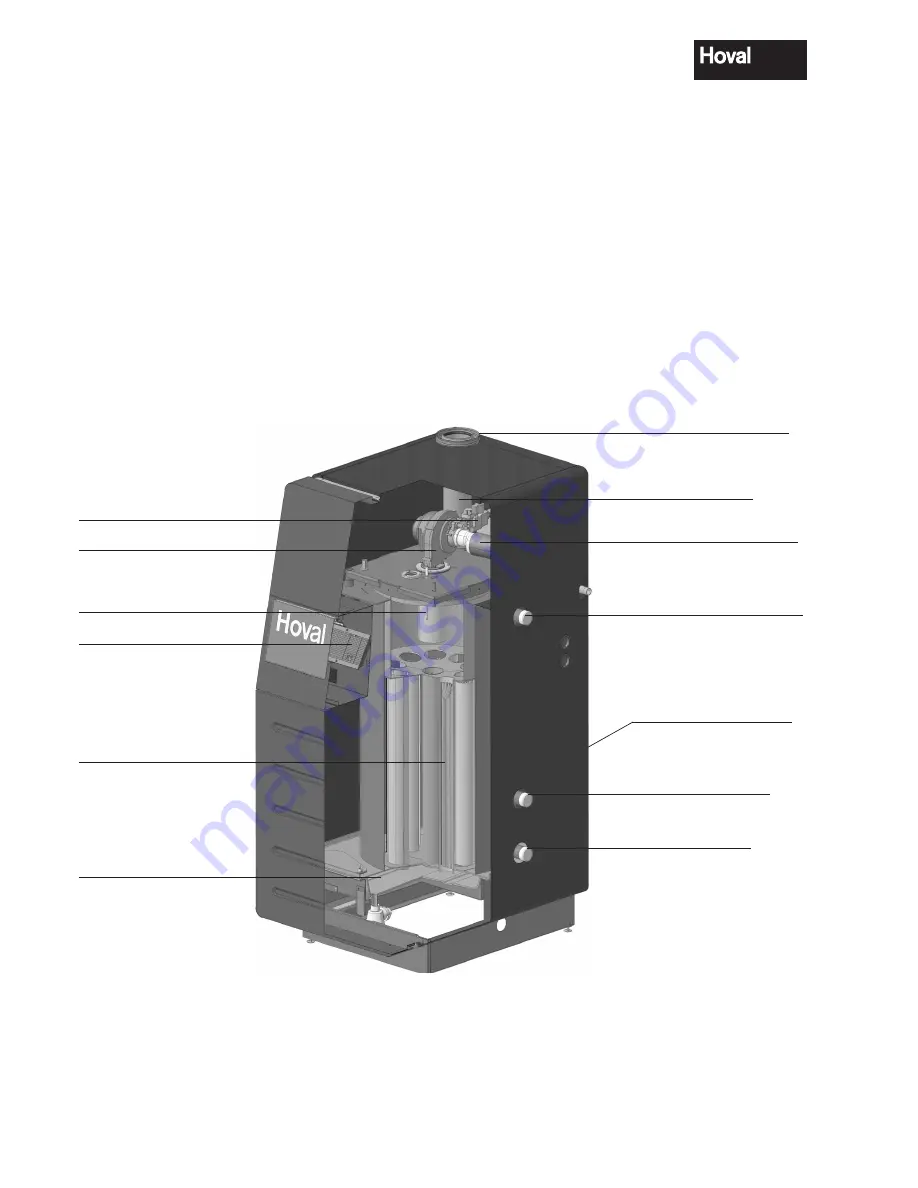
4 210 266 / 03
8
Technical data
4.
Technical data
4.1 Description of the boiler
The Hoval UltraGas
®
is a low emission, energy-saving
condensing gas boiler comprising the Ultraclean
burner system, a gas fired premix burner with com-
bustion air fan. The Hoval UltraGas
®
has a vertically
disposed combustion chamber of stainless steel as
a primary heating surface and a secondary heat-
ing surface of a corrosion resistant aluminium alloy.
The secondary heating surface is designed so that
part of the water vapour contained in the flue gas is
condensed and the vaporisation heat it contains is
utilised for the heating circuit. The gas burner is in the
form of a break draught burner, which can easily be
swung up for maintenance purposes. The UltraGas
®
is designed to operate with natural and liquid gas. The
figure below shows the design principle.
Concentric flue gas connection
Connection hose for room sealed
operation
Feed tube on left and/or right side
Internal flue gas conduit
High temperature return on
left and/or right side
Low temperature return
on left and/or right side
Gas safety and
control devices
Combustion air fan
Electrode for ignition and
flame monitoring
TopTronic
®
T controller
aluFer
®
heat exchanger
Condensate collection tray
Horizional flue gas pipe optional