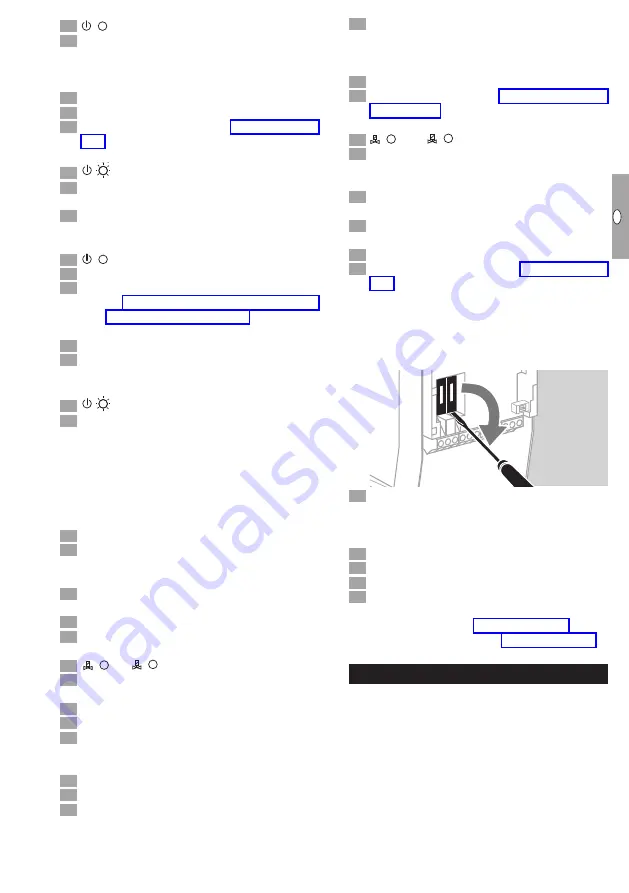
GB-9
D
GB
F
NL
I
E
?
1
2
Power
yellow and permanently lit?
!
Safety interlock input signal is interrupted, no
voltage at terminal 5. The tightness test is still
being carried out. No enable signal is issued to
the automatic burner control unit.
•
Check safety interlocks.
!
Fuse F2 defective.
•
Replace fuse F2, see page 9 (Replacing the
fuse).
?
1
2
Power
yellow and flashing?
!
Permanent remote reset. The remote reset signal
has been active for more than 10 s.
•
The warning signal is cancelled once the remote
reset signal to terminal 11 has been removed.
?
1
2
Power
red and permanently lit?
!
Incorrect jumper/DIP switch setting.
•
Correct jumper and DIP switch setting, see
pages 7 (Setting measurement time tM)
and 6 (Setting the test instant). Then press
the reset button.
!
Internal error.
•
Remove the unit and return it to the manufacturer
for inspection.
?
1
2
Power
red and flashing?
!
Too frequent burner start commands. The TC
performs a fault lock-out. The start commands
are limited to 5 x in 15 minutes.
▷
As long as this limit is not exceeded, another
start-up attempt is possible after three further
minutes. If a tightness test is completed, the
counter which limits the number of start com-
mands is reset.
•
Then press the reset button.
!
Too many remote resets. More than 5 resets
have been conducted within the last 15 minutes,
either automatically or manually.
!
Consecutive fault caused by a previous fault
whose actual cause has not been remedied.
•
Pay attention to previous fault messages.
•
Remedy cause. Then press the reset button.
?
1
2
Power
or
1
2
Power
red and permanently lit?
!
The valve is leaking. The TC performs a fault
lock-out.
•
Replace the valve.
!
Wiring of the TC to the valves is faulty.
•
Start the program and observe the interspace
pressure p
z
. The pressure must change during
the TEST phase. Check the wiring.
!
Inlet pressure p
u
< 10 mbar.
•
Provide the min. inlet pressure of 10 mbar.
!
Interspace pressure p
z
cannot be reduced.
•
The volume downstream of the valve on the
burner side must be 5 times higher than the
volume between the valves and atmospheric
pressure must prevail.
!
The measurement time t
M
is too long.
•
Readjust t
M
, see page 7 (Setting measure-
?
1
2
and
1
2
Power
red and permanently lit?
!
During the tightness test, the TC has determined
that inlet valve 1 and outlet valve 2 have been
reversed (fault lock-out).
•
Check the wiring. Then press the reset button.
? No LED lit even though mains voltage ap-
plied?
!
Fuse F1 defective.
•
Replace fuse F1, see page 9 (Replacing the
fuse).
Replacing the fuse
▷
The fuses F1 and F2 can be removed for in-
spection.
▷
Insert a screwdriver into the opening in the con-
tact guard to prise out the fuse.
Disconnect the TC from the electrical power
supply.
▷
Before opening the unit, the fitter should ground
himself.
Unscrew the housing cover.
Remove fuse F1 or F2.
4
Check function of fuse.
5
Replace the defective fuse.
▷
When replacing the fuse, use only the approved
fuse type, see page 10 (Technical data).
▷
Restart the TC, see page 8 (Commissioning).
Maintenance
Tightness controls TC require little servicing. We rec-
ommend carrying out a function check once a year
or twice a year in the case of biogas.