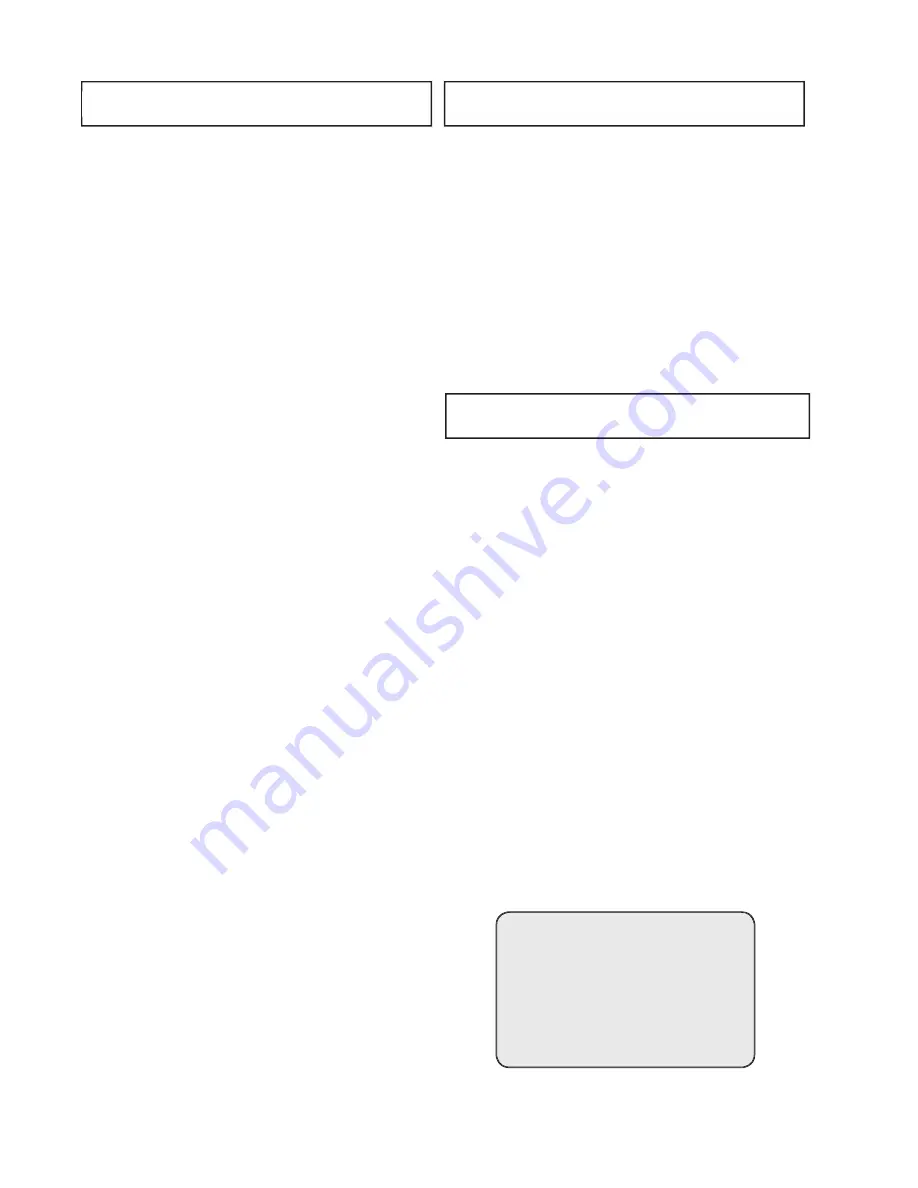
6
Operating Instructions
Always remember that the magnet’s holding power is
directly related to the workpiece thickness and surface
condition. Since magnetic attraction diminishes with thin-
ner material or rough surfaces, mechanical clamping of
drill unit to workpiece should be used when cutting thin
material (3/8” or less) or material with uneven surfaces.
Note: Always form a loose knot in the power cord
close to the molded plug. This prevents cutting fl uid
from running down the cord and into the power recep-
tacle. (Refer to the diagram within the Safety Instruc-
tions in this manual)
1. Make sure workpiece and bottom of magnet are free
of chips, oil, etc.
2. Secure unit to workpiece with safety chain.
3. Position drill by sliding it and gently feeding Arbor so
that pilot point is touching center of hole to be drilled.
4. Turn magnet ON by pressing the magnet ON button.
5. Move Impactor Slide Hammer up and down several
times, rapping base sharply to insure Impactor Point
is seated in workpiece and magnet is fl ush with
workpiece.
6. Turn Feed Handle, raising the cutter until the pilot is
above the work surface.
7. Open the cutting fl uid valve several full turns (Models
10914 only)
8. Make certain that cutter is clear of workpiece and turn
motor On by pressing the motor START button.
9. Feed the cutter slowly into workpiece. Only
after cutting path is established to a depth of about
1/16” can full force be applied to feed handles.
10. Ease up on feed pressure as cutter starts breaking
through.
11. At conclusion of cut, turn motor OFF by pressing
motor STOP button. Turn feed handles to raise Arbor
thereby ejecting the slug if it hasn’t already fallen free.
12. Turn magnet OFF by pressing the magnet OFF
button. As the magnet de-energizes, the rear of the
magnet should lift up off the work surface.
13.
Disconnect from power source.
14. If necessary, remove chips from cutter and magnet.,
preferably wearing leather work gloves and/or with
pliers.
15. Disconnect safety chain and you are ready to move
unit to new drilling position.
Special Instructions for horizontal or
Overhead Operation
1.
Always Use Safety Chain.
2. Use grease or animal-fat base solid lubricant applied
liberally to cutter.
3. For horizontal use, apply cutting fl uid to external parts
of cutter with plastic bottle or oiling can.
Adjustment of Gibs
1. Loosen all Gib Screws (40237)
2. Feed the drill in and out a few times and then, with top of
motor slide fl ush with top of housing, tighten the Gib
Screws until you feel them touch the Steel Gib (40225)
3. Feed the drill in and out again.
4. Adjust Gib screws so that there is uniform pressure from
top to bottom. (Top of motor slide fl ush with top of
housing)
5. Turn each Gib Screw in about 1/8 to 1/4 turn, depending
upon your preference.
6. Gibs should be tight enough so that slide moves in and
out smoothly with no wobble or shaking. (looseness will
cause cutter breakage)
Safety Switch Adjustment
1. Unplug unit from power source and place it on a fl at
sheet of steel that is at least 3/8” thick. Only magnet
portion should be on steel plate. Rear support block
(containing Glide Post and Impactor) should hang over
the edge of the steel plate.
2. Remove Access Hole Screw (10977) from back of
housing.
3. Insert 5/32” Allen Wrench into access hole and back off
(counterclockwise) Microswitch Adjusting Screw (10969)
about three full turns.
4. Plug unit into power source and turn magnet ON.
Depress and hold motor START switch ON while simulta-
neously turning Microswitch Adjusting Screw clockwise
until motor starts. Once the motor starts release the Motor
On Switch. Turn the adjusting screw 1-1/2 turns clock-
wise. This will set the Microswitch.
Testing of Microswitch
1. Plug unit into power source. Turn Magnet and motor
switches ON. Strike side of magnet at rear with a rubber
hammer. Motor should shut off before the magnet moves
1/2” in any direction. If the test was successful, replace
the Access Hole Screw (10969). If the unit failed the test,
recheck the Microswitch Adjustment.
NOTE: Safety switch adjustment should be checked
regularly following the procedures outlined above.
Operating Instructions
#1 cause of cutter
breakage and
prematurely dull
teeth is too little
feed pressure