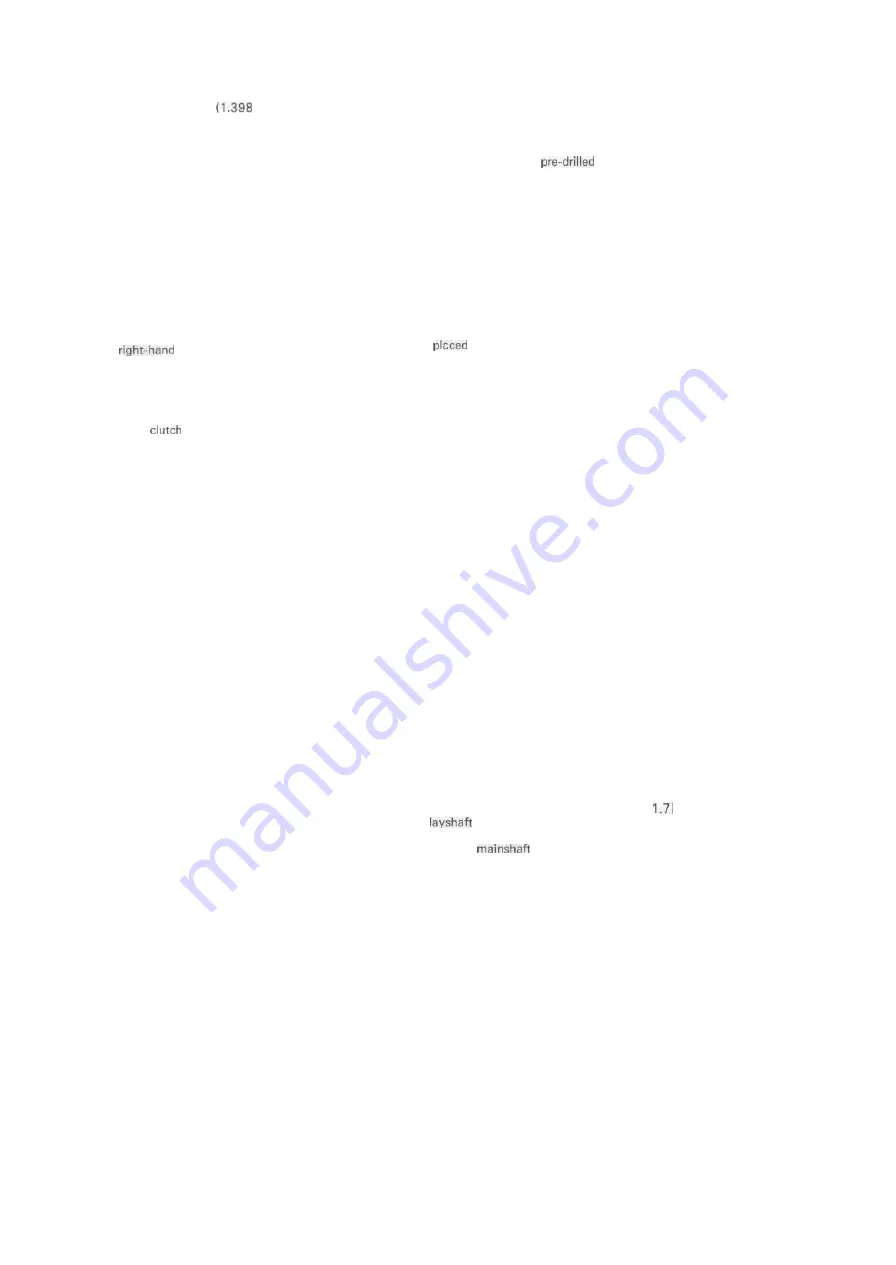
Chapter 1 Engine, clutch and gearbox
35
4 Measure the uncompressed length of the clutch springs
which should be 35.5 mm
in) when new. Should any
spring have settled to the specified service limit or shorter, all
four springs should be renewed as a set.
5 Check the condition of the thrust bearing assembly and
pushrod, which are located in the clutch centre. Excessive play
or wear will cause noise and erratic operation.
6 Check the condition of the slots in the outer surface of the
clutch centre and the inner surfaces of the outer drum. In an
extreme case, clutch chatter may have caused the tongues of
the inserted plates to make indentations in the slots of the outer
drum, or the tongues of the plain plates to indent the slots of the
clutch centre. These indentations will trap the clutch plates as
they are freed, and impair clutch action. If the damage is only
slight the indentations can be removed by careful work with a
file and the burrs removed from the tongues of the clutch plates
in a similar fashion. More extensive damage will necessitate
renewal of the parts concerned.
7 The clutch release mechanism attached to the inside of the
crankcase
cover takes the form of a vertical spindle
with a cam on the lower end. A light return spring ensures that
pressure is taken off the end of the pushrod once the handlebar
lever has been released. No attention is normally required, other
than greasing prior to reassembly.
8 The primary drive is by means of a crankshaft-mounted
gear driving the
by way of teeth on the outer drum. The
two gears should be examined for signs of wear or chipped
teeth, and replaced as necessary, preferably as a pair.
29 Examination and renovation: gearbox components
1 Examine each of the gear pinions to ensure that there are
no chipped or broken teeth and that the dogs on the end of the
pinions are not rounded. Gear pinions with these defects must
be renewed; there is no satisfactory method of reclaiming them.
2 Examine the selector forks carefully, ensuring that there is
no scoring or wear where they engage in the gears, and that
they are not bent. Damage and wear rarely occur in a gearbox
which has been properly used and correctly lubricated, unless
very high mileages have been covered.
3 The tracks in the selector drum, which co-ordinate the
movement of the selector forks, should not show signs of undue
wear. Check also that the detent arm spring has not weakened,
and that no play has developed in the gear selector linkages.
4 Unless the unit has shown signs of wear or malfunctioning,
it is unnecessary to dismantle the kickstart assembly. It is
however, a very simple unit to deal with.
5 Check the movement of the gear on the spiral which brings
it into engagement with the coupling gear. Look for chipped or
broken teeth and excessive wear, replacing the gear if
necessary.
30 Engine casings and covers: examination and repair
1 The aluminium alloy casings and covers are unlikely to
suffer damage through ordinary use. However, damage can
occur if the machine is dropped, or if sudden mechanical
breakages occur, such as the rear chain breaking.
2 Small cracks or holes may be repaired with an epoxy resin
adhesive, such as Araldite, as a temporary expedient. Per-
manent repairs can only be effected by argon-arc welding, and a
specialist in this process is in a position to advise on the viability
of proposed repair. Often it may be cheaper to buy a new
replacement.
3 Damaged threads can be economically reclaimed by using a
diamond section wire insert, of the Helicoil type, which is easily
fitted after drilling and re-tapping the affected thread. The
process is quick and inexpensive, and does not require as much
preparation and work as the older method of fitting brass, or
similar inserts. Most motorcycle dealers and small engineering
firms offer a service of this kind.
4 Sheared studs or screws can usually be removed with
screw extractors, which consist of tapered, left-hand thread
screws, of very hard steel. These are inserted by screwing anti-
clockwise, into a
hole in the stud, and usually
succeed in dislodging the most stubborn stud or screw. The only
alternative to this is spark erosion, but as this is a very limited,
specialised facility, it will probably be unavailable to most
owners. It is wise, however, to consult a professional engineer-
ing firm before condemning an otherwise sound casing. Many
of these firms advertise regularly in the motorcycle papers.
31 Engine reassembly: general
1 Before reassembly of the engine/gear unit is commenced,
the various component parts should be cleaned thoroughly and
on a sheet of clean paper, close to the working area.
2 Make sure all traces of old gaskets have been removed and
that the mating surfaces are clean and undamaged. One of the
best ways to remove old gasket cement is to apply a rag soaked
in methylated spirit. This acts as a solvent and will ensure that
the cement is removed without resort to scraping and the con-
sequent risk of damage.
3 Gather together all the necessary tools and have available
an oil can filled with clean engine oil. Make sure all the new
gaskets and oil seals are to hand, also all replacement parts
required. Nothing is more frustrating than having to stop in the
middle of a reassembly sequence because a vital gasket or
replacement has been overlooked.
4 Make sure that the reassembly area is clean and that there
is adequate working space. Many of the smaller bolts are easily
sheared if over-tightened. Always use the correct size
screwdriver bit for the crosshead screws and never an ordinary
screwdriver or punch. If the existing screws show evidence of
maltreatment in the past, it is advisable to renew them as a
complete set.
5 If the purchase of a replacement set of screws is being con-
templated, it is worthwhile considering a set of socket or Allen
screws. These are invariably much more robust than the
originals, and can be obtained in sets for most machines, in
either black or nickel plated finishes. The manufacturers of
these screw sets advertise regularly in the motorcycle press.
32 Engine reassembly: gear clusters and selector
mechanism reassembly and replacement
1 Having examined and renewed the gearbox components as
necessary, the clusters can be built up and assembled as a com-
plete unit for installation in the engine/gearbox casings.
2 Study the line drawing carefully (Fig.
and assemble the
components in the exact order shown, ensuring that
the thrust washers and circlips are correctly positioned. The
gearbox
(input shaft) should be tackled in a similar
manner. See also the accompanying photographic sequence.
33 Engine reassembly: replacing the crankcase components
1 Place the larger, left-hand, crankcase half on blocks on the
workbench, checking that a reasonable amount of room is
allowed for the shafts to protrude when fitted. The gearbox
mainshaft and layshaft clusters should be placed into position
first, ensuring that the shim fitted on the mainshaft end is not
omitted. The selector forks, having previously been fitted to
their pivot shaft, can now be placed in position. This operation
calls for a certain amount of patience, as the three forks must be
eased into their respective grooves before the pivot shaft will
locate correctly.