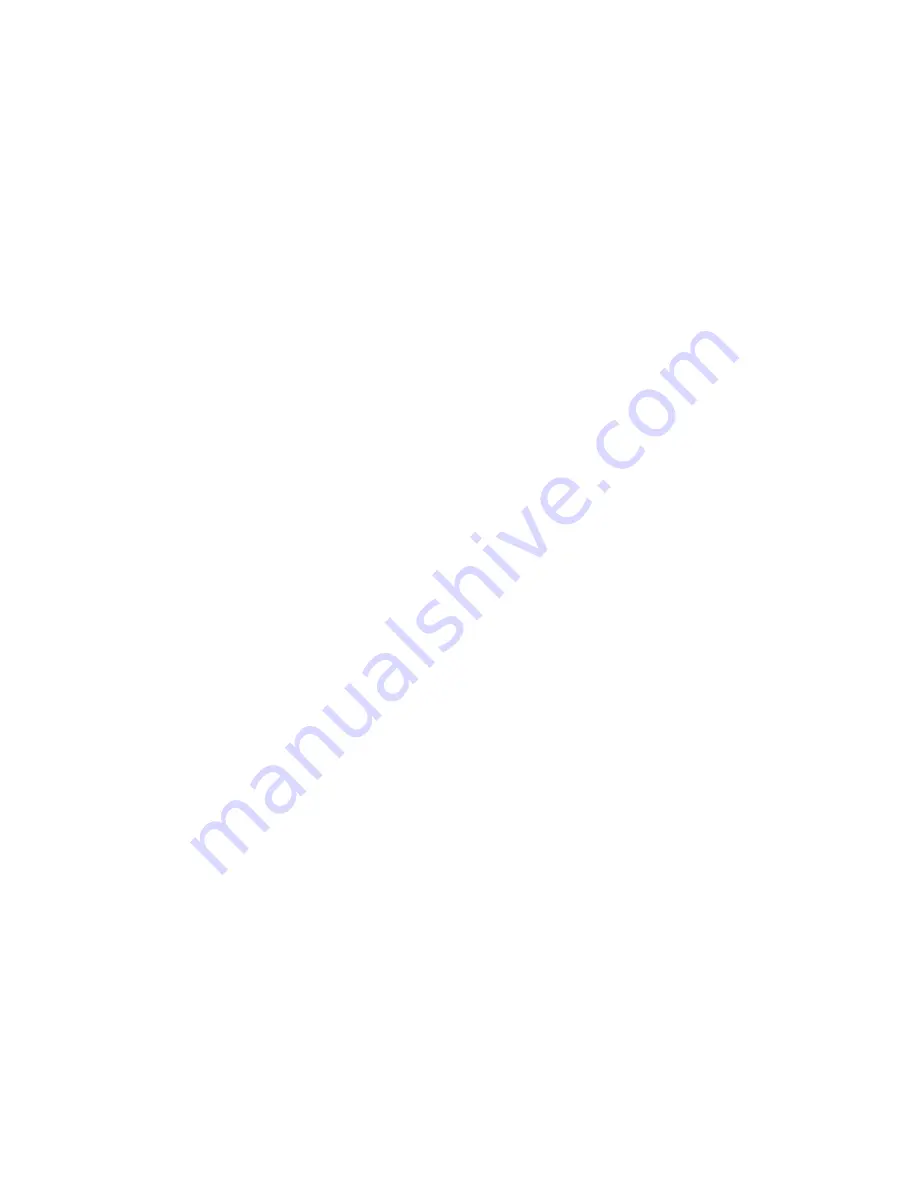
140
7. EVAPORATOR ASSEMBLY
See the exploded view under “III. 3. ICEMAKING MECHANISM”.
1) Push the stop button to drain the water in the evaporator.
2) Disconnect the power source.
3) Remove the panels.
4) Remove the three thumbscrews, and take off the spout from the evaporator.
5) Remove the bin control switch.
6) Remove the spout gasket at the top of the evaporator.
CUTTER
7) Remove the bolt and lift off the cutter.
BELT HEATER
8) Detach the spring, and remove the belt heater.
EXTRUDING HEAD
9) Remove the sealing bolts, and lift off the extruding head.
10) Check the bearing inside the extruding head. If it is worn out or scratched, replace the
bearing.
Note: Replacing the bearing needs a fitting tool. If it is not available, replace the whole
extruding head.
AUGER
11) Lift out the auger. Check the top and bottom areas in contact with the bearings. If the
surface is scratched or pitted, replace the auger. Check the blade edge of the auger. If it
is scratched or worn where it has contacted the evaporator, replace it.
EVAPORATOR
Note: Skip the following steps 12) through 18) when the evaporator does not need
replacement.
12) Recover the refrigerant and store it in a proper container, if required by an applicable law
(See "1. [b] REFRIGERANT RECOVERY").
Summary of Contents for 1800ALKE(-N)
Page 5: ...1 I SPECIFICATIONS 1 DIMENSIONS SPECIFICATIONS a FM 170AKE...
Page 6: ...2 b FM 170AKE N...
Page 7: ...3 c FM 300AKE Auxiliary code D 0 or earlier...
Page 8: ...4 Auxiliary code D 1 or later...
Page 9: ...5 d FM 300AKE N Auxiliary code D 0 or earlier...
Page 10: ...6 Auxiliary code D 1 or later...
Page 11: ...7 e FM 480AKE Auxiliary code D 0 or earlier...
Page 12: ...8 Auxiliary code D 1 or later...
Page 13: ...9 f FM 480AKE N Auxiliary code D 0 or earlier...
Page 14: ...10 Auxiliary code D 1 or later...
Page 15: ...11 g FM 480AWKE Auxiliary code D 0 or earlier...
Page 16: ...12 Auxiliary code D 1 or later...
Page 17: ...13 h FM 480AWKE N Auxiliary code D 0 or earlier...
Page 18: ...14 Auxiliary code D 1 or later...
Page 19: ...15 i FM 600AKE Auxiliary code D 0 or earlier...
Page 20: ...16 Auxiliary code D 1 or later...
Page 21: ...17 j FM 600AKE N Auxiliary code D 0 or earlier...
Page 22: ...18 Auxiliary code D 1 or later...
Page 23: ...19 k FM 600AWKE Auxiliary code D 0 or earlier...
Page 24: ...20 Auxiliary code D 1 or later...
Page 25: ...21 l FM 600AWKE N Auxiliary code D 0 or earlier...
Page 26: ...22 Auxiliary code D 1 or later...
Page 27: ...23 m FM 750AKE Auxiliary code D 0 or earlier...
Page 28: ...24 Auxiliary code D 1 or later...
Page 29: ...25 n FM 750AKE N Auxiliary code D 0 or earlier...
Page 30: ...26 Auxiliary code D 1 or later...
Page 31: ...27 o FM 1000AKE Auxiliary code D 0 or earlier...
Page 32: ...28 Auxiliary code D 1 or later...
Page 33: ...29 p FM 1000AKE N Auxiliary code D 0 or earlier...
Page 34: ...30 Auxiliary code D 1 or later...
Page 35: ...31 q FM 1200ALKE Auxiliary code D 0 or earlier...
Page 36: ...32 Auxiliary code D 1 or later...
Page 37: ...33 r FM 1200ALKE N Auxiliary code D 0 or earlier...
Page 38: ...34 Auxiliary code D 1 or later...
Page 39: ...35 s FM 1800ALKE Auxiliary code D 0 or earlier...
Page 40: ...36 Auxiliary code D 1 or later...
Page 41: ...37 t FM 1800ALKE N Auxiliary code D 0 or earlier...
Page 42: ...38 Auxiliary code D 1 or later...
Page 57: ...53 c FM 1200ALKE N...
Page 58: ...54 d FM 1800ALKE N...
Page 60: ...56 2 WIRING DIAGRAM a WIRING DIAGRAM FM 170AKE N Auxiliary code D 0 or earlier...
Page 61: ...57 FM 170AKE N Auxiliary code D 1 or later...
Page 62: ...58 FM 300AKE N Auxiliary code D 0 or earlier...
Page 63: ...59 FM 300AKE N Auxiliary code D 1 or later...
Page 64: ...60 FM 480AKE N Auxiliary code D 0 or earlier...
Page 65: ...61 FM 480AKE N Auxiliary code D 1 or later...
Page 66: ...62 FM 480AWKE N Auxiliary code D 0 or earlier...
Page 67: ...63 FM 480AWKE N Auxiliary code D 1 or later...
Page 68: ...64 FM 600AKE N Auxiliary code D 0 or earlier...
Page 69: ...65 FM 600AKE N Auxiliary code D 1 or later...
Page 70: ...66 FM 600AWKE N Auxiliary code D 0 or earlier...
Page 71: ...67 FM 600AWKE N Auxiliary code D 1 or later...
Page 72: ...68 FM 750AKE N Auxiliary code A 2 or earlier...
Page 73: ...69 FM 750AKE N Auxiliary code A 3 and B 0...
Page 74: ...70 FM 750AKE N Auxiliary code B 1 to D 0...
Page 75: ...71 FM 750AKE N Auxiliary code D 1 or later...
Page 76: ...72 FM 1000AKE N Auxiliary code A 2 or earlier...
Page 77: ...73 FM 1000AKE N Auxiliary code A 3 and B 0...
Page 78: ...74 FM 1000AKE N Auxiliary code B 1 to D 0...
Page 79: ...75 FM 1000AKE N Auxiliary code D 1 or later...
Page 80: ...76 FM 1200ALKE N Auxiliary code A 3 or earlier...
Page 81: ...77 FM 1200ALKE N Auxiliary code A 4 and B 0...
Page 82: ...78 FM 1200ALKE N Auxiliary code B 1 to D 0...
Page 83: ...79 FM 1200ALKE N Auxiliary code D 1 or later...
Page 84: ...80 FM 1800ALKE N Auxiliary code A 3 or earlier...
Page 85: ...81 FM 1800ALKE N Auxiliary code A 4 and B 0...
Page 86: ...82 FM 1800ALKE N Auxiliary code B 1 and D 0...
Page 87: ...83 FM 1800ALKE N Auxiliary code D 1 or later...
Page 92: ...88 FM 750AKE N FM 1000AKE N Auxiliary code B0 or earlier...
Page 93: ...89 FM 1200ALKE N Auxiliary code B0 or earlier...
Page 94: ...90 FM 1800ALKE N Auxiliary code B0 or earlier...
Page 106: ...102 b TIMING CHART...
Page 127: ...123 m FM 750AKE...
Page 128: ...124 n FM 750AKE N...
Page 129: ...125 o FM 1000AKE...
Page 130: ...126 p FM 1000AKE N...