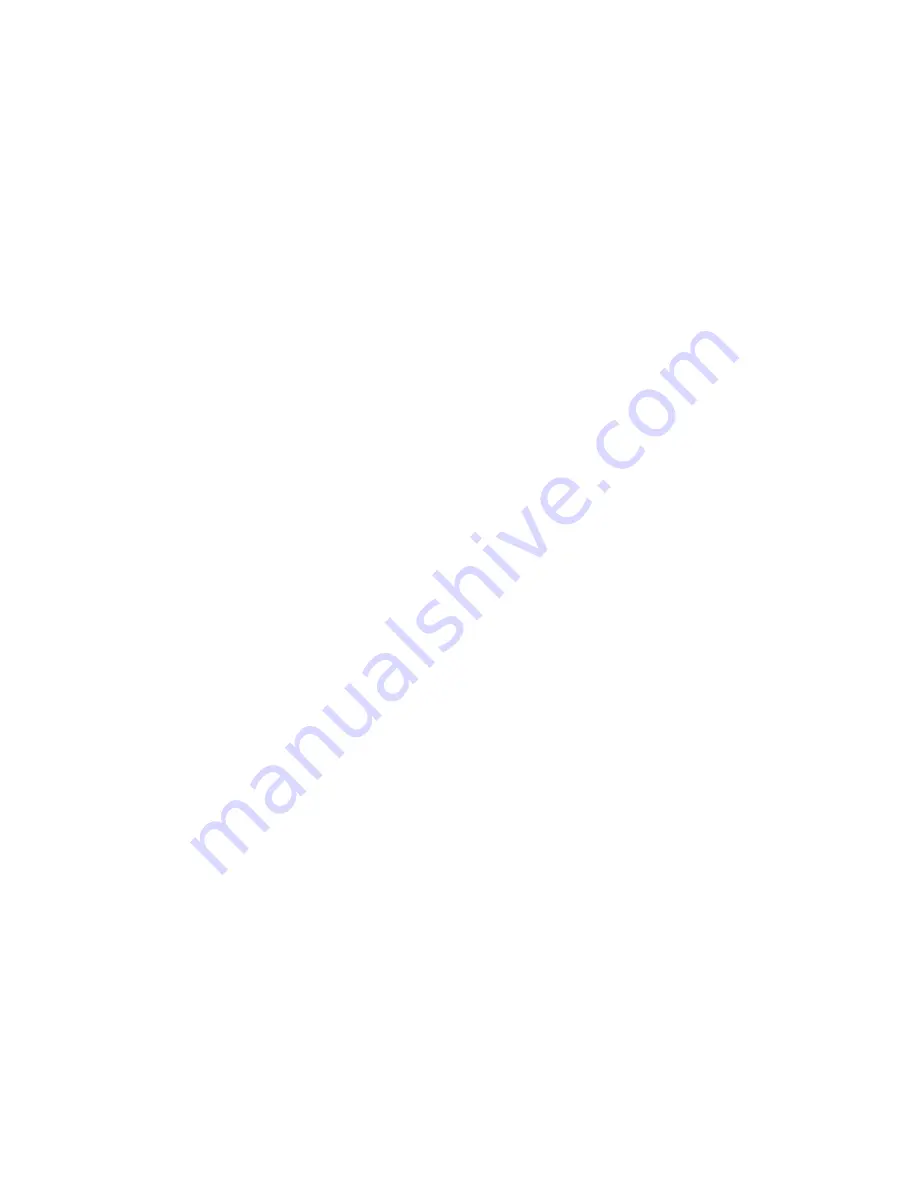
15
Pump-Out Diagnosis
: In the freeze cycle before pump-out (see table above), after
5 min. of freeze disconnect CB black K5 connector (FS connector). Check that PM
stops and re-starts. Next, check that PM rotation is correct (water flowing down the
drain through CV). If PM does not stop and re-start, check that CB LEDs 1, 3, and 2
are on. If not, replace CB. If LEDs 1, 3, and 2 are on and PM does not energize, check
for 115VAC at CB K1 #5 (DBU) to neutral (W). If 115VAC is not present, replace CB.
If 115VAC is present, check that X10 relay is de-energized. If not, check X11 relay
status. If X11 relay is energized, replace CB. If X11 relay is de-energized and X10
relay is energized, replace X11 relay (contacts sticking). If X10 relay is de-energized,
check for 115VAC at terminal #6 (DBU) to neutral (W) and terminal #2 (DBU) to neutral
(W). If 115VAC is present on terminal #6 (DBU) and not on terminal #2 (DBU), replace
X10 relay. If 115VAC is present on X10 terminal #2 (DBU) and PM is not energized
check for 115VAC at X12 terminal #6 (DBU) to neutral (W) and X12 terminal #4 (DBU)
to neutral (W). If 115VAC is present on X12 terminal #6 (DBU) and not on X12 terminal
#4 (DBU), check for 115VAC at X12 terminal #7 (P) to X12 terminal #8 (W).
If 115VAC is not present, check CB K1 pin #2 (P) wiring for loose connection. If 115VAC
is present and X12 is not energized, check coil continuity. Replace as needed. If X12
is energized and X12 terminal #4 (DBU) does not have 115VAC, replace X12 relay
(contacts sticking). If X12 terminal #4 (DBU) has 115VAC, PM should be energized and
rotating in pump-out rotation. If not, check PM motor windings and impeller for binding.
If energized and rotating correctly, make sure the drain line is not clogged and that CV
is clean and operating properly.
Confirm LLV de-energizes. If LLV is energized with LEDs 1, 3, and 2 on, replace CB.
8)
Normal Harvest Cycle
– Same as the initial harvest cycle. Return to step 5a) above.
Note: Appliance continues to cycle until BC is satisfied or power is switched off.
The appliance always restarts at the 1-min. fill cycle.
2. Shutdown
1) See "II.D.Bin Control Check."
Legend:
BC
–bin control;
CB
–control board;
Comp
–compressor;
CV
–check valve;
FM
–fan motor;
FS
–float switch;
HGV
–hot gas valve;
HPS
–high-pressure switch;
LLV
–liquid line valve;
PM
–pump motor;
TXV
–thermostatic expansion valve;
WV
–inlet water valve