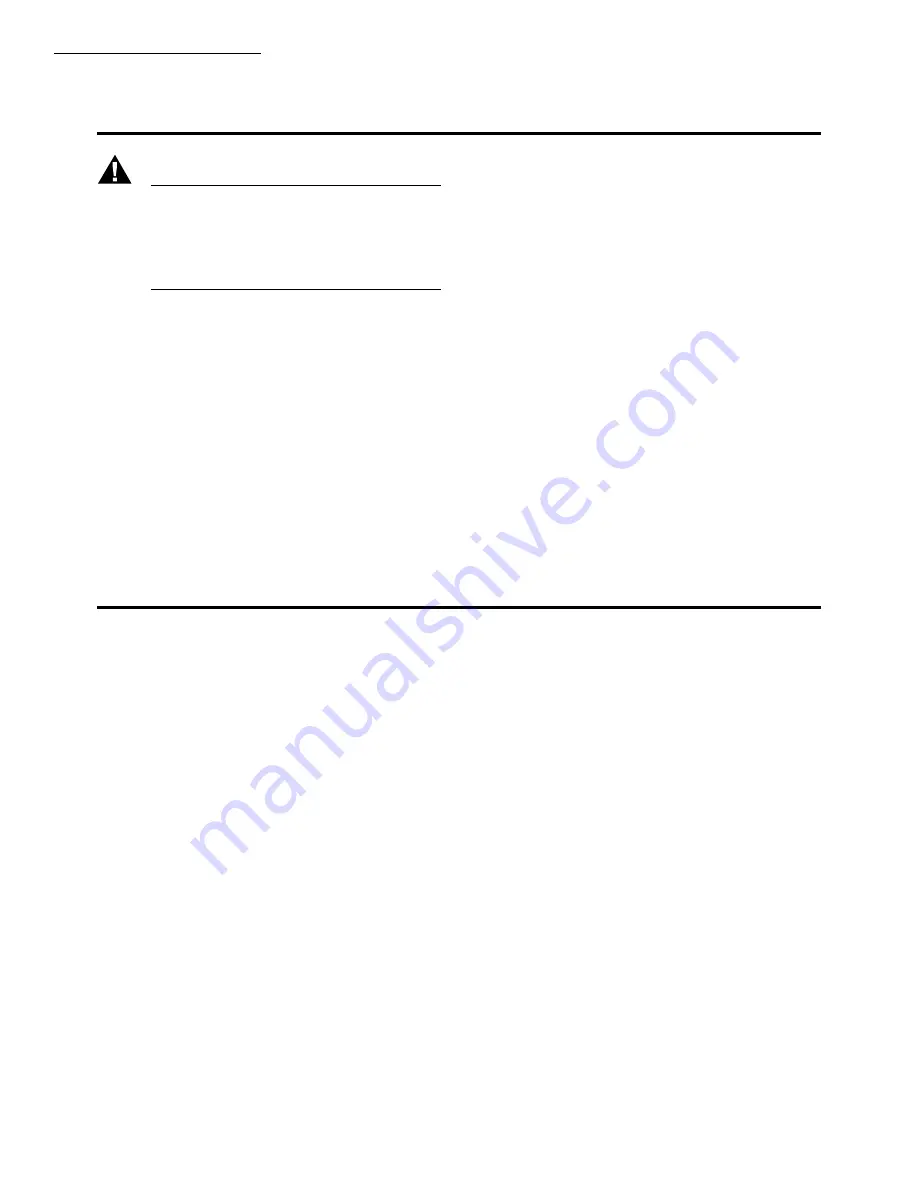
Maintenance
WARNING
FIRE OR EXPLOSION HAZARD
CAN CAUSE PROPERTY DAMAGE,
SEVERE INJURY, OR DEATH
Improper cleaning or reassembly could cause gas
leakage. When cleaning, ensure that control is reas-
sembled properly and perform gas leak test.
Regular preventive maintenance is important in applica-
tions such as in the commercial cooking and agricultural and
industrial industries that place a heavy load on system con-
trols because:
• The equipment operates 100,000-200,000 cycles per
year in many such applications, particularly commer-
cial cooking. Such heavy cycling can wear out the gas
control in one to two years.
• Exposure to water, dirt, chemicals and heat can damage
the gas control and shut down the control system.
The maintenance program should include regular check-
out of the gas control, see Start-Up and Checkout, page 8, and
the control system as described in the appliance manufacturer’s
literature.
Maintenance frequency must be determined individually
for each application. Some considerations are:
• Cycling frequency. Appliances that may cycle 100,000
times annually should be checked monthly.
• Intermittent use. Appliances that are used seasonally
should be checked before shutdown and again before
the next use.
• Consequence of unexpected shutdown. Where the cost
of an unexpected shutdown would be high, the system
should be checked more often.
• Dusty, wet, or corrosive environment. Since these
environments can cause the gas control to deteriorate
more rapidly, the system should be checked more
often.
The gas control should be replaced if:
• It does not perform properly on checkout or trouble-
shooting.
• The gas control knob is hard to turn or push down, or
it fails to pop back up when released.
• The gas control is likely to have operated for more than
200,000 cycles.
Operation
The VR8305 Gas Controls provide ON-OFF manual
control of gas flow. In the OFF position, main burner gas flow
is prevented. In the ON position, main burner gas flow is
under control of the thermostat, the direct ignition (DI)
module, and the two automatic main valves.
SYSTEM OPERATION WITH MODULE
When the thermostat calls for heat, the DI module is
energized. The module activates the first and second auto-
matic valves of the gas control, which allows main burner gas
flow. At the same time, the DI module generates a spark at the
igniter-sensor to light the main burner.
The second automatic valve diaphragm, controlled by the
servo pressure regulator, opens and adjusts gas flow as long
as the system is powered. The servo pressure regulator
monitors outlet pressure to provide an even main burner gas
flow. Loss of power (thermostat satisfied) de-energizes the
DI module and closes the automatic valves. The system is
ready to return to normal service when power is restored
through the thermostat.
If the igniter-sensor stops detecting a flame at the main
burner, the trial for ignition is restarted. On DI modules with
lockout timers, the automatic valves are de-energized and
ignition stops after the lockout period. On modules without
lockout timers, the trial for ignition continues indefinitely.
If main burner flame is restarted successfully, operation
continues as described above. Gas control operation is de-
scribed in more detail below.
VALVE POSITION DURING THERMOSTAT OFF
CYCLE
The valve is positioned as shown in Fig. 10 when the:
• gas control knob is in the ON position.
• thermostat is not calling for heat.
The first automatic valve is closed. The second automatic
valve operator is de-energized, closing the channel to the
pressure regulator, and opening a channel to the underside of
the second automatic valve operator valve diaphragm. The
combination of spring pressure under the second automatic
valve diaphragm and lack of outlet pressure hold the dia-
phragm firmly closed. Main burner gas flow is blocked by
both valves.
WHEN THERMOSTAT CALLS FOR HEAT
When the thermostat calls for heat, the DI module gener-
ates a spark at the main burner and the first automatic valve
and second automatic valve operators are energized, Fig. 11.
The first automatic valve opens, and the second automatic
valve operator valve disc is lifted off its seat. This diverts gas
flow from the second automatic valve diaphragm, and causes
a reduction of pressure on the underside of this diaphragm.
The reduced pressure on the bottom of the automatic valve
diaphragm repositions the diaphragm downward, away from
the valve seat, allowing main burner gas flow.
Standard-Opening Pressure Regulation (VR8305M)
During the On cycle, the servo pressure regulator provides
VR8305
MAINTENANCE • OPERATION
10
Summary of Contents for VR8305
Page 15: ...15 68 0109 3 ...