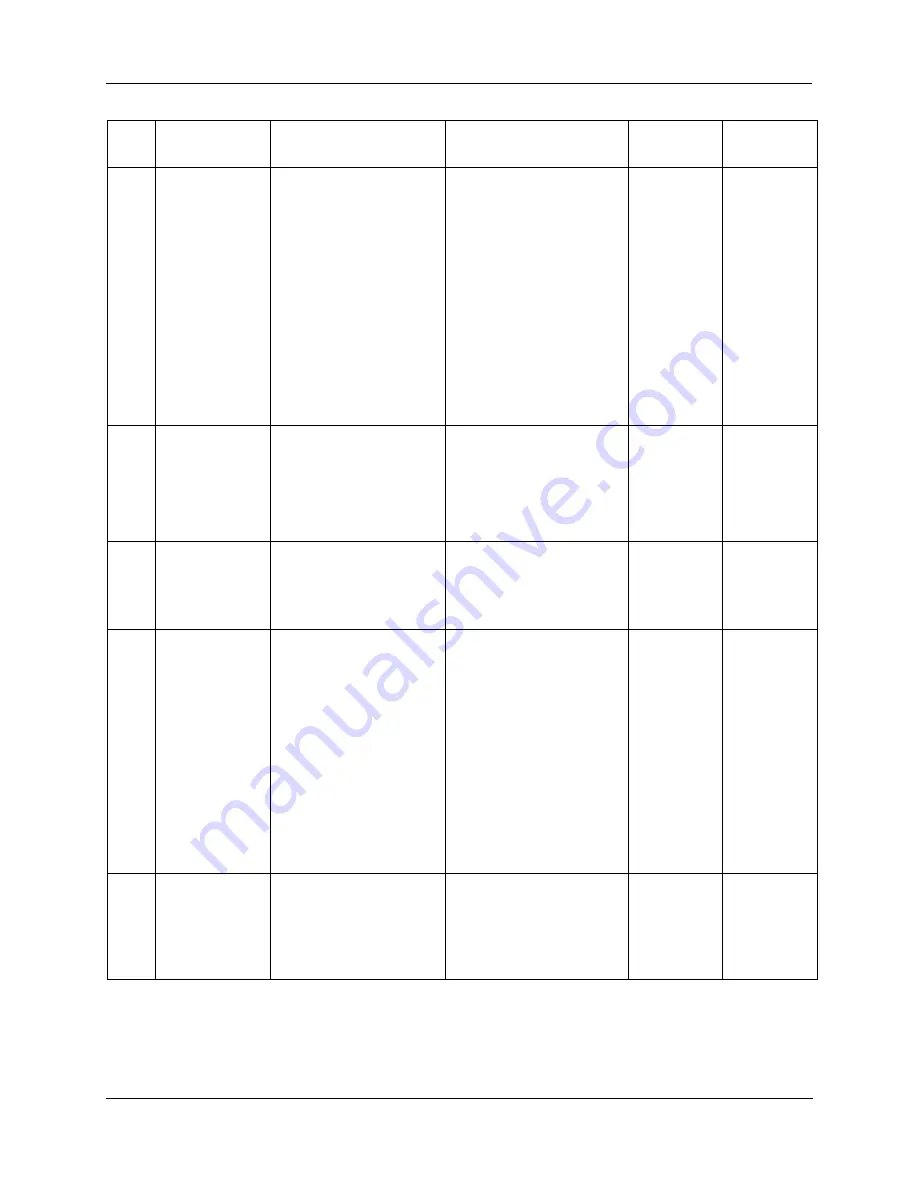
Revision 6
HC900 Process & Safety Controller User and Installation Manual
177
21 April 2017
Number
of Red
Strobes
Possible Causes
Lead and/or Reserve Controller
Action(s)
User Action
Honeywell OI
Indication
HCDesigner/HC
Utilities Indication
2
There are slave blocks
in the configuration,
and no communication
port is configured as a
Modbus master.
MSTRFAIL pins on ASYS and
FSYS blocks turn on.
All Modbus slave and Modbus
read blocks freeze their output
pins to the last value.
All slave blocks have their BAD
COMM pin on.
All slave blocks have their NO
SCAN pin on.
IN SCAN STATUS is set to NO
for all slaves.
COMM STATUS is set to BAD
for all slaves in the function block
diagram.
Statistical counters for all slaves
are 0.
1. Use the OI, HCDesigner, or
HCUtilities to configure one of the
serial ports (S1 or S2) as a master.
2. Use the OI, HCDesigner, or
HCUtilities to download a
configuration that has no slave
blocks.
2
Controller mode is
changed to RUN-
Locked while there are
forces present on
safety worksheet.
Controller will not go to RUN-
Locked mode.
To clear the diagnostic:
1. Change mode back to RUN
mode OR
2. Clear all safety forces using HCD
through Monitor->Forced
Blocks OR
3.
Force a cold-start
In HCD, "System
Diagnostics"
shows status as
"Invalid Change of
Mode"
2
Controller mode is
changed to RUN-
Locked when safety
configuration is
changed at run-time.
Controller will not go to RUN-
Locked mode.
7.
To clear the diagnostic:
8.
1. Change mode back to RUN
mode OR
2. Force a cold-start
In HCD, "System
Diagnostics"
shows status as
"Safety
Configuration mis
match"
3
One of the following
microprocessor
exceptions occurred:
Watchdog timer
timeout
Address error
Prefetch error
Data abort error
Software interrupt
Undefined
instruction error
At the time of the exception, the
microprocessor resets. If it’s the
Lead controller, and there is an
available reserve, a failover occurs.
When the microprocessor
completes its reset condition, it will
become an available reserve if a
lead is present or become a lead if
no lead is present.
This diagnostic will cause the
HWOK
pins of the AYSY and FSYS
blocks to be turned off.
To clear the diagnostic, force a cold
start.
If the problem reoccurs, try the
following:
1. Ensure the system is properly
grounded
2. Ensure the system is properly
isolated from external noise sources
3. Upgrade the firmware
4. Replace the CPU board.
5. Contact Honeywell Personnel.
If the lead’s status
LED is indicating
the failure, see
CPU
in the “Lead
CPU Diagnostics”
display.
If the reserve’s
status LED is
indicating the
failure, see
CPU
in
the “Reserve CPU
Diagnostics”
display.
If the lead’s status
LED is indicating
the failure, see
CPU Diagnostics
in the “Lead
Diagnostics
Overview” dialog
box.
If the reserve’s
status LED is
indicating the
failure, see
CPU
Diagnostics
in
the “Reserve
Diagnostics
Overview” dialog
box.
3
One of the exception
vectors located in RAM
became corrupted.
The exception vector was
automatically corrected in the
controller’s RAM and the controller
continues to operate normally.
This diagnostic will cause the
HWOK
pins of the AYSY and FSYS
blocks to be turned off.
Summary of Contents for HC900
Page 5: ...Revision 6 HC900 Process Safety Controller User and Installation Manual v 21 April 2017 ...
Page 6: ......
Page 30: ......
Page 140: ......
Page 186: ......