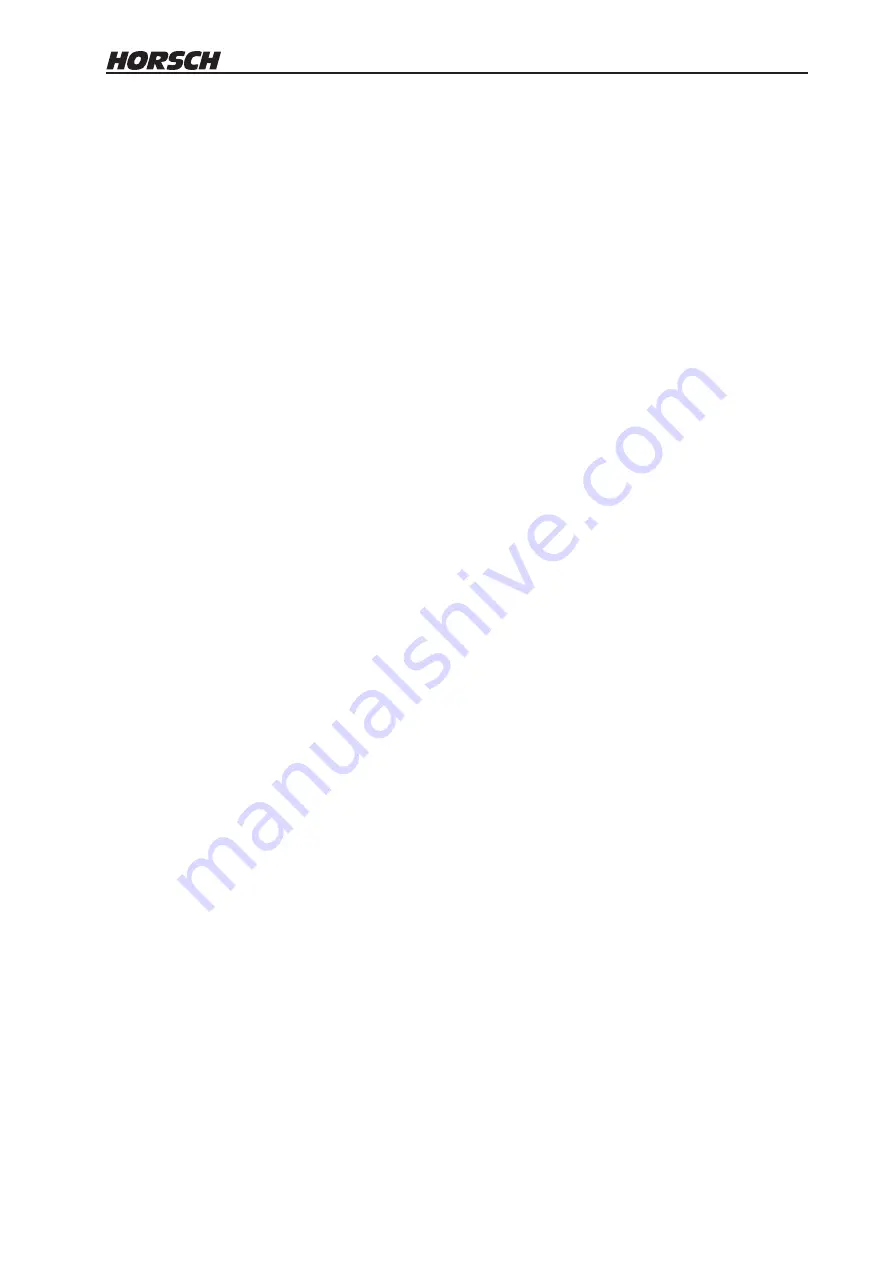
Intended use
The drill is state-of-the-art and designed in ac-
cordance with relevant, recognised safety regu-
lations. However, risks of injury to the operator
or third parties and impairment of the machine
or other tangible assets can occur during use.
The machine must only be operated for its in-
tended use if in a technically perfect condition,
whilst being aware of safety and risks and in
strict compliance with the operating instructions!
Faults, particularly those which impair safety,
must be remedied immediately.
The machine must only be operated, serviced
and repaired by persons who are familiar with
it and have been made aware of the dangers
involved.
Genuine spare parts and accessories from
HORSCH have been specially designed for this
machine.
Spare parts and accessories which are not de-
livered by us, have not been tested or approved
by us.
Installation or use of non-original HORSCH
products may have a detrimental effect on
specific design features of the machine and
impair the safety of machine operators and the
machine itself.
HORSCH will not assume liability whatsoever for
damage resulting from the use of non-original
parts and accessories.
The drill is designed for the placement of seeds
and fertilisers. Any other use beyond these
limits, e.g. as a means of transport, is deemed
improper.
HORSCH will not assume liability whatsoever
for damage resulting from unintended use. The
risk will be borne solely by the user.
The respective accident prevention regulations
and other generally recognised safety-related,
occupational medical and road traffic regulations
are to be adhered to.
Observance of the Operation Manual and com-
pliance with the operating, maintenance and
repair regulations specified by the manufacturer
belong to intended usage.
Consequential damage
The machine has been manufactured by
HORSCH with great care. Nevertheless, even
when used properly, deviations or complete
failure in the application rate may be caused,
e.g. by:
¾
differences in the composition of seed or
Fertilizer
(i.e. grain size distribution, density,
geometrical shape, dressing, sealing).
¾
Blockages or seed bridging (i.e. caused by
foreign bodies, non-smooth seeds, sticky
dressing, moist
Fertilizer
).
¾
Worn wearing parts (e.g. metering unit).
¾
Damage caused by external influences.
¾
incorrect drive motor speeds and driving
speeds.
¾
incorrect setting of the unit (incorrect connec-
tion, non-observance of setting tables).
Therefore, it is crucial to always check your
machine before and during operation for correct
operation and adequate application accuracy.
Compensation claims for damages which have
not been caused by the machine, are excluded.
This also includes that any liability for conse-
quential damages caused by drill and control
commands, is excluded.
5