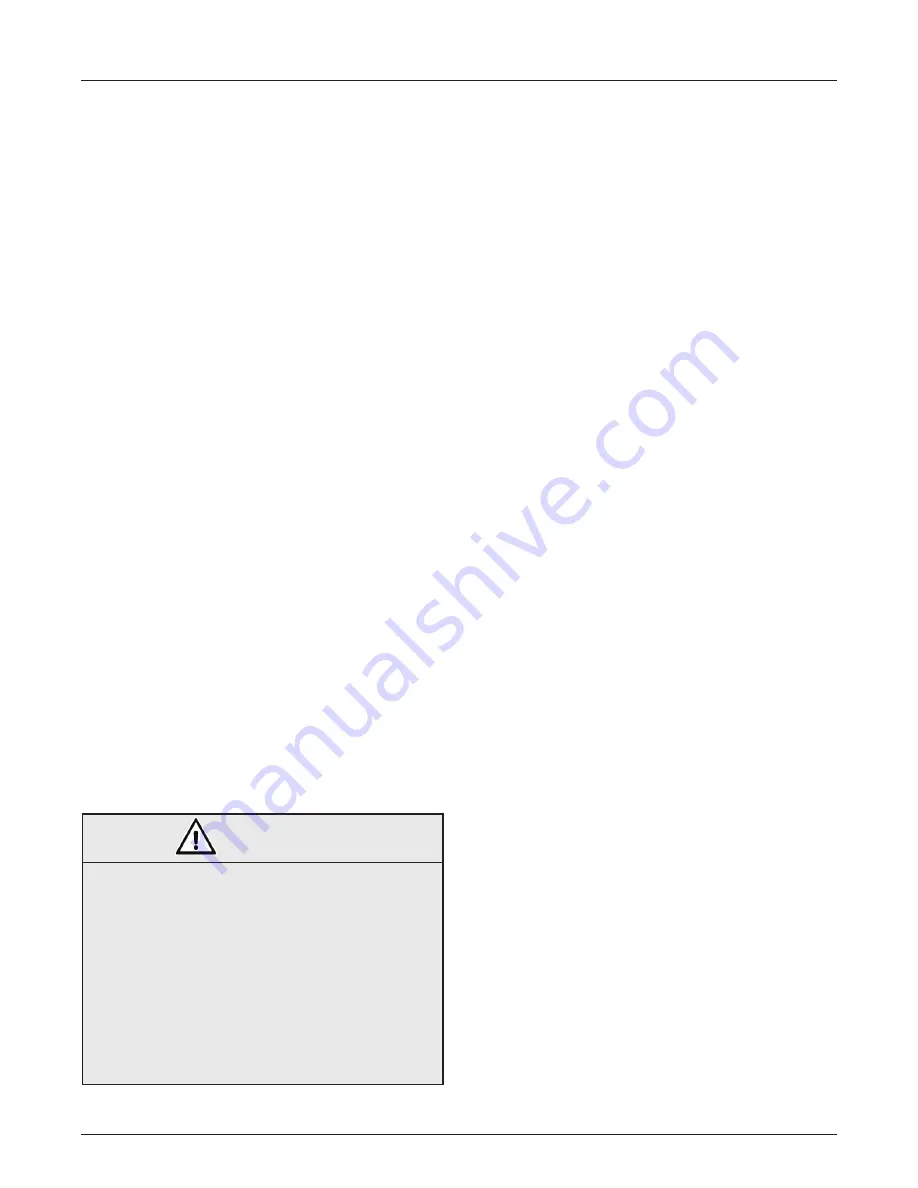
Document 2.4.128, Revision 3
October, 2017
18
Network Transformer Instruction Manual
Some of the accessory devices described below are
optional and may not be present in any particular
transformer design. The inclusion of particular
accessory device in any transformer design is
governed by industry standards and by individual
user specifications.
Diagrammatic Nameplate
The transformer nameplate is supplied on each
transformer and provides a circuit diagram and
certain physical and electrical information in
accordance with IEEE Standard C57.12.00.
Fluid Level Gauge
Fluid level gauges are magnetic dial-type devices
that indicate internal fluid levels. One gauge is
welded to the transformer main tank above the
primary terminal chamber at the 25°C fluid level. A
second gauge is welded on the side of the primary
switch chamber at the 25°C fluid level.
If a gauge reads “LOW,” the cause of the low reading
should be investigated and corrected. A low fluid
level in the main tank could cause overheating of the
transformer and could compromise the insulation
system. A low fluid level in the primary switch
chamber could compromise the insulation system of
the primary switch.
Fluid level gauges can be supplied with optional
switch contacts, which can be used to provide a
remote indication of low fluid level.
WARNING
FAILURE TO FOLLOW THE INSTRUCTIONS
BELOW COULD RESULT IN DEATH
OR SERIOUS PERSONAL INJURY AND
MAY ALSO RESULT IN DAMAGE TO THE
EQUIPMENT.
• Do not energize the transformer if the
fluid level is low.
• Maintain proper fluid level while the
transformer is energized.
Fluid Temperature Gauge
The fluid temperature gauge is a dial-type bi-metal
device that indicates the fluid temperature at
the top of the fluid column in the main tank. The
temperature gauge is mounted above the primary
terminal chamber in a dry leak-proof well, permitting
removal of the gauge without exposure to the tank
fluid.
The gauge is furnished with a red drag-hand pointer
that indicates the maximum temperature measured.
The drag-hand can be reset by rotating the magnet
at the center of the dial or, on some types, by
pressing a reset button. Fluid temperature gauges
may also be supplied with switch contacts, which can
be used to provide a remote indication of low or high
temperature.
During normal operation the fluid temperature
gauge should read less than the sum of the ambient
temperature and the rated temperature rise
(normally 85°C). Refer to IEEE Standard C57.91 for
loading recommendations.
Filler Plug and Upper Filter Press Connection
The filler plug and upper filter press connection is
located on the main tank cover, consisting of 1-inch
NPT opening with protective plug.
Combination Drain and Bottom Filter Valve
The combination drain and bottom filter valve is
provided to permit draining, filtering and sampling of
the insulating fluid for testing purposes. Two valves
are typically provided, one located on the main
transformer tank and another on the primary switch
chamber. Refer to
“Sampling and Testing the Fluid,”
“Removing or Lowering the Fluid,”
and
“Filling with
Fluid”
for instructions.
Terminal Chamber Vent and Level Plug
The terminal chamber vent and level plug is located
on the terminal chamber cover at the 25
°
C fluid
(or compound) level, which can be used to vent the
chamber and check the fluid (or compound) level.
SECTION 6: ACCESSORIES