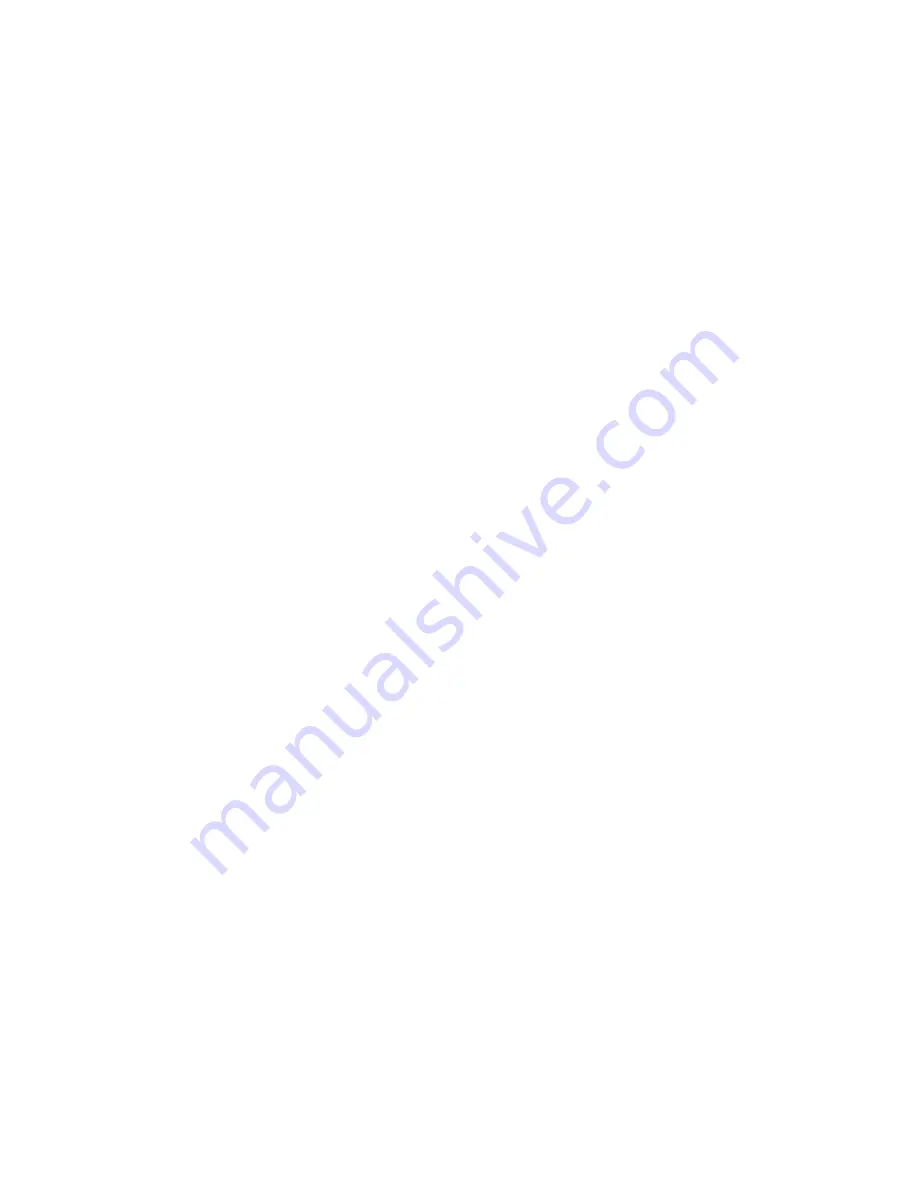
68
5) Make sure the "GM" LED is on. There is a delay of at least 30 seconds before the "GM"
LED turns on after power-up. After the "GM" LED turns on, press the "SERVICE" button
on the control board to bypass the 5-minute compressor delay.
WARNING! Risk of
electric shock. Care should be taken not to touch live terminals.
The "COMP" LED
turns on.
6) Press the actuator paddle located in the top of the chute.
S1 dip switch 7 in the "ON" position:
The compressor and gear motor should
de-energize within 10 seconds and the control board should sound a 9-beep alarm.
S1 dip switch 7 in the "OFF" position:
The compressor and gear motor should
de-energize within 10 seconds.
Diagnosis:
If the mechanical bin control fails to
open or the icemaker fails to shut down, check that the actuator paddle is moving
freely. Confirm that the actuator paddle is engaged. Check for continuity across
the mechanical bin control wires. If the mechanical bin control is found open and
the icemaker continues to run, the control board is bad and must be replaced. If
the mechanical bin control is found closed with the actuator paddle engaged, the
mechanical bin control proximity switch is bad and must be replaced.
7) Move the power switch to the "OFF" position and turn off the power supply.
8) Replace the chute assembly and strap in their correct positions.
9) Move the power switch to the "ON" position.
10) Replace the control box cover, top panel, and front panel in their correct positions.
11) Turn on the power supply to start the automatic icemaking process.