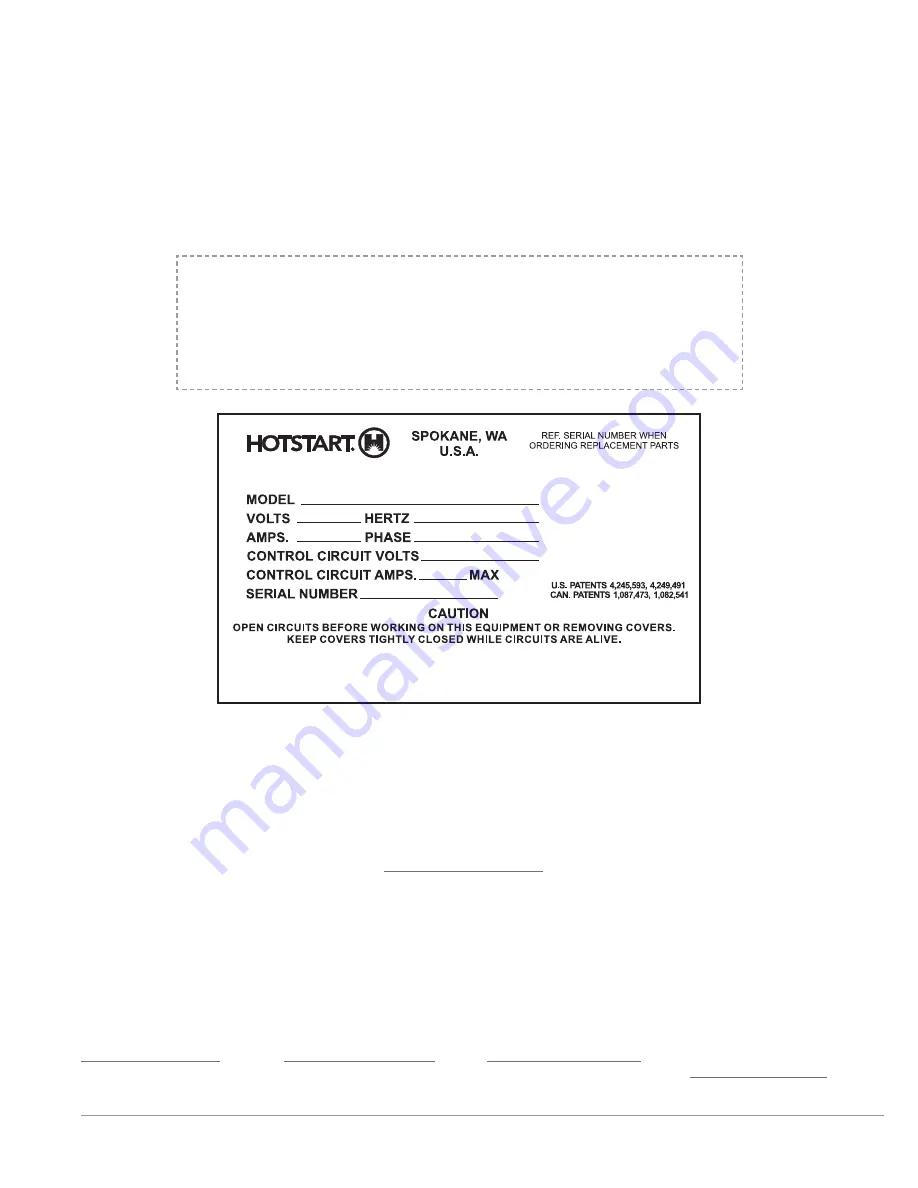
i
installation
&
operation
manual
|
dlv
heating
system
IOM216306-000
Corporate & Manufacturing
Headquarters
5723 E. Alki Ave.
Spokane, WA 99212 USA
509.536.8660
Oil & Gas Office
21732 Provincial Blvd.
Suite 170
Katy, TX 77450 USA
281.600.3700
Europe Office
HOTSTART GmbH
Am Turm 86
53721 Seigburg, Germany
+49.2241.12734.0
Asia Pacific Office
HOTSTART Asia Pacific Ltd.
2-27-15-4F Honkomagome
Bunkyo-ku, Tokyo
113-0021, Japan
+81.3.6902.0551
NOTE
Typical heating system identification plate. Your identification
plate may vary.
IDENTIFYING YOUR SYSTEM
The HOTSTART heating system is designed to heat fluids for use in marine propulsion, diesel-powered
generator sets, locomotives, gas compression or any large-engine applications. The system is pre-wired,
pre-plumbed and assembled on steel plate. Each heating system has an identification plate which includes
the part number and serial number.
When ordering replacement parts, be sure to reference your heating system’s
model
number
and
serial
number
found on the identification plate and following label:
WARRANTY INFORMATION
Warranty information can be found at
www.hotstart.com
or by contacting our customer service
department at
509.536.8660
. Have your
model
number
and
serial
number
ready when contacting
the warranty department.