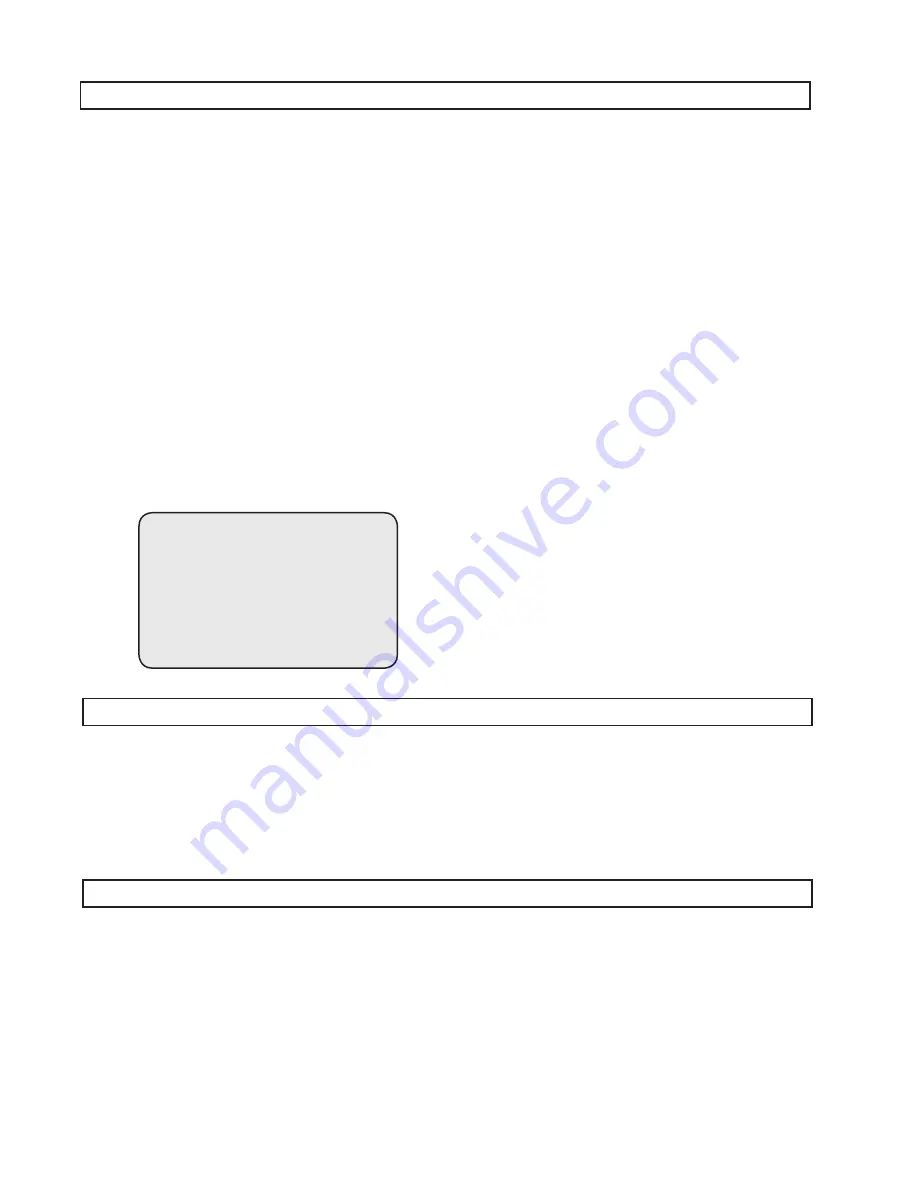
6
OPERATING INSTRUCTIONS
ARBOR ADJUSTMENT
DRILL MAINTENACE
Always remember that the magnet’s holding power is directly related to the workpiece thickness and surface condition. Since magnetic
attraction diminishes with thinner material or rough surfaces, mechanical clamping of drill unit to workpiece should be used when cutting
thin material (3/8" or less) or material with uneven surfaces.
Note: Always form a loose knot in the power cord close to the molded plug. This prevents cutting fluid from running down the
cord and into the power receptacle. (Refer to the diagram within the Safety Instructions in this manual)
1. Make sure workpiece and bottom of magnet are free of chips, oil, etc.
2. Secure unit to workpiece with safety chain.
3. Position drill by sliding it and gently feeding Arbor so that pilot point is touching center of hole to be drilled.
4. Turn magnet ON by pressing the magnet ON button.
5. Turn Feed Handle, raising the cutter until the pilot is above the work surface.
6. Open the cutting fluid valve.
7. Make certain that cutter is clear of workpiece and turn motor On by pressing the motor START button.
8. Feed the cutter slowly into workpiece. Only after cutting path is established to a depth of about
1/16" can full force be applied to feed handles.
9. Ease up on feed pressure as cutter starts breaking through.
10. At conclusion of cut, turn motor OFF by pressing motor STOP button. Turn feed handles to raise Arbor thereby
ejecting the slug if it hasn’t already fallen free.
11. Turn magnet OFF by pressing the magnet OFF button.
12.
Disconnect from power source.
13. If necessary, remove chips from cutter and magnet., preferably wearing leather work gloves and/or with pliers.
14. Disconnect safety chain and you are ready to move
unit to new drilling position.
Special Instructions for horizontal or Overhead Operation
1.
Always Use Safety Chain.
2. Use grease or animal-fat base solid lubricant applied liberally to cutter.
3. For horizontal use, apply cutting fluid to external parts of cutter with plastic bottle or oiling can.
1. Loosen all Gib Screws (40237)
2. Feed the drill up & down a few times and then, with top of motor slide flush with top of housing, tighten the Gib
Screws until you feel them touch the Steel Gib (See Parts Breakdown for location)
3. Feed the drill up and down again.
4. Adjust Gib screws so that there is uniform pressure from top to bottom. (Top of motor slide flush with top of housing)
5. Turn each Gib Screw in about 1/8 to 1/4 turn, depending upon your preference.
6. Gibs should be tight enough so that slide moves in and out smoothly with no wobble or shaking. (looseness will
cause cutter breakage)
#1 cause of cutter
breakage and
prematurely dull
teeth is too little
feed pressure
"Babying" the cutter through
the cut will only decrease
tool life
In order to minimize wear on moving parts and insure
smoother operation and longer life, the following
maintenance should be done periodically, based on use.
1. At intervals of 500 holes or 10 hours of actual running
time, check all fasteners for tightness and retighten if
necessary. This is especially important for fasteners
required for smooth, efficient cutting action. These
include: Gib screws and nuts, motor hold down
screws, skid plate screws, bracket mounting screws
and nuts, housing bolts, clamp screw and front
support bracket bolts.
2. Coolant bottle must be attached to inducer under
pressure with shut-off valve open to lubricate inducer
o-rings whenever motor, is running.
3. Apply grease to slide dovetails, brass gibs, and the
feed gear rack. (For best results, use Shell Cyprina-RA
or equivalent.)
4. Remove front support bracket from arbor and pack
bearing with grease. (Shell Cyprina-RA or equivalent)