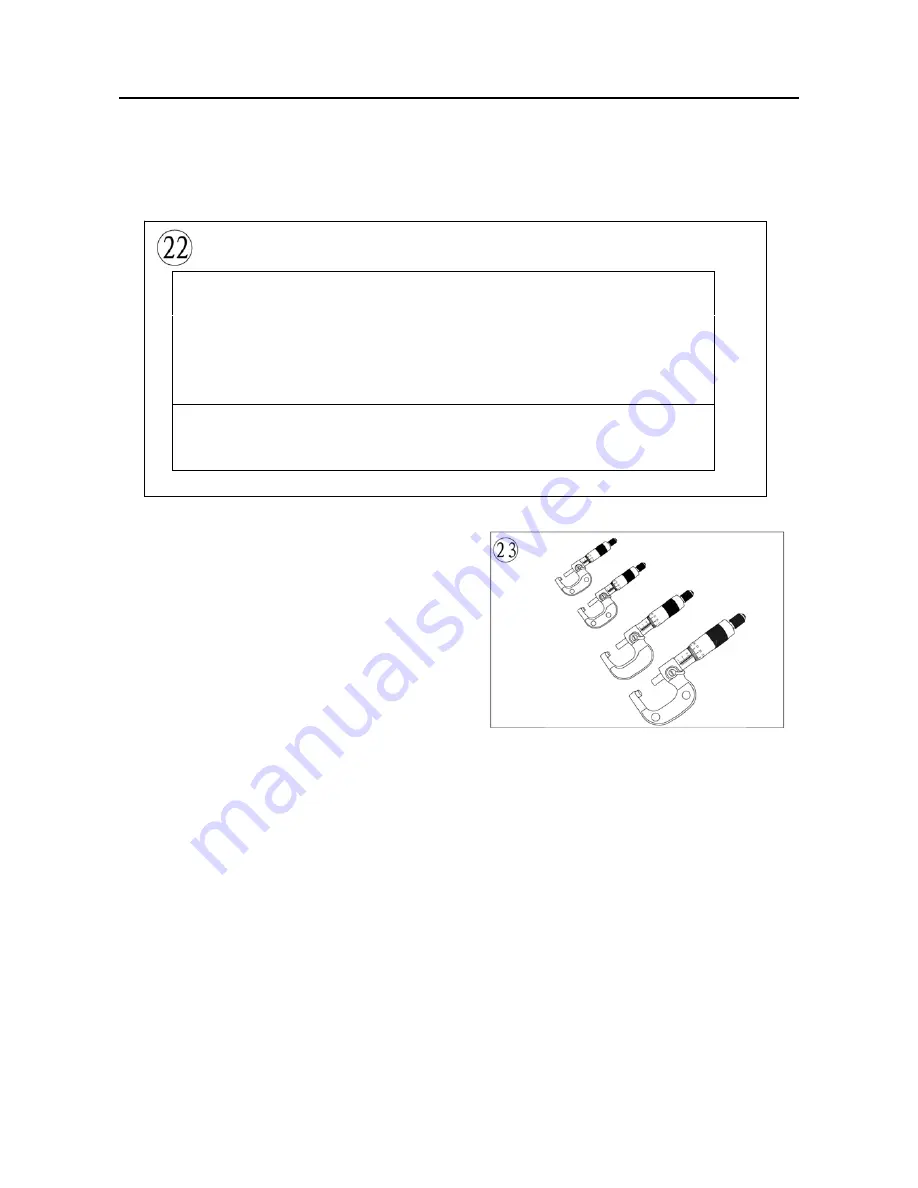
GENERAL INFORMATION
1-19
Micrometers
A micrometer is an instrument designed for linear measurement using the decimal divisions of
the inch or meter (
Figure 22
). While there are many types and styles of micrometers, most of the
procedures in this manual call for an outside
micrometer. Use the outside micrometer to measure
the outside diameter of cylindrical forms and the
thickness of materials.
A micrometer’s size indicates the minimum and
maximum size of a part that it can measure. The usual
sizes (
Figure 23
) are 0-25mm (0-1 in.), 25-50 mm (1-2
in.), 50-75 mm (2-3 in.) and 75-100 mm (3-4 in.).
Micrometers that cover a wider range of
measurements are available. These use a large frame
with interchangeable anvils of various lengths. This type of micrometer offers a cost savings, but its
overall size may make it less convenient.
When reading a micrometer, numbers are taken from different scales and added together. The
following sections describe how to adjust, care for and read the measurements of various types of
outside micrometers.
For accurate results, properly maintain the measuring surfaces of the micrometer. There cannot
be any dirt or burrs between the tool and the measured object. Never force the micrometer to close
around an object. Close the micrometer around the highest point so it can be removed with a slight
drag.
Adjustment
Before using a micrometer, check its adjustment as follows:
1. Clean the anvil and spindle faces.
2A. To check a 0-1 in. or 0-25 mm micrometer:
a. Turn the thimble until the spindle contacts the anvil. If the micrometer has a ratchet stop, use it to
ensure that the proper amount of pressure is applied.
DECIMAL PLACE VALUES*
0.1
Indicates 1/10 (one tenth of an inch or
millimeter)
0.01
Indicates 1/100 (one one-hundredth of
an inch or millimeter)
0.001
Indicates 1/1000 (one one-thousandth
of an inch or millimeter)
*This chart represents the values of figures placed to the right of the decimal point. Use
it when reading decimals from one-tenth to one one-thousandth of an inch or millimeter.
It is not a conversion chart (for example: 0.001 in. is not equal to 0.001 mm).