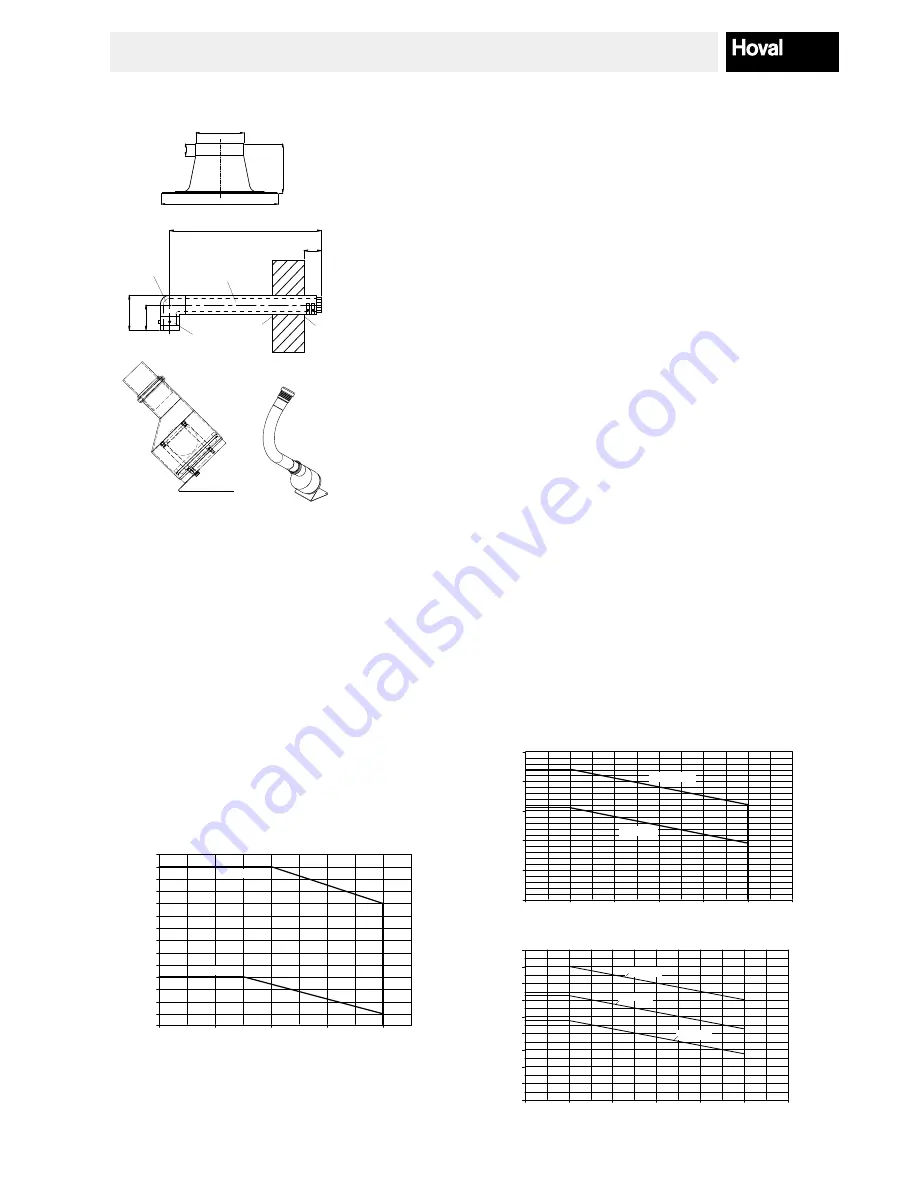
47
TopGas Cascade
60 - 720 kW
4215256-00 - 11/16
Ø100
Ø150
1095
1135
102
152
11
0
Ø100
Ø150
152
102
990 / 490 / 240
1000 / 500 / 250
Ø100
Ø150
Ø102 Ø152
90
95
100
45°
125
135
Ø102 Ø152
93°
125
150
Ø150
1230
Ø100
Ø150
680
1180
1290
200
160
22° - 45°
390
40
Ø160
165
Ø102
Ø152
215
Ø100
Ø150
152
102
Ø100
Ø150
152
102
Ø100
Ø150
490
500
240
250
Ø100
Ø100
Ø150
Ø100
11
5
240
140
1220 max
195
275
Wall
plate
Wall
plate
Wall
terminal
93 degree
bend
Vertical
adaptor
Ø100
Ø150
1095
1135
102
152
11
0
Ø100
Ø150
152
102
990 / 490 / 240
1000 / 500 / 250
Ø100
Ø150
Ø102 Ø152
90
95
100
45°
125
135
Ø102 Ø152
93°
125
150
Ø150
1230
Ø100
Ø150
680
1180
1290
200
160
22° - 45°
390
40
Ø160
165
Ø102
Ø152
215
Ø100
Ø150
152
102
Ø100
Ø150
152
102
Ø100
Ø150
490
500
240
250
Ø100
Ø100
Ø150
Ø100
11
5
240
140
1220 max
195
275
Wall
plate
Wall
plate
Wall
terminal
93 degree
bend
Vertical
adaptor
8.11 Aluminium flat roof flashing
2042 413
8.12 100/150 Wall terminal kit (for horizontal discharge)
Comprises of vertical adaptor, 93 degree elbow 2 wall plates and
a horizontal wall terminal. Max dimension can be extended by
use of extension pieces.
2042 405
All items finished white RAL 9016
Flue design (TopGas
®
60-120)
• An adapter with sample points must be used (fitted to the boiler flue outlet connection).
• The flue gas is very cool and saturated with moisture so there will be very little or no buoyancy to pull the gases up the chimney.
• The burner fan assists with the evacuation of the flue gases so there may be slight pressurisation of the flue.
• It is permissible for the condensate from the flue system to drain back through the boiler.
• Horizontal flue sections must be inclined back to the boiler (3
°
minimum) to prevent condensate remaining in the flue.
• Flues must be designed to meet all current regulations / standards.
• See Technical data section for flue gas mass flow rates, temperatures, usable fan overpressure and ventilation requirements.
• The tables below are for guidance only.
Maximum flue lengths (TopGas
®
35-60)
100/150 PP concentric flue (horizontal discharge)
-
-
21
22
23
24
25
26
27
28
29
30
31
32
33
0
1
2
3
4
0
5
10
15
20
25
0
1
2
3
4
5
6
20
19
0
2
4
6
8
10
12
14
16
18
0
1
2
3
4
5
6
Horizontal flue gas pipe length (m)
Max flue height (m)
TopGas 60
TopGas 35
TopGas 45
TopGas 60
TopGas 35-45
Horizontal flue gas pipe length (m)
Max flue height (m)
Horizontal flue gas pipe length (m)
Max flue height (m)
TopGas 35-45
TopGas 60
-
-
21
22
23
24
25
26
27
28
29
30
31
32
33
0
1
2
3
4
0
5
10
15
20
25
0
1
2
3
4
5
6
20
19
0
2
4
6
8
10
12
14
16
18
0
1
2
3
4
5
6
Horizontal flue gas pipe length (m)
Max flue height (m)
TopGas 60
TopGas 35
TopGas 45
TopGas 60
TopGas 35-45
Horizontal flue gas pipe length (m)
Max flue height (m)
Horizontal flue gas pipe length (m)
Max flue height (m)
TopGas 35-45
TopGas 60
-
-
21
22
23
24
25
26
27
28
29
30
31
32
33
0
1
2
3
4
0
5
10
15
20
25
0
1
2
3
4
5
6
20
19
0
2
4
6
8
10
12
14
16
18
0
1
2
3
4
5
6
Horizontal flue gas pipe length (m)
Max flue height (m)
TopGas 60
TopGas 35
TopGas 45
TopGas 60
TopGas 35-45
Horizontal flue gas pipe length (m)
Max flue height (m)
Horizontal flue gas pipe length (m)
Max flue height (m)
TopGas 35-45
TopGas 60
100 PP flue (in chimney stack, provision for
room air is required)
100/150 PP concentric flue (in chimney stack)
The above figures include for one 93 degree bend.
Additional 93 degree bends will have the effect of
reducing the length by 2.5 metres and 45 degree bends
will reduce the length by 1.5 metres. The flue lengths
stated will have no effect on the boiler output.
Where the boiler cascade takes its air supply directly from the plant room, it is possible to combine one or more TopGas boilers into
a common flue duct, where each boiler within the cascade is connected to a common duct or ducts via an individual flue connection
piece complete with a non-return flap or damper. In this case all boilers should be provided with an optional air inlet non-return flap
(available as an accessory for the TopGas 60-120 as above) or with an external non-return flap for the TopGas 35 and 45 (not Hoval
supply).
8.13 Air inlet non-return damper for TopGas
®
(60-120) only
Fitted inside the boiler casing to prevent back flow of flue gases
through an off-line cascade boiler. Cannot be used with models
35 and 45.
6036 265