type. Combustion air must be supplied directly from
the outdoors to the burner, and the flue (exhaust) gases should be vented directly to the outdoors through the wall or roof.
4. This appliance
uses 2” or 3” diameter pipe for exhaust vent and intake pipe. It is important to ensure an airtight seal from the
appliance collar to the vent terminations. See Table 9 for a list of Approved Vent Materials.
Figure 5 - CO Warning Label
Summary of Contents for EFTC-140F
Page 2: ...2 LP 496 REV 11 23 15 ...
Page 37: ...37 LP 496 REV 11 23 15 Figure 24 Electrical Wiring Diagram ...
Page 38: ...38 LP 496 REV 11 23 15 Figure 25 Ladder Diagram ...
Page 72: ...72 LP 496 REV 11 23 15 ...
Page 73: ...73 LP 496 REV 11 23 15 ...