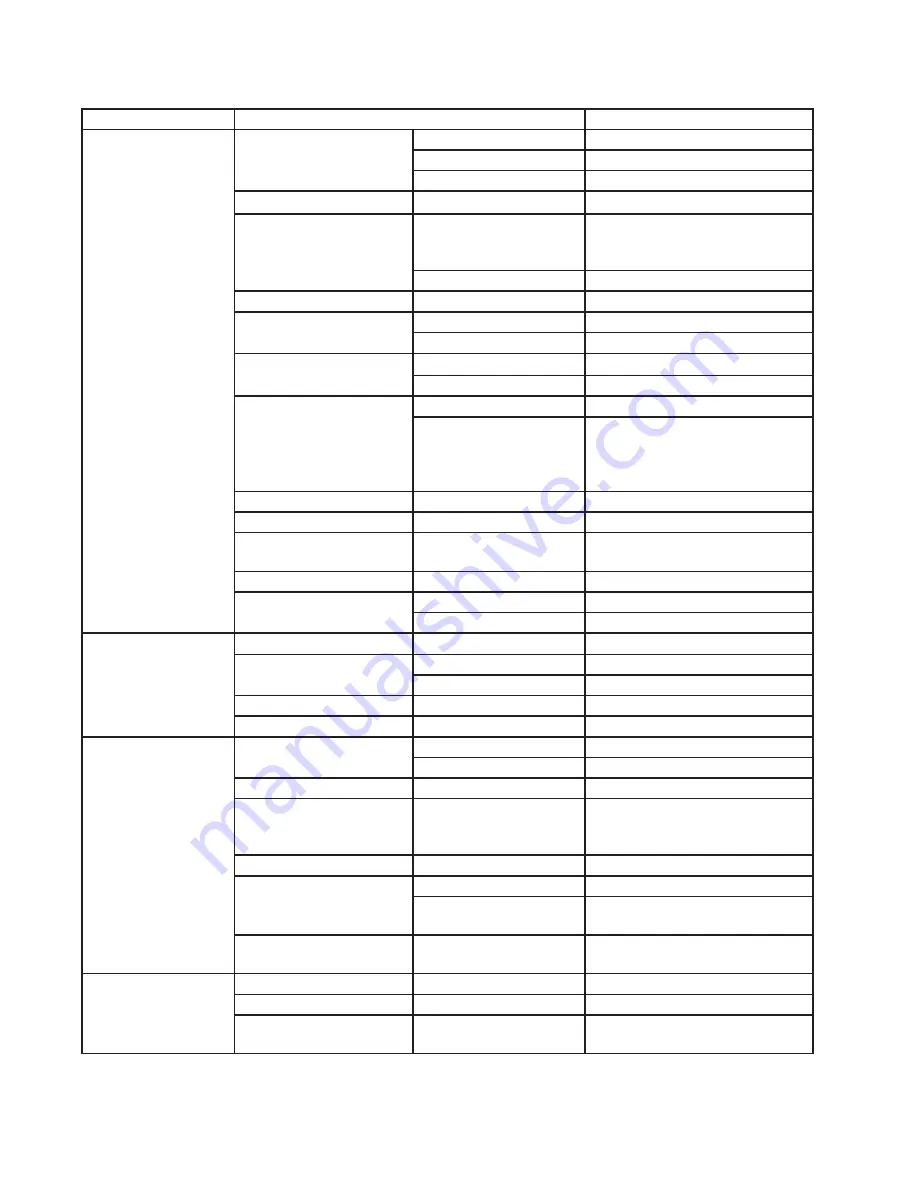
42
B. Diagnosis Chart
Problem
Possible Cause
Remedy
[1] Compressor will
not start—no
current draw.
a) Power Supply
1. "OFF" position.
1. Move to "ON" position.
2. Loose connection(s). 2. Tighten or reconnect.
3. Failure.
3. Call electrician.
b) Cord and Plug
1. Defective.
1. Replace.
c) Circuit Breaker
(kitchen)
1. Tripped.
1. Check and reset. Call
electrician if breaker trips
repeatedly.
2. Defective.
2. Call electrician.
d) Transformer
1. Open coil winding.
1. Check continuity and replace.
e) Wiring to Control Board 1. Loose connection(s). 1. Tighten.
2. Faulty.
2. Check continuity and replace.
f) Voltage
1. Too low.
1. Call electrician.
2. Too high.
2. Call electrician.
g) High Pressure Switch
1. Bad contacts.
1. Check continuity and replace.
2. Has operated 5 or
more times in one
hour. (E4 should be
displayed)
2. Determine why pressure
switch is activated.
h) Thermistor
1. Defective.
1. Check and replace.
i) Control Board
1. Defective.
1. Replace control board.
j) Compressor Overload 1. Defective. (Contacts
open)
1. Replace.
k) Compressor
1. Open windings.
1. Check continuity and replace.
l) Relay (Condensing
Unit)
1. Bad contacts.
1. Replace.
2. Open coil winding.
2. Check and replace.
[2] Compressor will
not run—draws
current and trips
on overload.
a) Voltage
1. Too low.
1. Call electrician.
b) Start Relay
1. Bad contacts.
1. Replace.
2. Open coil windings.
2. Replace.
c) Compressor
1. Locked rotor.
1. Replace.
d) Start Capacitor
1. Defective.
1. Check and replace.
[3] Compressor runs
intermittently and
trips on overload.
a) Voltage
1. Too low.
1. Call electrician.
2. Too high.
2. Call electrician.
b) Condenser Filter
1. Clogged.
1. Clean filter.
c) Refrigerant Line or
Component
1. Plugged or restricted. 1. Clean and replace drier. Clean
and replace capillary tube heat
exchanger assembly.
d) Condenser Fan Motor
1. Failed.
1. Replace.
e) Refrigerant
1. Overcharged.
1. Evacuate and recharge.
2. Non-condensibles in
system.
2. Evacuate and recharge.
f) Location of Unit
1. Restricted air flow to
condenser.
1. Move unit or increase
ventilation.
[4] Cabinet
temperature too
high; compressor
will not start.
a) Thermistor
1. Defective.
1. Check and replace.
b) Compressor Relay
1. Defective.
1. Check and replace.
c) Control Board
1. Defective.
1. Replace.
Summary of Contents for HUF40A
Page 6: ...6 Units mm in 1a HUR40A D HUF40A D 1 HUR40A HUF40A ...
Page 7: ...7 2 HWR40A HWF40A Units mm in 2a HWR40A D HWF40A D ...
Page 8: ...8 3 HUR68A HUF68A Units mm in 3a HUR68A D HUF68A D ...
Page 9: ...9 4 HWR68A HWF68A Units mm in 4a HWR68A D HWF68A D ...
Page 10: ...10 5 HUR96A 5a HUR96A D Units mm in ...