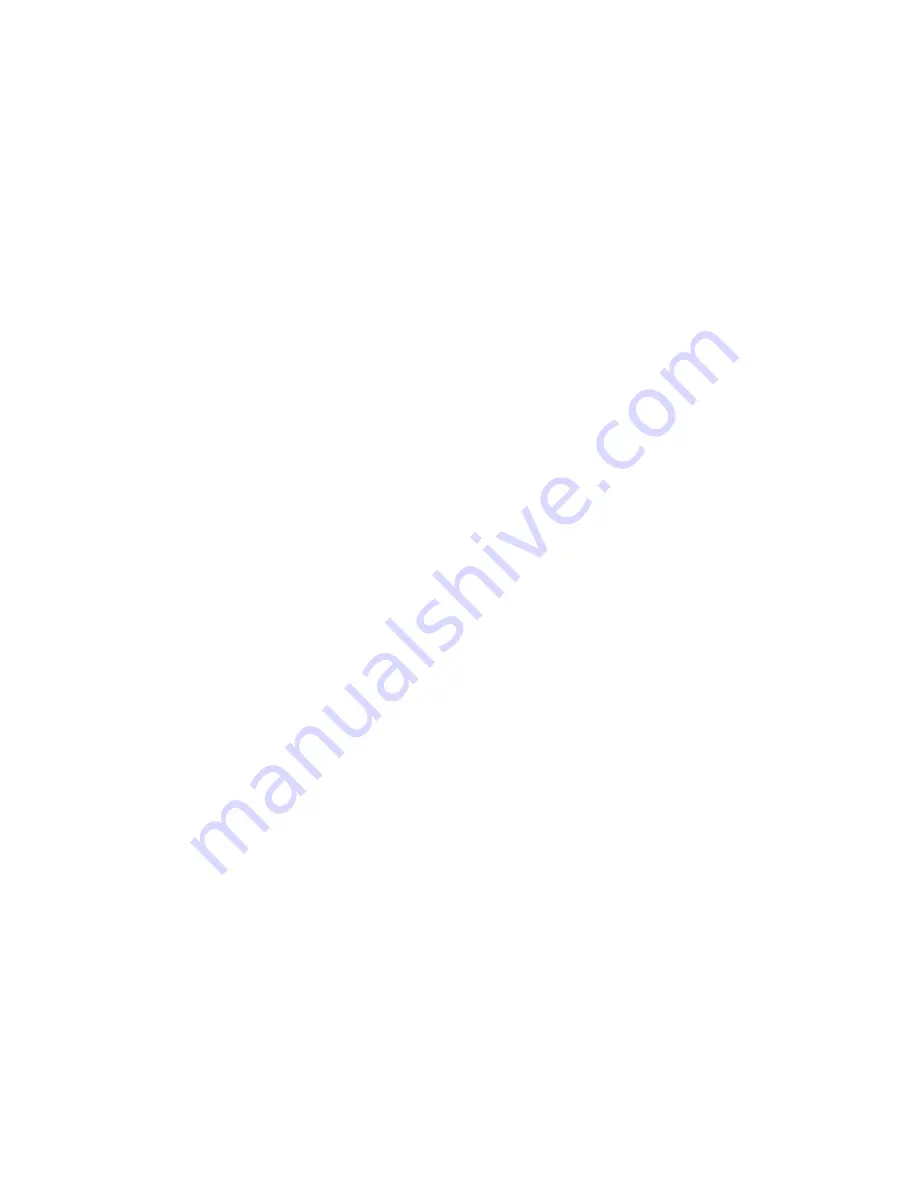
8
GLIDE POST ADJUSTMENT
Two glide posts are utilized. Post nearest edge of magnet
should make initial contact and be set according to
instructions. Second glide post setting should be located
1/16” to 1/8” above the other glide post.
1. Adjustment is made with Magnet ON and glide post
over the work surface.
2. Remove the Lock Screw (10979)
3. Screw Glide Post (10644) up until the bottom of the
body is about 1/4-inch above the work surface.
4. Place a .040” shim between end of Glide Post and the
work surface.
5. Screw Glide Post down, compressing plunger until the
body of the glide post rests on the shim.
6. Install Lock Screw using 242 Loctite (if available)
REPLACING ARBOR and/or
ARBOR SUPPORT BRACKET
1. Remove arbor assembly as described above.
2. Remove the top retaining clip from the arbor and slide
the inducer ring and thrust washers off the end of the
arbor.
3. Remove the bottom inducer retaining ring clip
(40302) from the arbor. Remove the ejector collar
retaining ring (40398) and slide the old arbor out of the
support bracket.
4. Slide new arbor assembly through arbor support
bracket with one thrust washer (40234) on top and
another underneath the support bracket. The retaining
ring (40398) is installed above the top thrust washer.
5. Put one retaining clip on the new arbor and slide it
down about 3/4” past the bottom groove.
6. Slide the inducer ring onto the arbor with a thrust
washer on each side. Inducer ring must be below the
arbor retaining set screw.
7. Install the other retaining clip into the top groove.
INSTALLING ARBOR ASSEMBLY
1. Slide arbor completely onto spindle so that the spindle
key is fully engaged into the arbor slot and the top of the
arbor rest firmly on the shoulder of the spindle.
2. Tighten arbor mounting set screw.
3. Replace front support bracket with spacers set for
proper depth of cut.
4. Feed the arbor down, allowing the ejector collar to push
the coolant ring up and the retaining clip into its groove.
5. Adjust and tighten arbor support bracket before using
drill. (See arbor support bracket adjustment procedure)
5. Screw Impactor Point 1/4 - 1/3 turn further toward work
surface.
6. Tighten Nyloc Nut, while preventing the Impactor from
turning.
7. Check adjustment by placing a 1” x 3” piece of paper
under rear edge of magnet and turn magnet ON. Use
Slide Hammer (10961) once or twice to impact the
point. Paper should not slip out from under magnet
then pulled.
NOTE: Impactor adjustment should be checked
regularly following the procedure outlined in Step 7
above.
IMPACTOR ADJUSTMENT
1. Sharpen or replace impactor point if point is exces
sively worn or chipped.
2. Adjustment is made with MAGNET ON and impactor
over the work surface.
3. Loosen Nyloc Nut (10567) on bottom of Impactor.
4. Screw Impactor (10962) so that the point is flush with
work surface.
ADJUSTMENT OF GIBS
1. Loosen all Gib screws (40237)
2. Feed the drill up and down a few times and then, with
top of motor slide flush with top of housing, tighten the
Gib Screws until you feel them touch the Steel Gib.
(40225).
3. Feed the drill up and down again.
4. Adjust Gib screws so that their is uniform pressure
from top to bottom. (Top of motor slide flush with top of
housing.)
5. Turn each Gib Screw in about 1/8 - 1/4 turn, depending
upon your preference.
6. Gibs should be tight enough so that the slide moves up
and down smoothly with no wobble or shaking (Loose
ness will cause cutter breakage).
NOTE: GIBS SHOULD BE LUBRICATED REGULARLY
ARBOR SUPPORT BRACKET
ADJUSTMENT
Adjust gibs before adjusting arbor support bracket
1. Turn magnet ON.
2. Loosen Arbor Support Bracket Bolts (40451)
3. Be sure top of arbor is flush with the shoulder on motor
spindle and key is fully engaged. Also check arbor-to-
spindle screw to make sure it is tight.
4. Turn feed handle until motor and spindle are at the
bottom of their travel.
5. Tighten Arbor Support Bolts (400 inch lbs.)
6. Feed slide up and down a few times, checking for free
and even vertical movement.
NOTE: Check arbor support bolts regularly to make
sure they are tight, ot tighten as needed.
Summary of Contents for 10925
Page 10: ...10 POWER FEED GEAR MOTOR...
Page 14: ...14 10925 10926 Power Feed Assembly...
Page 15: ...10925 10926 Mechanical Breakdown 15...
Page 16: ...16 Electrical Panel Layout Diagram...