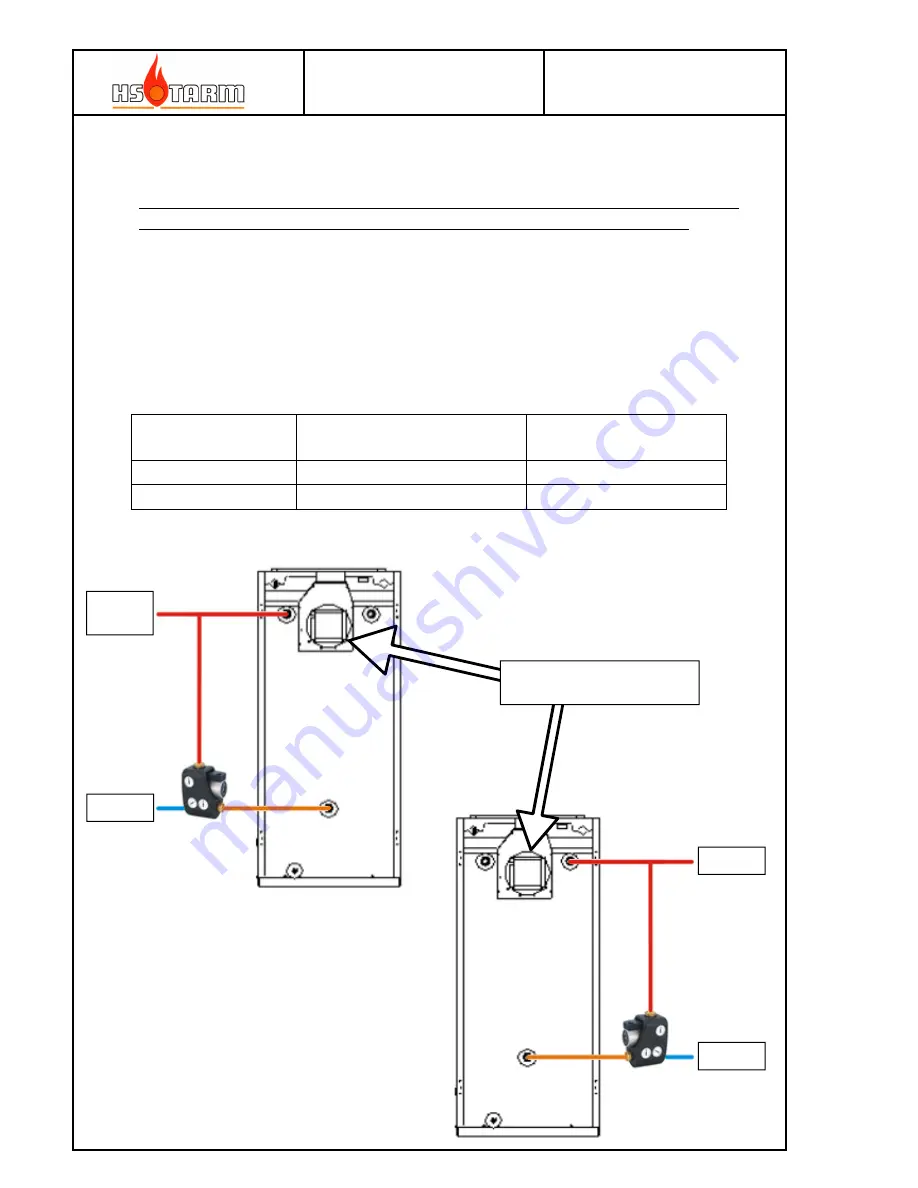
MANUAL
HK2 – HK4 25-08-2014
Page
26
3.7
Boiler connections / storage tanks
The boiler must be connected to an energy store through a recycling system having the
following function (this stipulation is obligatory in order to keep the guarantee):
-
The circulation between the boiler and the heating implements (the energy store, the
storage tank, the heating installation...) must be absent as long as the boiler has not
reached the temperature of 60°C.
-
When the circulation between the boiler and the heating implements is made, a
permanently controlled reheating to minimum 60°C is obligatory and is done by a by-pass
between the boiler flow and the return to the boiler (recycling).
Hydraulic connections to the boiler: preserve an easier access to care / maintenance
Boilers type
Minimum required useful tank
volume
Advised useful tank
volume
HK2
1250 liters
1500 liters
HK3
2250 liters
2500 liters
Flow
outlet
Return
Flow
Return
Fan cleaning / maintenance
access
Summary of Contents for HK2
Page 27: ...MANUAL HK2 HK4 25 08 2014 Page 27 3 8 Electrical connections ...
Page 33: ...MANUAL HK2 HK4 25 08 2014 Page 33 No text ...
Page 34: ...MANUAL HK2 HK4 25 08 2014 Page 34 No text ...
Page 35: ...MANUAL HK2 HK4 25 08 2014 Page 35 No text ...
Page 36: ...MANUAL HK2 HK4 25 08 2014 Page 36 Rev 02 010914 ...