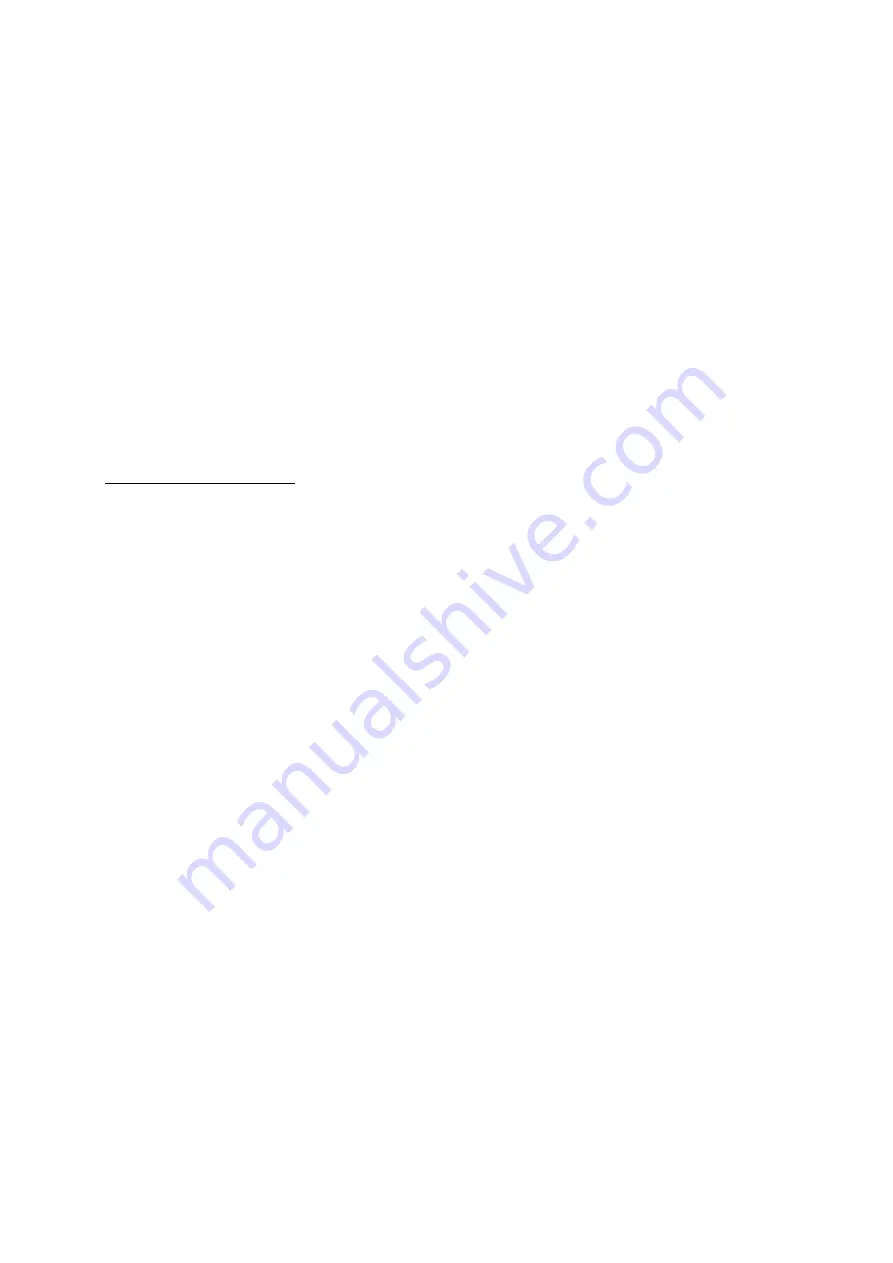
2
Make the slot in the fin 28 mm deep, ca. 8 mm wide – check the width, so that it fits onto the boom end.
Take the rudder and elevator servos. Make up the opening for the servos in the balsa servo floor. Assemble the
floor with the ply cross pieces, drill holes for the servo fastening screws and install the complete tray in place.
For
the pod-side walls strength it is important to mount the servos on the servo tray provided.
DO NOT omit
the servo tray as it plays important structural role in fuselage resistance against the centrifugal forces
during the launch
(the tray serves as the shear web, the fuselage sides are the “spar strips”).
Make the canopy lock of double piano wire 0,8 mm. Bend to shape, the ends meet in the middle of the length of
the lock. CA dip glue the lock wire to the hatch in the middle, spray CA activator. Do not use much CA, as it can
get hot and warm the canopy during the hardening.
Secure with epoxy soaked rectangle of carbon cloth (see the procedure for the wing joiners).
Using a fine file, make small notches in the pod, so that the lock wire can not shift sidewise.
Wing
The foam color can vary according to the producer. Anyway, the material is same.
VERY IMPORTANT WARNING: NEVER touch the wing / stab surface with nitrate base solvent. The skin is
slightly porous and the solvent would definitely damage the foam core!!!
For the same reason do not use common CA glue for the wing / stab assembly.
The wing is supplied in two parts. Mark position of the two mounting screws on the root ribs and make up small
half-round notches with rat-tail file (2 in each panel). Use good 5 minutes Epoxy to glue the wing parts together.
The dihedral of each panel is 6 deg. With one wing panel laying flat on the building board, the second panel is
supported 155 mm at the tip (2x6 deg = 12 deg).
Carefully open the holes to 5 mm dia. The axis of the holes MUST be perpendicular to the horizontal plane of the
model. Install two aluminum tubes, trim to length and epoxy in place. Use drill press and support both part of the
wing equally. Check for correct fit, file out the holes if necessary. Install two aluminum tubes, trim to length and
epoxy in place.
Locate the position of the launching peg: in the left wing tip for right hander and vice versa. Make the hole for the
launch peg.
Make patches from the carbon cloth/adhesive tape according to the pattern (four patches for the wing centre
connection, two round patches for the peg reinforcement.
Do NOT
try to separate the cloth from the tape in this
stage!!! Soak the carbon with thin slow curing epoxy and lay down over the center/tip connection seam and over
the peg hole, top and bottom. Press with fingers and attach in place with wide adhesive tape all over the patches.
After the epoxy sets, remove all of the adhesive tapes. The surface of the patches is nice and shiny.
Open carefully the 4 mm holes for the mounting screws and the opening for launching carbon peg. Epoxy the peg
well in place.
Note: It is possible that the peg/epoxy joint will loose as it is loaded. When it happens, apply drop of thin CA into
the seam for the good and permanent joint.
Attach the wing on the fuselage with the front screw. Locate and drill hole 3,2 mm dia. for the rear plastic screw in
the pod and run M4 tap. Be sure the wing is square with the fuselage.
Note: Over the years, the 4 carbon wing connection patches proved to give enough strength, provided the model
is flown in F3K style, on a flat field. If you crash, the wing halves usually separate in the middle and the repair is
possible.
If you want to do some slope flying, do not try the hard discuss type launch. The large angle of attack can cause
the wing break. We recommend to reinforce the two carbon patches around the front bolt with doublers of glass
cloth ca. 0,2 mm thick. Any case, be very careful when doing DLG on a slope as it is easy to slip and to suffer
serious body injury.