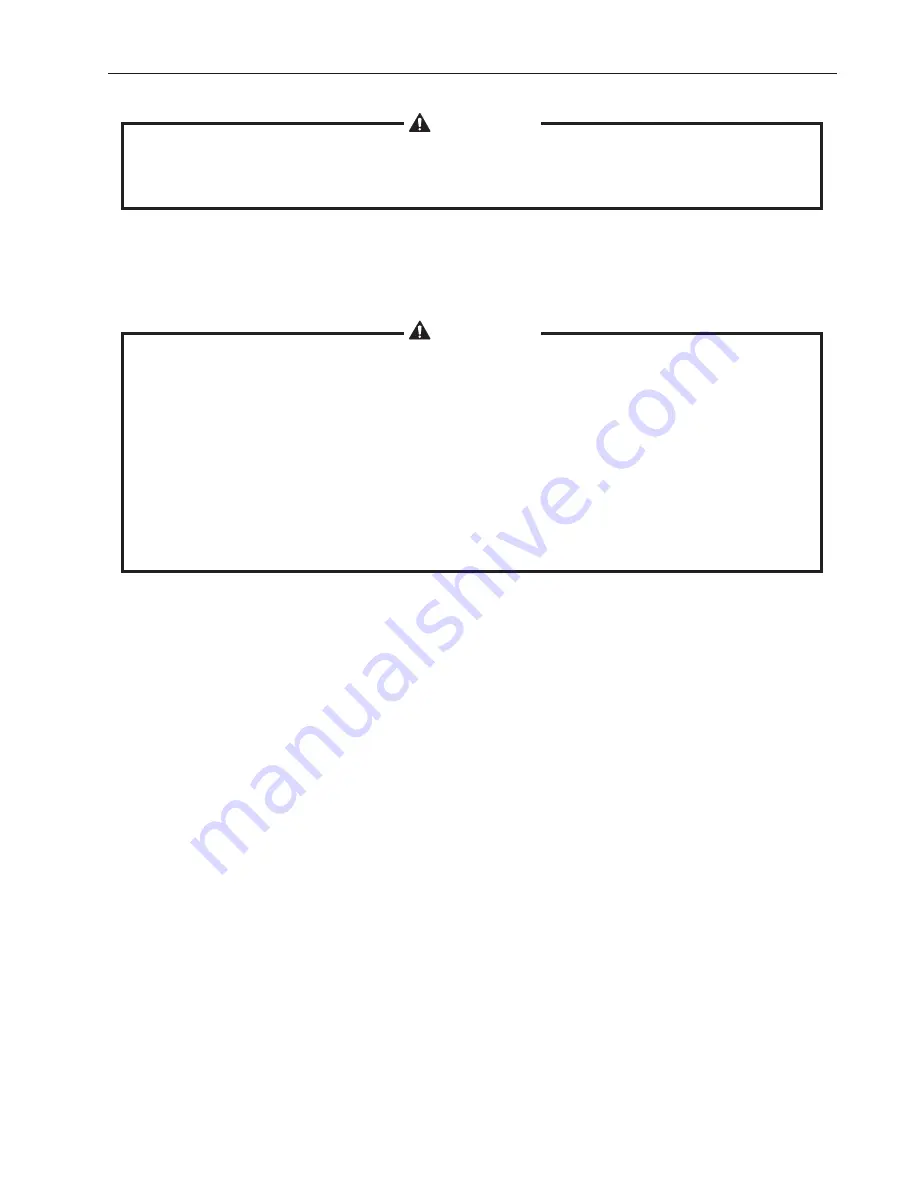
63
VI. Cleaning and Maintenance
WARNING
CHOKING HAZARD:
Ensure all components, fasteners, and thumbscrews are
securely in place after any cleaning or maintenance is done to the unit. Make
sure that none have fallen into the dispenser unit/storage bin.
A. Cleaning and Sanitizing Instructions
Hoshizaki recommends cleaning and sanitizing this unit at least once a year. More
frequent cleaning and sanitizing, however, may be required in some existing water
conditions.
WARNING
1. To prevent injury to individuals and damage to the icemaker, do not use
ammonia type cleaners.
2. Carefully follow any instructions provided with the bottles of cleaning and
sanitizing solution.
3. Always wear liquid-proof gloves and goggles to prevent the cleaning and
sanitizing solutions from coming into contact with skin or eyes.
4. To prevent damage to the water pump, do not leave the control switch in
the "SERVICE" position for extended periods of time when the water tank is
empty.
1. Cleaning Procedure
1) Dilute 9.5 fl. oz. (281 ml) of Hoshizaki "Scale Away" with 1.8 gal. (6.8 l) of warm water.
2) Remove all ice from the evaporator and the dispenser unit/storage bin.
Note: To remove cubes on the evaporator, turn off the power supply and turn it on
after 3 minutes. The harvest cycle starts and the cubes will be removed from the
evaporator.
3) Turn off the power supply.
4) Remove the front panel, then move the service switch to the "DRAIN" position. Move
the control switch to the "SERVICE" position.
5) Replace the front panel in its correct position, then turn on the power supply for
2 minutes.
6) Turn off the power supply.
7) Remove the front panel, then remove insulation panel (A) (the large insulation panel in
front of the evaporator) by lifting up the panel slightly and pulling it towards you.