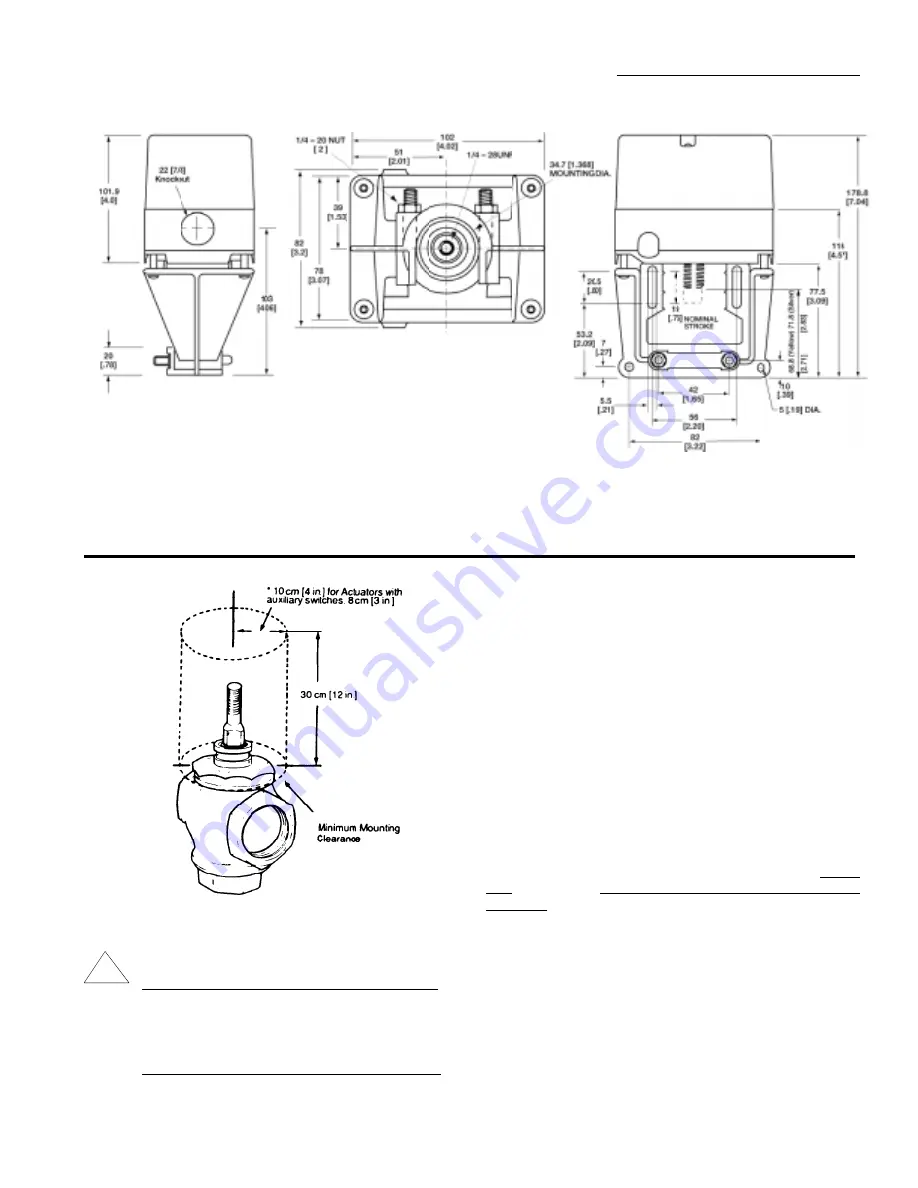
Installation
ML7984B
SPECIFICATIONS •INSTALLATION
FIG. 1 -- DIMENSIONS OF ML7984 VALVE ACTUATOR IN MM (INCHES).
FIG.2 -- MINIMUM MOUNTING CLEARANCE.
!
CAUTION
1. Installer must be a trained service technician.
2. DO NOT electrically operate the ML7984
before assembly to the valve because damage
not apparent to the installer may occur.
2. Although the actuator can be mounted in any position, it is
preferable that the ML7984 is mounted above the valve body.
This will minimize the risk of damage to the ML7984 in the
Mounting:
1.Ensure that the valve body is installed correctly, that is, the
arrow points in the direction of the flow.
event of condensation or a valve gland leak.
3. Remove the stem button (Fig. 3) from the valve stem.
4. Slide the position indicator (plastic disk or rubber O-ring)
over the valve stem. (See inset, Fig. 3) Indicator will self
align to the marking on the yoke after one complete operating
cycle.
Assembly of ML7984 to the valve:
1. The drive shaft of the ML7984 has a threaded hole to link
with the valve stem. Slide the yoke over the valve bonnet
(Fig. 4)
2. Thread the ML7984 drive shaft onto the valve stem all the
way, until it is completely attached (with no threads
showing), by turning the valve actuator in a clockwise
direction, as viewed from above (depending on the valve
models, use a pin or wrench to keep valve stem from turning).
Note that the valve actuator is shipped with drive shaft in the
mid-position.
4. Orient the conduit hole to the most desirable direction, then
tighten the LOCKNUTS on the U-bolt.
3. Care should be exercised when using the TOOLS on the
valve stem during tightening. (Fig.4) DO NOT damage the
threads or other parts of the stem.
3