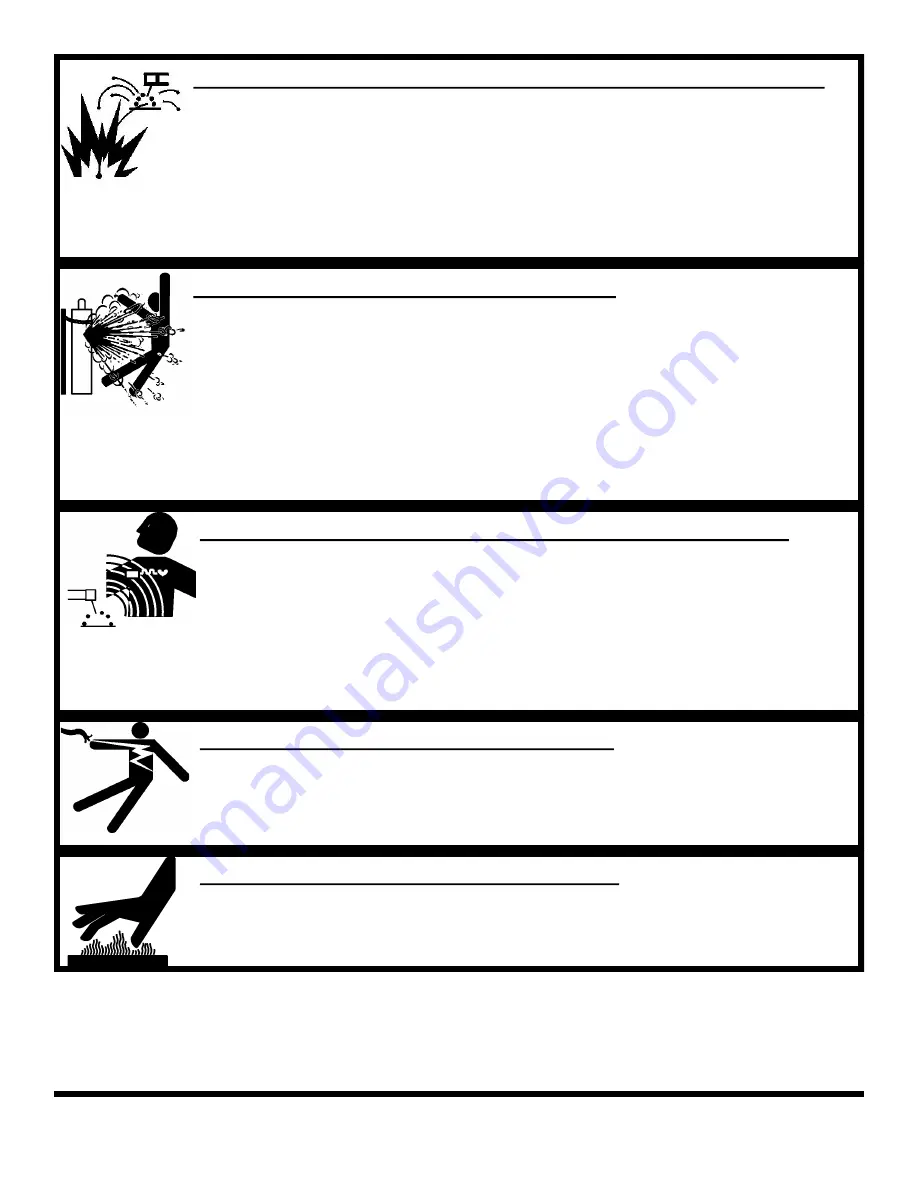
WELDING SPARKS CAN CAUSE INJURY, FIRE, OR EXPLOSION
Remove all flammable materials from the welding area
Always have a charged fire extinguisher available in the welding area
When not welding make sure the welding tip is not grounded, this causes a heat build up and
possible fire
Avoid welding near hydraulic lines, fuel lines, electrical cords, air hoses, or welding guns and
cables
Sparks and hot metal fly out from the work area when welding, wear approved safety glasses with
side shields under approved helmets, wear proper body and hand protection, and wear flame
resistant ear plugs to keep sparks from entering the ears
CYLINDERS CAN EXPLODE IF DAMAGED
Gas cylinders contain gas under very high pressure. If damaged they can result in that cylinder ex-
ploding. Gas cylinders are a major part of metalworking and must be treated with care.
Protect gas cylinders from excessive heat, mechanical shocks, slag, open flames, sparks, and arcs
Always keep cylinders in an upright position securely fastened to a fixed support
Valve protection caps should always be in place and hand tight except when the cylinder is in use
Keep all cylinders away from any welding or electrical circuits
Never allow the arc from a welder to contact a cylinder
Never cut any type of pressurized cylinder, an explosion could result
Always turn your face away from the valve when opening the cylinder
Read and follow all instructions on compressed gas cylinders, associated equipment, and CGA pub-
lication P-1 listed in the Safety Standards before using
ELECTRIC AND MAGNETIC FIELDS MAY BE DANGEROUS
Electric current used in arc welding can create Electro-Magnetic Fields (EMF)
Magnetic fields can affect pacemakers and wearers should avoid proximity to EMF. Wearers need
to contact their doctors before operating this type of equipment
Exposure to EMF during operation of this equipment may have other health effects which are not
yet known
Route the work and torch cables together and not around your body
Do not place your body between the torch cable and the ground cable. They both need to be on the
same side of your body when operating
Do not work next to the welding machine
ELECTRICALLY POWERED EQUIPMENT
Disconnect power source or turn off circuit breaker at the power panel before working on any
equipment
Only install equipment using the US National Electrical Code, all local codes, and the manufactur-
er’s recommendations
KDAR Company
2
HOT PARTS CAN CAUSE SERIOUS BURNS
Do not touch hot parts without wearing protection.
Allow the torch to cool sufficiently before working with parts that could potentially be hot.