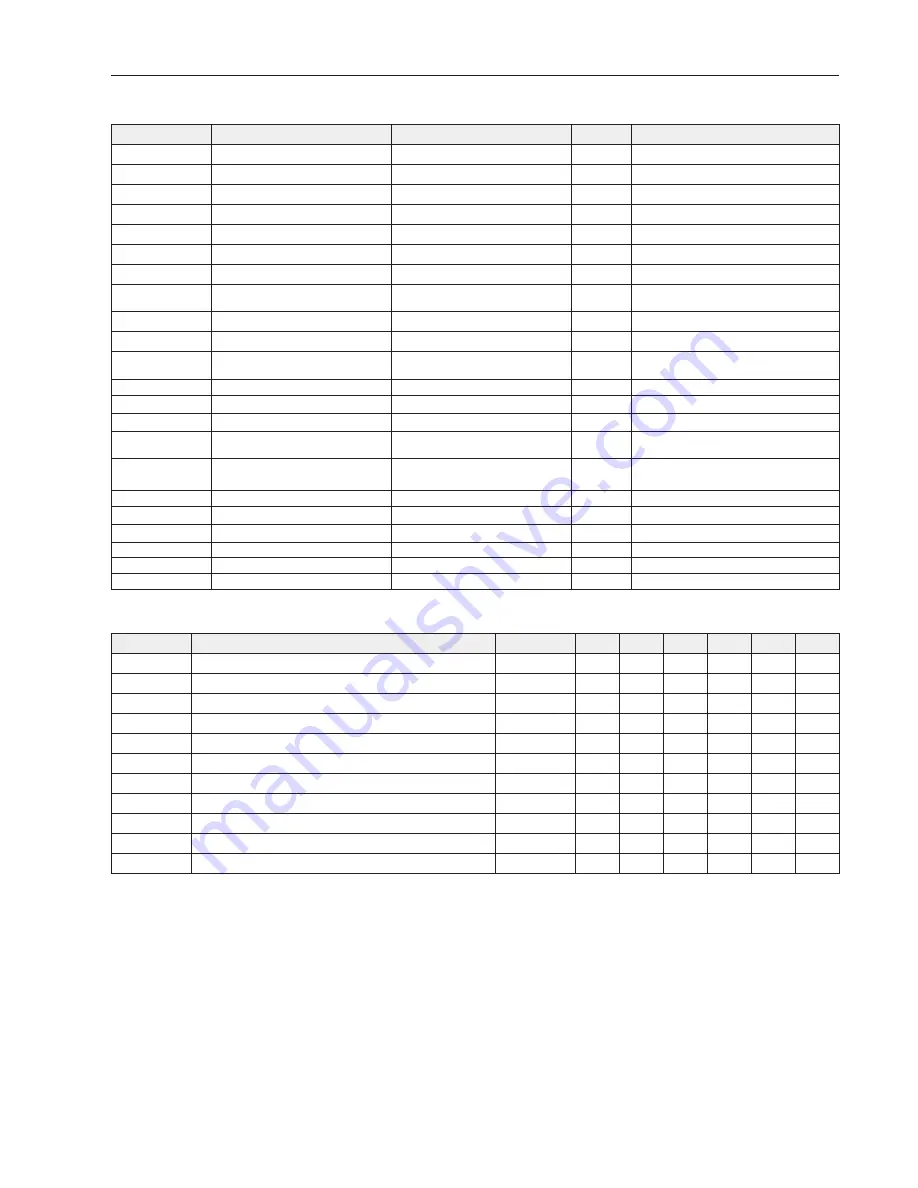
35
4 205 116 / 02
Overview of settings
FAULT REPORTING OVERVIEW TopTronic
®
T
Status
Designation
Fault type
Code
Remark
Logical
Boiler temperature
Not reached (90 min)
50-4
Logical
Tank temperature
Not reached (4 h)
51-4
Logical
Flow temperature MC1
Not reached (1 h)
52-4
Logical
Flow temperature MC2
Not reached (1 h)
53-4
Logical
Room temperature HC
Not reached (3 h)
54-4
Logical
Room temperature MC1
Not reached (3 h)
55-4
Logical
Room temperature MC2
Not reached (3 h)
56-4
System
Lock by energy supply company
ST 2
Address collision
70-0
System
Activity
No T2B signal
70-1
System
Activity
No FA signal
70-6
System
Activity
Regulator with address 10 is
missing
70-8
System
Activity
Data bus error
70-9
No Hoval regulator
System
HP return sensor
Return min. temp. below setpoint
85-4
System
HP return sensor
Return max. temp. exceeded
85-5
System
QF
Heat source min. temp. below
setpoint
86-4
System
QF
Heat source max. temp. exceeded
(cooling operation)
86-5
System
QF
Fault heat source sensor
--
Standard signal «VE-x»
System
WPS
Variable input HP fault
87-7
System
Pulse counter
No pulse (5 min)
90-0
System
Fault
Warning
W:XX
Warning in automatic fi ring device
System
Fault
Lock-out
E:XX
Fault in automatic fi ring device
System
Fault
Blocking
B:XX
Fault in automatic fi ring device
SENSOR ALLOC.
Par.
Designation
Factory
10
20
30
40
50
Lev.
1
Balancing external sensor
0
OEM
RS-T
Balancing room sensor (only adjustable with RS-T)
0
HF
2
Balancing heat generator
0
OEM
3
Balancing tank sensor
0
OEM
4
Balancing fl ow sensor 1
0
OEM
5
Balancing fl ow sensor 2
0
OEM
6
Balancing solar collector sensor
0
OEM
7
Balancing solar buffer sensor
0
OEM
8
Balancing variable input 1
0
OEM
9
Balancing variable input 2
0
OEM
10
Balancing variable input 3
0
OEM