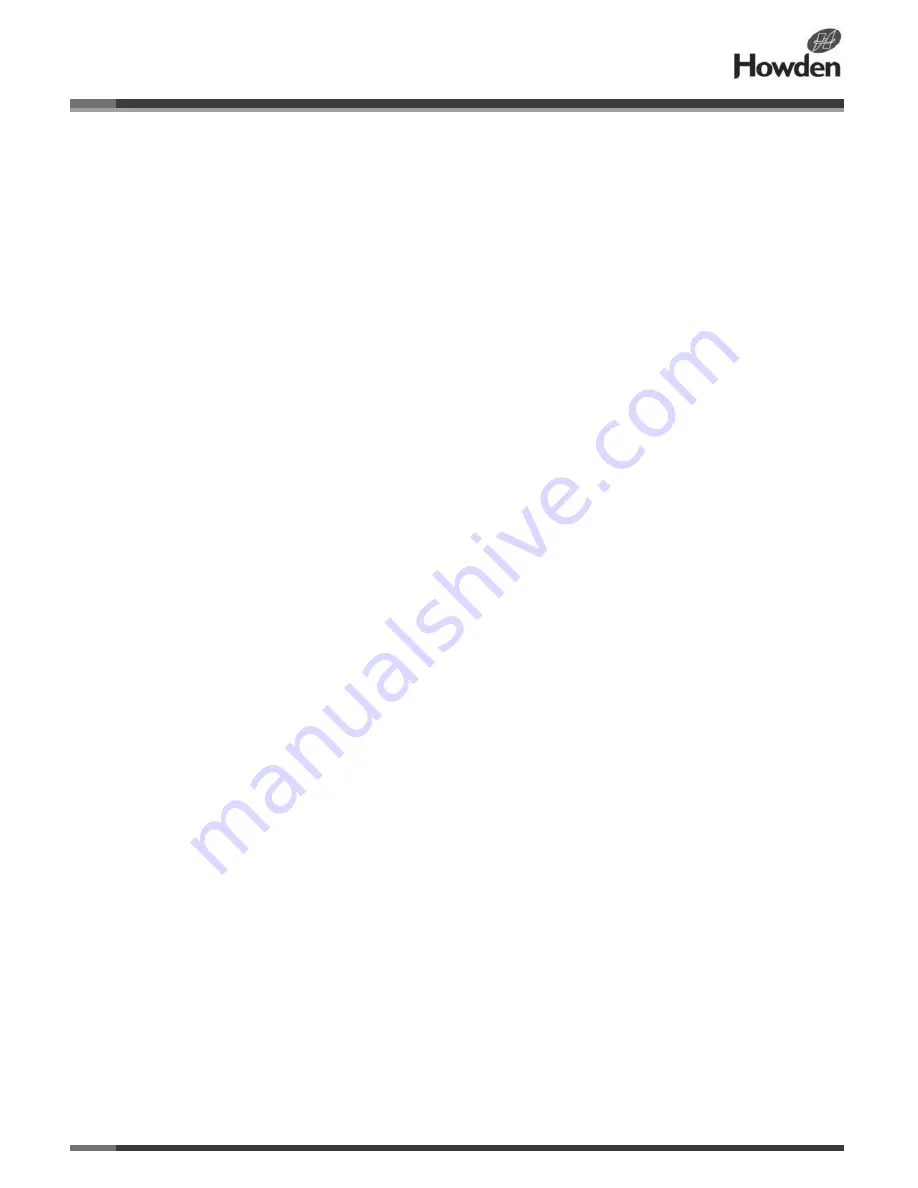
ILRB-3000 GEA20261
RAS and RAS-J WHISPAIR Blowers
Page 13 of 33
2 Start the blower and allow the oil temperature to stabilize
(approximately 1/2 hour running time).
3 Slowly begin to lower the position of the oil level switch
and mark the height at which it resets.
4 If only an oil level shutdown is to be used, continue to
lower the switch until it is 3/4 inch below the position where
the switch is reset, and lock it in place.
5 If an oil level alarm is to be used jointly with a shutdown,
lower the switch 1/2 inch below the point where the alarm
switch is reset, and lock it in place.
Lip seal oil leakage
-
A small amount of oil seal leakage
always occurs at the drive shaft seal and the headplate
seals because the unit requires this film under the lip for
proper operation. This oil should be wiped off of the blower
and base plate surfaces periodically, to prevent build-up.
Operation
Before operating a blower for the first time, thoroughly
recheck the unit installation using the following
procedure checklist as a guide. In addition, make sure
to consider any special conditions of your installation.
1 Ensure that no bolts, tools, rags, or debris have been
left in the blower air chamber or piping.
2 If you are using an outdoor intake without a filter,
ensure that the opening is clean and protected by a
strong screen. Use of a temporary protective screen at
the blower inlet as described under INSTALLATION is
strongly recommended during early operation.
3 If the installation was not performed recently, recheck
the blower leveling, drive alignment, belt tension, and
tightness of all mounting bolts.
4 Hand turn the drive shaft to make sure that the
impellers rotate without bumping or rubbing at any point.
5 Check that the blower lubrication system oil levels are
at the center of the sight glasses.
6 Check that the driver (and gear unit if supplied) is
properly lubricated. Make sure that power is available
and that all electrical overload and safety controls are
installed and workable.
7 Open the manual unloading valve in the discharge air
line. Make sure that any blocking valve in the inlet piping
is open.
8 Bump the blower a few revolutions with the driver to
ensure that the direction of rotation agrees with the
arrow near the blower shaft and to make sure that both
units coast freely to a stop.
After completing the check list items above, the blower
is ready for trial operation under “no-load” conditions.
The following procedure is suggested for this initial
operation test period.
9 Start the blower, let it accelerate to full speed, and
then shut it off. Listen for any knocking sounds, both
with the power on and also as it slows down.
10 If no problems have been noted, after the blower
comes to a complete stop, restart the unit and let it
operate for 5 to 10 minutes under no-load conditions.
Feel all of the cylinder surfaces for any hot spots
indicating impeller rubs. Continue to listen for noises
and watch for changes in vibration.
11 If all conditions are acceptable, continue operating
the unit, while gradually closing the discharge unloading
valve to replicate normal operating conditions as closely
as possible. We recommend using high-quality pressure
and vacuum gauges and thermometers in both inlet and
discharge locations to measure pressure and
temperature rises across the blower. Observe the
pressure increase as the unloading valve is closed, and
do not allow it to exceed the rating of the specific blower
as listed under LIMITATIONS.
12 If all conditions remain satisfactory, continue the run
for about one hour. Observe the pressure and
temperature rise periodically to make sure neither
exceeds the specified limits. Continue to check for
noises and hot spots, and observe oil level behaviour at
the three sumps.
If trouble appears, refer to the TROUBLESHOOTING
CHECKLIST for suggested remedies. The blower
should now be ready for continuous duty under full load.
During the first several days, periodically verify that all
conditions remain reasonably steady and within limits.
These checks may be especially important if the unit is
part of a process system where conditions may vary. At
the first opportunity, stop the blower and clean or
remove the temporary inlet protective screen. If no
appreciable amount of debris has collected, the screen
may be removed. See comments under
INSTALLATION. Also, verify levelling, coupling
alignment or belt tension, and anchor bolt tightness.
If operating experience indicates that the blower’s
capacity is a little too high for the actual requirements, a
small excess may be blown off continuously through the
manual unloading or vent valve. Never rely on the
pressure relief valve as an automatic vent because it
may cause the discharge pressure to become
excessive, and can also result in valve failure. If the
blower capacity is too low, refer to the
TROUBLESHOOTING CHECKLIST before contacting
the nearest
Howden Roots
sales office for
recommendations.
ILRB-3000 GEA20261 RAS and RAS-J WHISPAIR Blowers.pdf 13
03/09/2015 13:21:26
Summary of Contents for Roots RAS Whispair
Page 5: ...ILRB 3000 GEA20261 RAS and RAS J WHISPAIR Blowers Page 5 of 33 ...
Page 16: ...ILRB 3000 GEA20261 RAS and RAS J WHISPAIR Blowers Page 16 of 33 ...
Page 23: ...ILRB 3000 GEA20261 RAS and RAS J WHISPAIR Blowers Page 23 of 33 ...
Page 25: ...ILRB 3000 GEA20261 RAS and RAS J WHISPAIR Blowers Page 25 of 33 ...
Page 27: ...ILRB 3000 GEA20261 RAS and RAS J WHISPAIR Blowers Page 27 of 33 ...
Page 28: ...ILRB 3000 GEA20261 RAS and RAS J WHISPAIR Blowers Page 28 of 33 ...
Page 29: ...ILRB 3000 GEA20261 RAS and RAS J WHISPAIR Blowers Page 29 of 33 ...
Page 30: ...ILRB 3000 GEA20261 RAS and RAS J WHISPAIR Blowers Page 30 of 33 ...
Page 31: ...ILRB 3000 GEA20261 RAS and RAS J WHISPAIR Blowers Page 31 of 33 ...
Page 32: ...ILRB 3000 GEA20261 RAS and RAS J WHISPAIR Blowers Page 32 of 33 ...