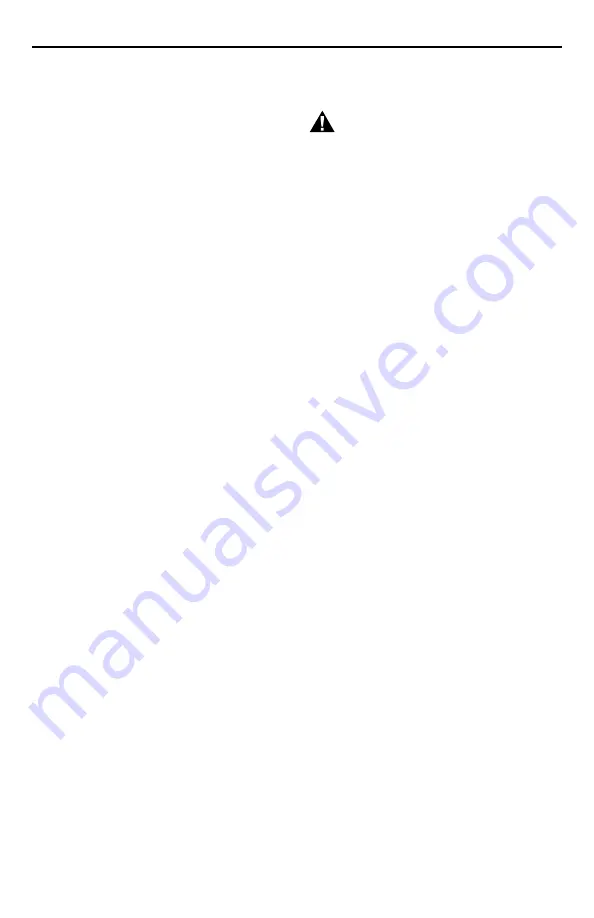
69-0845—2
14
S8910U UNIVERSAL HOT SURFACE IGNITION MODULE
Trial for Ignition
At the end of the warmup period, the gas control opens for
the ignition trial time determined by the selection tab. The
hot surface igniter stays powered for an ignition activation
period of one second if the four-second trial time is used or
four seconds if the seven-second trial time is used. The
igniter turns off after the ignition activation period. Near the
end of the ignition trial time, the flame rectification sensing
circuit determines if the main burner flame is present. If so,
the gas control remains open and the burner operation
phase begins.
Burner Operation
When the main burner is lit, a flame rectification circuit is
completed between the flame sensor (igniter on local
sense systems or flame rod on remote sense systems)
and the main burner (burner ground). The S8910U flame
sensing circuit detects the flame current and holds open
the gas control. The main flame is monitored continuously
during the call for heat.
Safety Shutdown
One Trial Selection Tabs (A and C)
If flame is not sensed by the end of the timed trial for
ignition, the gas control closes and the module locks out. It
must be manually reset by removing power or setting the
thermostat below the room temperature for at least 30
seconds.
If the burner lights and flame is proved but goes out during
the run cycle, the gas control closes and the module
initiates a warmup period followed by one trial for ignition.
If flame is not established, the gas control closes and the
module locks out, requiring manual reset.
Three Trial Selection Tabs (B and D)
If flame is not sensed by the end of the first timed trial for
ignition, the gas control closes and the module initiates a
second 96 seconds between trial purge cycle, followed by
igniter warmup and a second trial for ignition. If flame is not
established, the between trial purge, warmup, trial for
ignition cycle is repeated a third time. If flame is still not
established following the third trial, the gas control closes
and the module locks out. It must be manually reset by
removing power or setting the thermostat below the room
temperature for at least 30 seconds.
If the burner goes out during the run cycle, the gas control
closes and the module checks for the number of ignition
trials performed during the current call for heat. If the
number is less than three, the module initiates a between
trial purge, warmup and trial for ignition. After the third trial
during a single call for heat, the module locks out. The
module must be manually reset following the lockout.
MAINTENANCE
WARNING
FIRE OR EXPLOSION HAZARD
CAN CAUSE PROPERTY DAMAGE,
SEVERE INJURY, OR DEATH.
Do not attempt to take apart the module or to clean
it. Improper assembly and cleaning can cause
unreliable operation.
Regular preventive maintenance is important in applica-
tions that place a heavy load on system controls such as
those used in the commercial cooking and agricultural and
industrial industries because:
•
In many such applications, particularly commercial
cooking, the equipment operates 100,000 to 200,000
cycles per year. Such heavy cycling can wear out the
gas control in one to two years.
•
Exposure to water, dirt, chemicals and heat can
damage the gas control and shut down the control
system. A NEMA 4 enclosure can reduce exposure to
environmental contaminants. See Electronic Ignition
Service manual, form 70-6604.
The maintenance program should include regular check-
out of the system as outlined in the Startup and Checkout
section, and checkout of the control system as described
in the appliance manufacturer literature.
Maintenance frequency must be determined individually
for each application. Some considerations are:
•
Cycling frequency. Appliances that may cycle 20,000
times annually should be checked monthly.
•
Intermittent use. Appliances that are used seasonally
should be checked before shutdown and again before
the next use.
•
Consequence of unexpected shutdown. Where the cost
of an unexpected shutdown would be high, the system
should be checked more often.
•
Dusty, wet, or corrosive environment. Because these
environments can cause the gas control to deteriorate
more rapidly, the system should be checked more
often.
Any control should be replaced if it does not perform
properly on checkout or troubleshooting. In addition,
replace any module if it is wet or looks like it has ever been
wet. Protective enclosures, as described in the Planning
the Installation section, are recommended regardless of
checkout frequency.
TROUBLESHOOTING
IMPORTANT
1. The following service procedures are provided
as a general guide. Follow appliance manu-
facturer service instructions if available.
2. Meter readings between gas control and
ignition module must be taken within the trial
for ignition period. Once the ignition module
shuts off, wait for retry or reset at the thermo-
stat.
3. If any component does not function properly,
make sure it is correctly installed and wired
before replacing it.