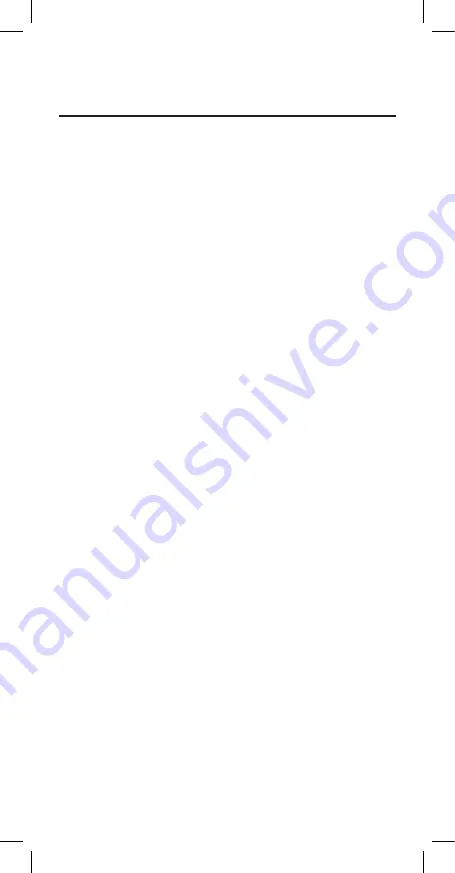
USER MANUAL
HIGH-FLOW 150 PSI A
IR SOURCE KIT
MOUNTING AND WIRING:
1.
Disconnect ground cable from vehicle’s battery.
2.
Temporarily position the air source kit in the location
where it will be mounted.
3.
Mount air source kit at tank leg mounts with the four
grommets, and four sets of bolts, nuts, washers,
and locking washers provided. Use of thread
locker
is recommended.
4.
Route
1
/
2
-inch
O
.D. air line
to
the 1/2-inch compression
fitting and make your air line
connection. Tighten
compression fitting nut securely
using a wrench.
5.
Connect ground (Black) wire to a clean ground,
(preferably a negative post of battery) and secure with
proper hardware
.
6.
Connect positive (Red) lead wire from pre-installed
pressure switch to a fuse holder (25-amp minimum).
7.
Once the kit is properly fused as close as possible to
the
power source, connect and test compressor system
by
running the compressor for a short time to build up
pressure in your air tank.
8.
Once air pressure reaches preset cut out pressure of
your pressure switch (1
1
0 PSI cut-on, 145 PSI cut-off),
the compressor will shut off automatically. Inspect all air
line connections for leaks with soap and water solution.
If
a leak is detected, the air line may not be cut squarely
or
pushed all the way in. Tighten connections if needed.