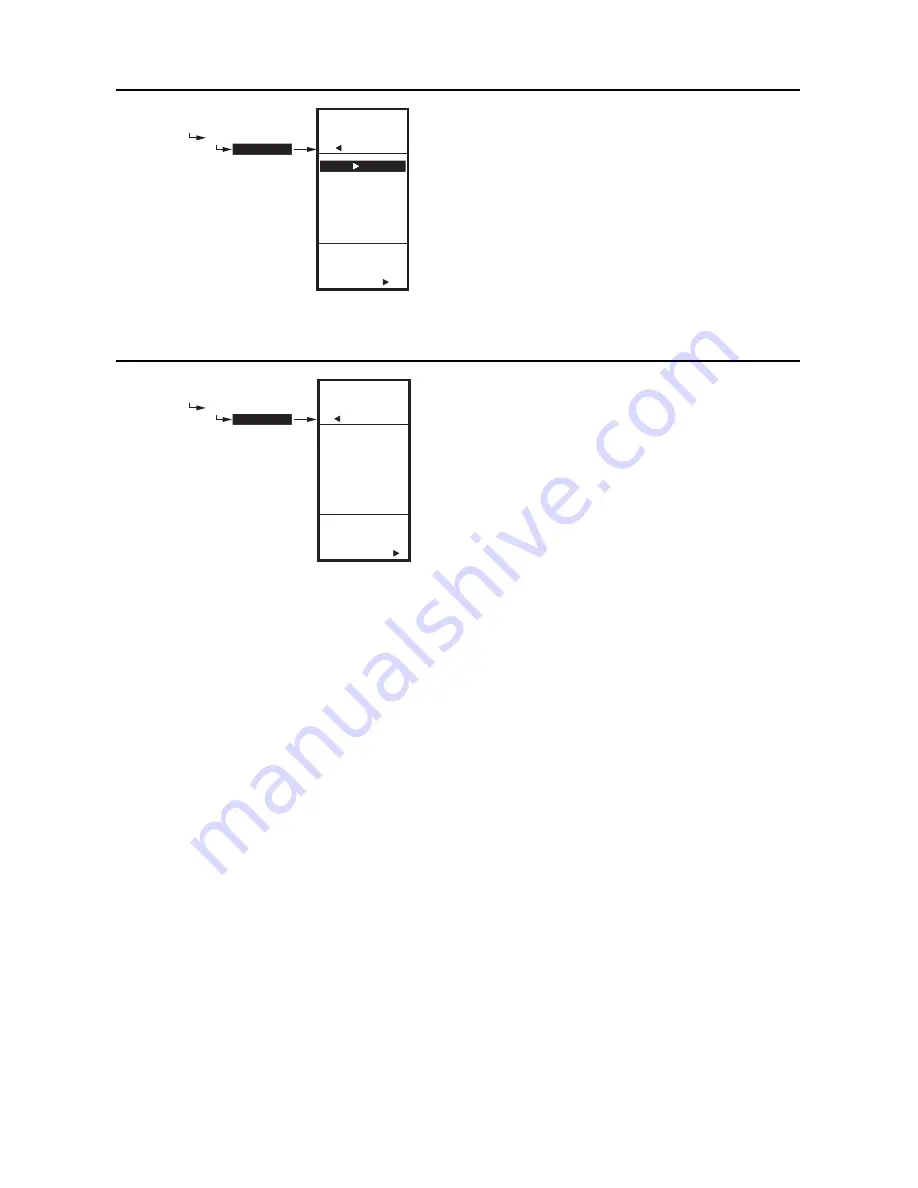
3. PROGRAMMING OUTPUTS (MOD AND RELAY) WITH RESET
T775U SERIES 2000 CONTROLLER
31
62-0255–05
Fig. 72. Program - Action Selection.
3.2.6. ACTION
For the MOD 1 output (and for outputs with RESET=NO),
the ACTION selection displays.
For all other outputs with RESET=YES, the ACTION
selection does
not
display; continue with “3.2.7.
SETBACK OFFSET (if configured)” on page 31.
1.
From the menu, use the
S
and
T
buttons to high-
light ACTION.
Default: HEAT
2.
Press the
X
button to display the action selections.
3.
Use the
S
and
T
buttons to select the desired
value.
4.
Press the
X
button to accept the highlighted selec-
tion and display the next option.
Fig. 73. Program - Setback (Offset).
3.2.7. SETBACK OFFSET
(if configured)
The Setback temperature option displays only if
scheduling is enabled (see Fig. 47 on page 21) or the DI
Option is set to Setback. (see Fig. 49 on page 22).
This value is the number of degrees plus (+) or minus (-)
that you want the temperature to be offset from the
setpoint.
For example, If you want the temperature to be 10°F less
than the setpoint during setback mode, enter -10°F. In
normal operations for heating, the offset will be negative.
For cooling, the offset will be a positive value.
1.
From the menu, use the
S
and
T
buttons to high-
light SETBACK.
2.
Use the
S
and
T
buttons to increase/decrease the
desired setpoint temperature.
Default: 0°F
Range: -150°F to 150°F (-101°C to 66°C)
3.
Press the
X
button to accept the value and display
the menu.
This completes the programming of the MOD 1 output.
To program the second Modulating output and the two
relays, continue with “3.3. Second Modulating Output and
Relays”.
PROGRAM
RELAY
1
ACTION
MENU
PROGRAM
RELAY 1
ACTION
SELECT
ACTION
FOR
RELAY 1
HEAT
COOL
REV ACT
DIR ACT
HUMID
DEHUMID
M24578
PROGRAM
RELAY
1
SETBACK
MENU
PROGRAM
RELAY 1
SETBACK
-10
F
o
ENTER
SETBACK
SETPOINT
FOR RELAY 1
M24579