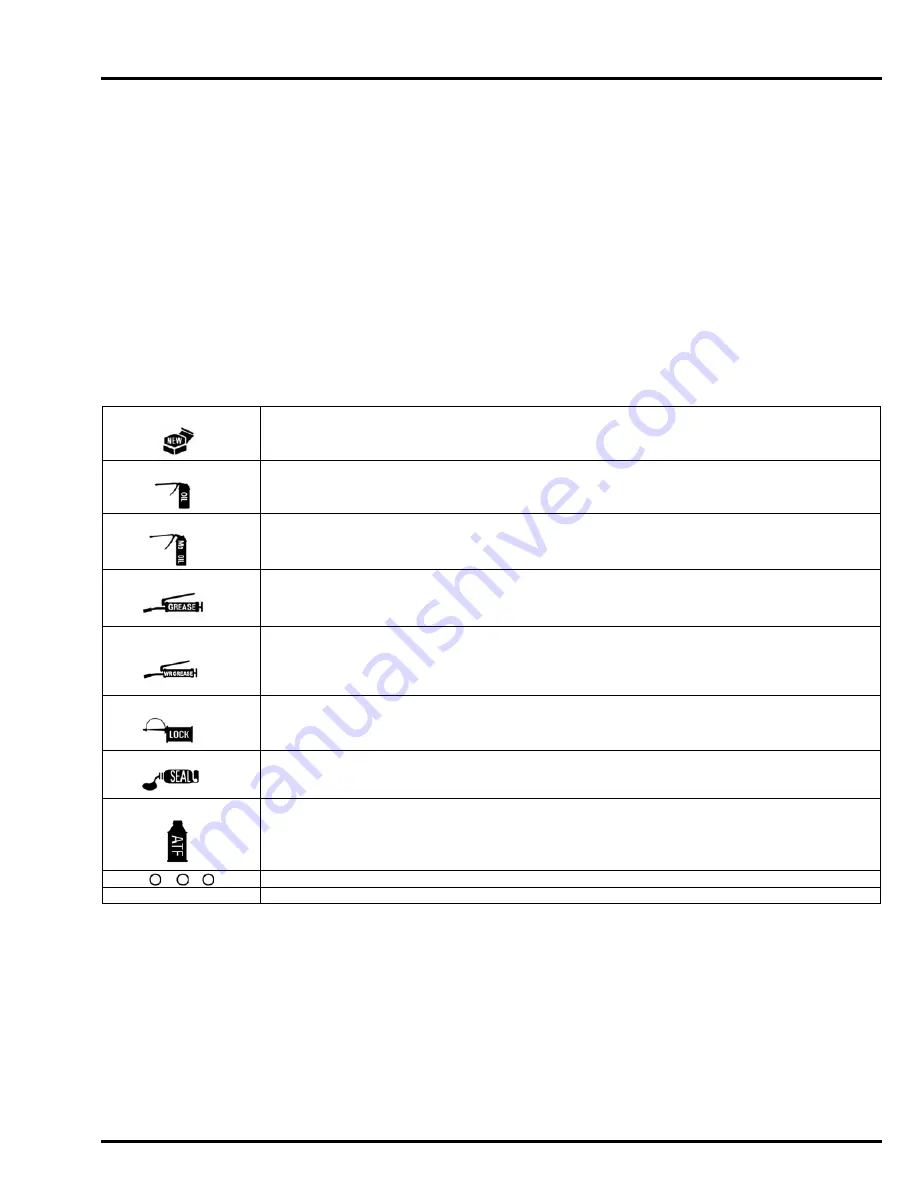
0-4
dummyhead
dummyhead
How to use this manual
SERVICE RULES
• Use Honda Genuine or Honda-recommended parts and lubricants or their equivalents. Parts that do not meet Honda’s design
specifications may damage the unit.
• Use the special tools designed for the product.
• Install new gaskets, O-rings, etc. when reassembling.
• When torquing bolts or nuts, begin with larger-diameter or inner bolts first and tighten to the specified torque diagonally, unless
a particular sequence is specified.
• Clean parts in cleaning solvent upon disassembly. Lubricate any sliding surfaces before reassembly.
• After reassembly, check all parts for proper installation and operation.
• Many screws used in this machine are self-tapping. Be aware that cross-threading or overtightening these screws will strip the
threads and ruin the hole.
Use only metric tools when servicing this unit. Metric bolts, nuts and screws are not interchangeable with non-metric fasteners. The
use of incorrect tools and fasteners will damage the unit.
SYMBOLS
The symbols used throughout this manual show specific service procedures. If supplementary information is required pertaining to
these symbols, it will be explained specifically in the text without the use of the symbols.
Replace the part(s) with new one(s) before assembly.
Use the recommend engine oil, unless otherwise specified.
Use molybdenum oil solution (mixture of the engine oil and molybdenum grease in a ratio of 1:1).
Use multi-purpose grease (lithium based multi-purpose grease NLGI #2 or equivalent).
Use marine grease (water resistant urea based grease).
Apply a locking agent. Use a medium strength locking agent unless otherwise specified.
Apply sealant.
Use automatic transmission fluid.
( x ) ( )
Indicates the diameter, length, and quantity of metric bolts used.
page 1-1
Indicates the reference page.