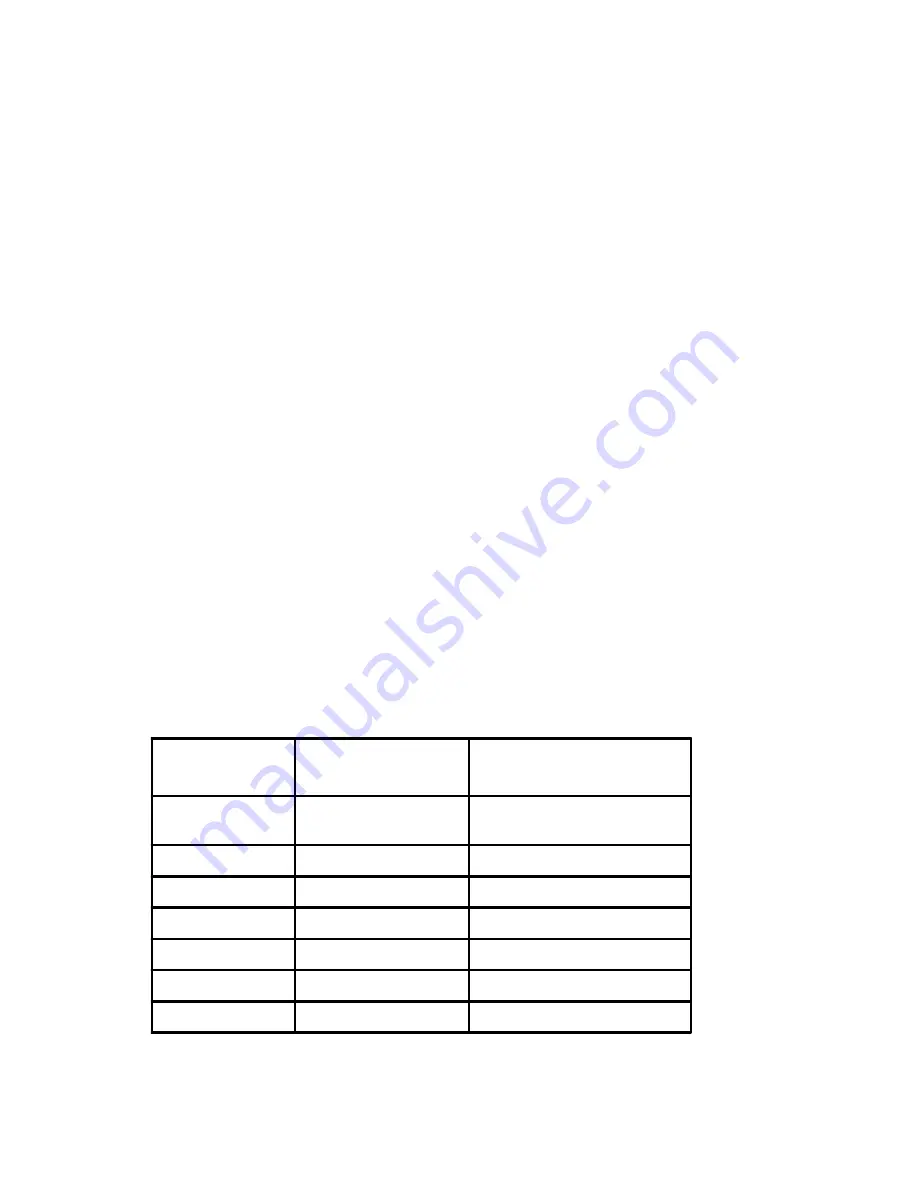
4
Table 1 Extension Cord Reference Chart
Unpacking Your New Portable Magnetic Drill
1. Open shipping carton and remove the literature and
hardare packages.
2. Read and follow all Instructions before attempting
to operate your new Magnetic Drill.
3. Complete and mail the Product Registration Card
NOW. It is important that Hougen Manufacturing, Inc.
have a record of product ownership.
4. Open hardware package and check contents.
10565 1/8” Allen Wrench for Gib Adjustment
10569 Feed handles (3)
10570 Feed handle knobs (3)
10727 3/16” Allen Wrench for reversing feed handle.
10730 Safety Chain
10779 7/32” Allen Wrench for cutter installation
13013 5/32” Allen Wrench for arbor installation and
microswitch adjustment
5. Using the handle of the Magnetic Drill, lift unit out of
the shipping case.
6. Remove all packing and securing material from the
drill unit.
7. Screw the three Knobs (10570) onto the three feed
handles (10569) and then screw the handles into the
hub .
8. Your Magnetic Drill was factory adjusted prior to shipping.
Check to make sure that all gib adjustment screws,
motor mount screws, front support bracket screws, and
magnet mounting screws are snug and have not vibrated
loose in transit.
9. Your New Magnetic Drill comes complete with arbor
mounted. The 3/4” diameter arbor bore fits all 3/4” -
shank “12000-Series” Rotabroach Cutters. A 1/2”
diameter boreArbor Adapter (10851), for mounting1/2”
shank “12,000-Series” Rotabroach Cutters, is optional.
Recommended cutting capacity when using “12,000-Series” Rotabroach Cutters-
Power Feed Mode
Manual Feed Mode
2” diameter maximum - 1” depth of cut
2-1/16” diameter maximum - 1” or 2” depth of cut
1-1/2” diameter maximum - 2” depth of cut
2” diameter maximum - 3” depth of cut
1-1/16” diameter maximum - 3” depth of cut
Actual cutting capacity may vary based on application. Feed setting chart on panel is recommended starting
point for diameter range. Adjustments may be needed for optimum cutting performance
Cutting Capacity
Length of Cord,
Feet
Recommended Wire
Gauge
Recommended Wire Gauge
115V Motor
10-12 Amps
230V Motor
5-6 Amps
Up to 25
16
18
26-50
14
18
51-100
10
16
101-200
8
14
201-300
6
12
301-500
4
10
Summary of Contents for 10925
Page 10: ...10 POWER FEED GEAR MOTOR...
Page 14: ...14 10925 10926 Power Feed Assembly...
Page 15: ...10925 10926 Mechanical Breakdown 15...
Page 16: ...16 Electrical Panel Layout Diagram...