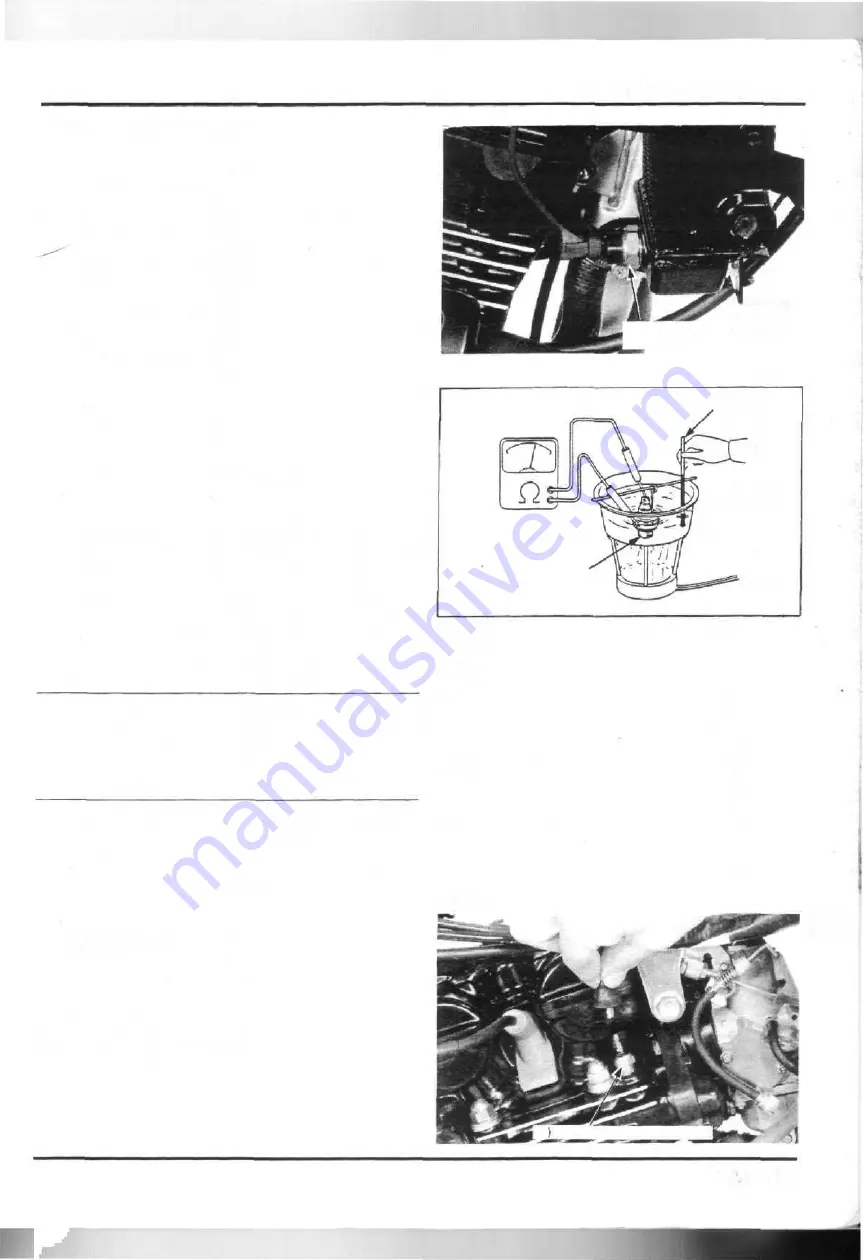
LIGHTS/METERS/SWITCHES
THERMOSTATIC SWITCH
The cooling fan motor is actuated by the thermostatic switch
located in the bottom of the radiator.
If the fan motor does not start, disconnect the 2P: Black con-
nector from the switch.
Connect together Black/Blue and Green terminals of the 2P
connector with a suitable jumper wire.
Turn the ignition switch ON. The cooling fan motor should
start running. If it does not start, check for battery voltage
from the Black/Blue lead of the fan motor connector and
ground with ignition switch ON.
If there is no voltage, check for a blown fuse, loose terminals
or connectors, or an open circuit.
If there is voltage, inspect the thermostatic switch as follows:
Drain the coolant (page 5-4) and remove the thermostatic
switch.
Connect one lead of an ohmmeter to the connector of the
thermostatic switch and the other to the body.
Suspend the thermostatic switch in a pan of coolant (50 — 50
mixture) and check the temperatures at which the switch
opens and closes.
Make sure that there is no continuity at room temperature and
then gradually raise the coolant temperature. The switch
should show continuity (close) at 93°—97°C (199° —
207°F}.
NOTE
• Keep the temperature for 3 minutes to confirm continuity.
A sudden change of temperature will Cause an incorrect
temperature reading between the thermometer and switch.
• Do not let the switch or thermometer touch the pan as it will
give a false reading.
• Immerse the switch in coolant up to its threads.
Install the thermostatic switch.
TORQUE: 18 N*m (1.8 kg-m, 13ft-lb)
Fill the cooling system (page 5-4),
TEMPERATURE SENSOR
Disconnect the Green/Blue wire from the temperature sensor.
Check for continuity between the sensor body and ground.
There should be continuity.
If there is no continuity, check the thermostat housing for
looseness and recheck.
( 1 | THERMOSTATIC
SWITCH
(1) THERMOMETER
(2) THERMOSTATIC
SWITCH
(1 TEMPERATURE SENSOR
19-9
•
Summary of Contents for NX250 1989
Page 1: ...NX250 1989...
Page 2: ......
Page 3: ......
Page 4: ......
Page 5: ......
Page 6: ......
Page 7: ......
Page 8: ......
Page 9: ......
Page 10: ......
Page 11: ......
Page 12: ......
Page 13: ......
Page 14: ......
Page 15: ......
Page 16: ......
Page 17: ......
Page 18: ......
Page 19: ......
Page 20: ......
Page 21: ......
Page 22: ......
Page 23: ......
Page 24: ......
Page 25: ......
Page 26: ......
Page 27: ......
Page 28: ......
Page 29: ......
Page 30: ......
Page 31: ......
Page 32: ......
Page 33: ......
Page 34: ......
Page 35: ......
Page 36: ......
Page 37: ......
Page 38: ......
Page 39: ......
Page 40: ......
Page 41: ......
Page 42: ......
Page 43: ......
Page 44: ......
Page 45: ......
Page 46: ......
Page 47: ......
Page 48: ......
Page 49: ......
Page 50: ......
Page 51: ......
Page 52: ......
Page 53: ......
Page 54: ......
Page 55: ......
Page 56: ......
Page 57: ......
Page 79: ......
Page 80: ......
Page 81: ......
Page 82: ......
Page 83: ......
Page 84: ......
Page 85: ......
Page 86: ......
Page 87: ......
Page 88: ......
Page 89: ......
Page 90: ......
Page 91: ......
Page 92: ......
Page 93: ......