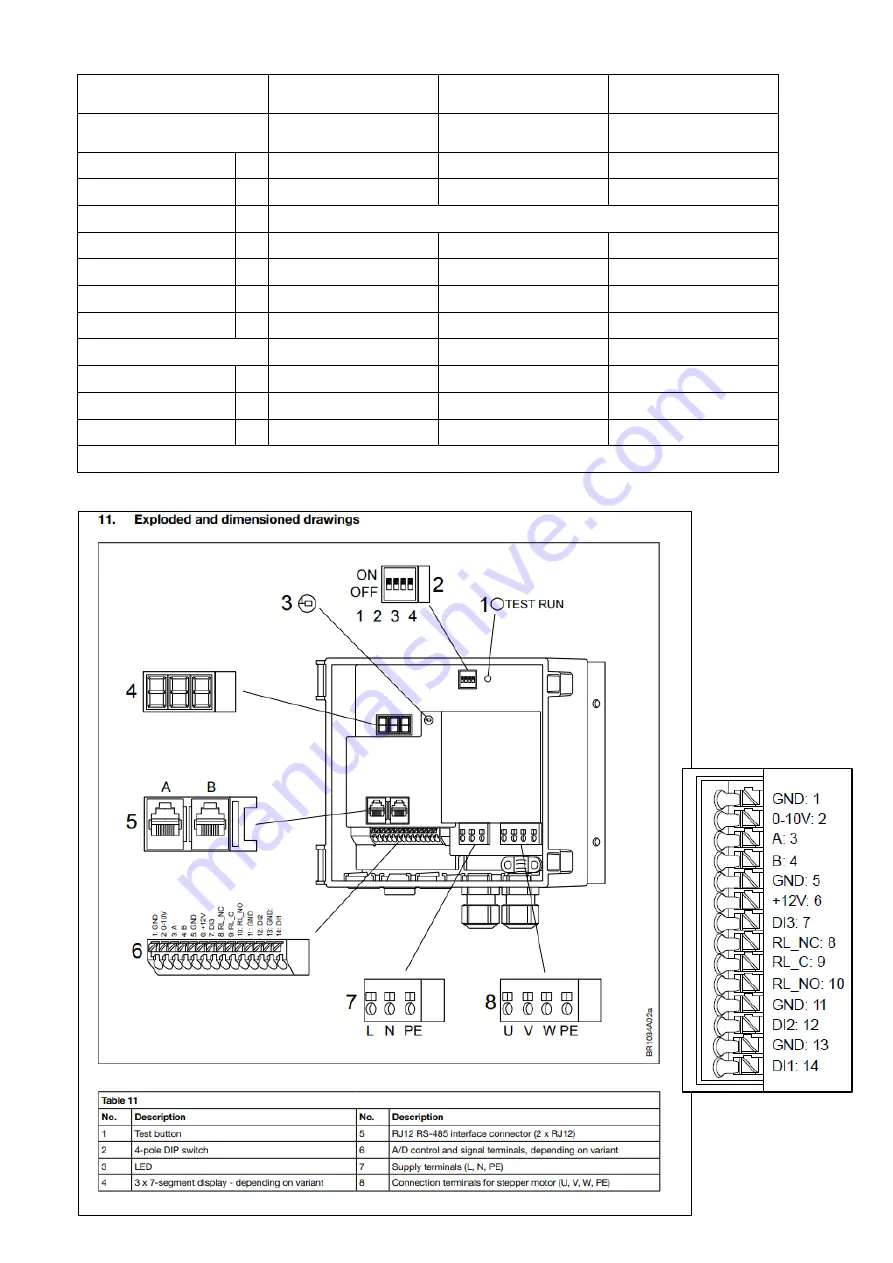
2
Technical data
Motor MRHX-3P0xN-03C5
MRHX-02N
MRHX-04N
MRHX-08N*
Control unit
DRHX-1055 MAD5
DRHX-1220 MAD5
DRHX-1220 MAD5
Max Torque
Nm
2
4
8
*
Input Signal
V
0-10
0-10
0-10
Output Rpm 50Hz
150 / 170 / 200 / 400* rpm
Voltage Input 50/60Hz
V
1x230
1x230
1x230
Motor voltage
V
3x0-200 V AC
3x0-200 V AC
3x0-200 V AC
Motor power
kW
0,055
0,110
0,220
Rated current
A
0,6
2,4
2,4
Class of protection
IP54
IP54
IP54
Weight
motor
kg
2,4
3,5
5
Weight
controller
kg
0,9
0,9
0,9
Shaft Ø
(motor)
mm
12
12
12
*
8 Nm torque at max. 250 motor rpm
–
but only max. 5 Nm torque at max. 400 motor rpm
6.