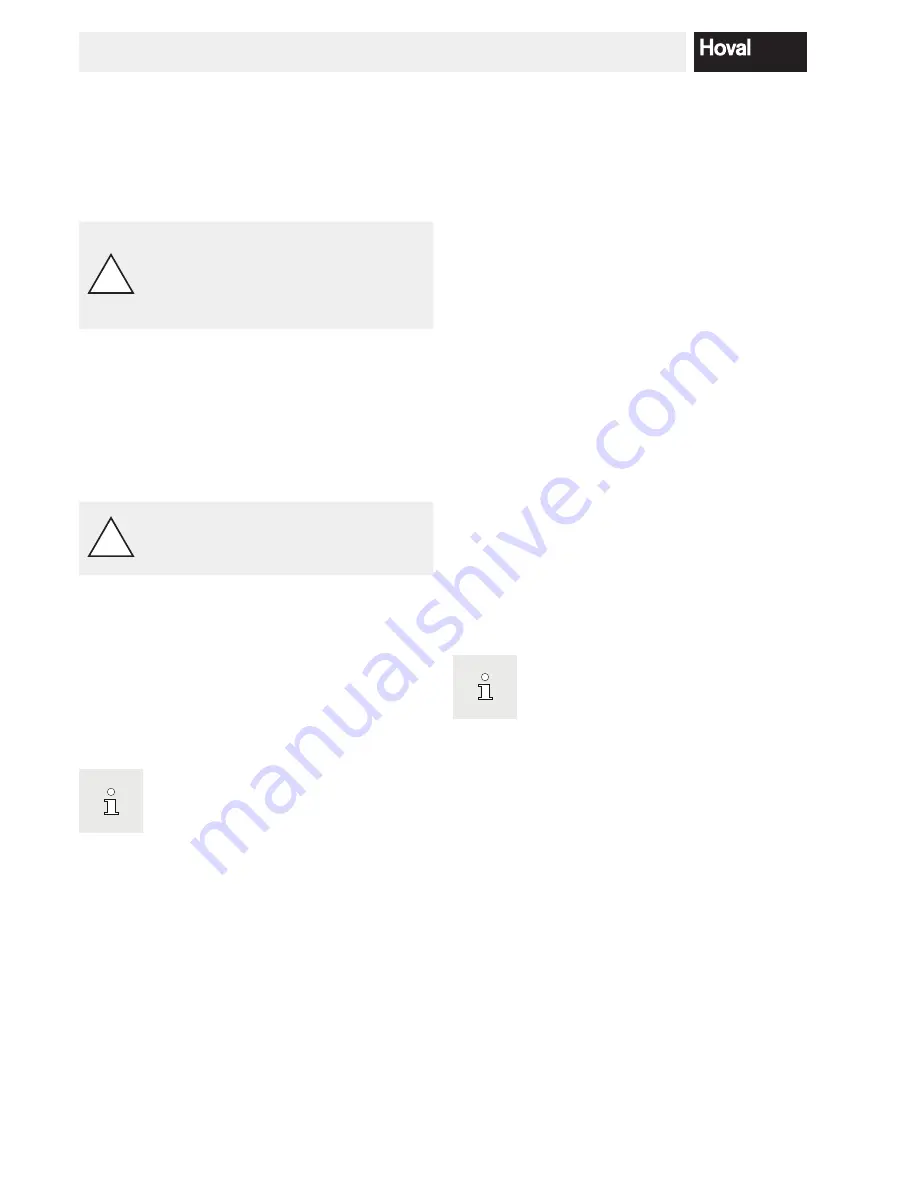
28
4 213 893 / 01
COMMISSIONING
d) Measurement of NOx and CO content. The measured
values must meet the limiting values prescribed by
the regulations. Values exceeding these reference
values are an indication of faulty burner setting, gas
burner or heat exchanger contamination or gas burn-
er defect.
!
WARNING
If the limiting values prescribed by the regu-
lations are exceeded, the boiler must be
put out of operation and the corresponding
meas ures for repair work must be initiated.
After a correction it is necessary to achieve the upper and
lower value again for a control/correction.
The boiler is now correctly set. To revert to normal opera-
tion, press the „RESET“-key.
5.5
Changing to a different kind of gas
!
WARNING
Changes are only to be carried out by a rec-
og nised specialist!
The boiler is set to natural gas H at the factory (Wobbe
fac tor 15,0 kWh/m
3
).
Changeover from natural gas H to natural gas L
The changeover to a low caloric natural gas is simple.
Only a check or correction of the CO
2
(O
2
) value at max.
and min. output must be carried out (see chapter 5.4.4).
Changeover from natural gas H to propane liquid gas
Compliance with the special local provisions
(VKF/DVGW/ÖVGW) for operating a boiler on
liquid gas is imperative in each case.
Ensure that the fuel type in the measuring de-
vice has been set correctly!
The propane liquid gas conversion kit comprises:
- 1 yellow sticker “Changed too the set gas type:
Liquid gas“ for the boiler rating plate
-
1 gas pressure deflector „Liquid gas“
A) With an already connected boiler:
- Close the gas shut-off valve
-
Place the system deflector in the operating pan el
to “0“
B) Take off the boiler hood
C) Remove the gas pressure deflector „Natural gas“ and
install the new gas pressure deflector „Liquid gas“.
Wire up the gas pressure deflector (AMP connector
at position 1 and 3).
D) Affix the yellow sticker „change to the set gas type:
Liquid gas“ to the boiler rating plate.
E) with boiler already connected:
- open the gas valve
-
place the system deflector to „I“
F) Set the CO
2
(O
2
)-content according to chapter 5.4.5 at
rat ed and minimum output to CO
2
= 9,9 - 10,2 (O
2
=
5,9 - 5,5) Vol.-% (dry).
5.6
Handing over to the user
5.6.1 Instruction the user
Obtain from the user a written confirmation that
- he has received adequate instruction in the correct op-
erating and maintenance of the system,
- he has received and read the operating and mainte-
nance instructions, plus additional documents concern
-
ing the burner, heating controller etc.,
-
and is consequently sufficiently familiar with the system.
A pre-printed form (in duplicate) for this confirmation is to
be found on last page of these installation instructions.
Also available on request for flow with the boiler are cop
-
ies of the official description for submission to the super
-
visory authorities or for obtaining a permit from the local
technical inspectorate.
The operating instructions and technical in-
formation are always to be kept in the boiler
installation room.
5.6.2 Checking the water level
The customer should be informed of the values between
which the movable pointer on the pressure gauge may
alternate. Refilling and bleeding the air from the system
are to be demonstrated.
5.6.3 Maintenance
On hand-over the customer is to be informed that check-
ing and cleaning of the gas firing is to be carried out at
regular intervals – normally at least once per year- by the
licensed installer or the responsible after-sales organisa-
tion. The conclusion of a maintenance agreement is also
important for economical operation in the sense of the
energy-saving laws and by a permanently correct burner
setting avoids complaints with the statutory inspection of
flue gas loss and pollutant emissions.
Summary of Contents for TopGas 35
Page 35: ...35 4 213 893 01 ...