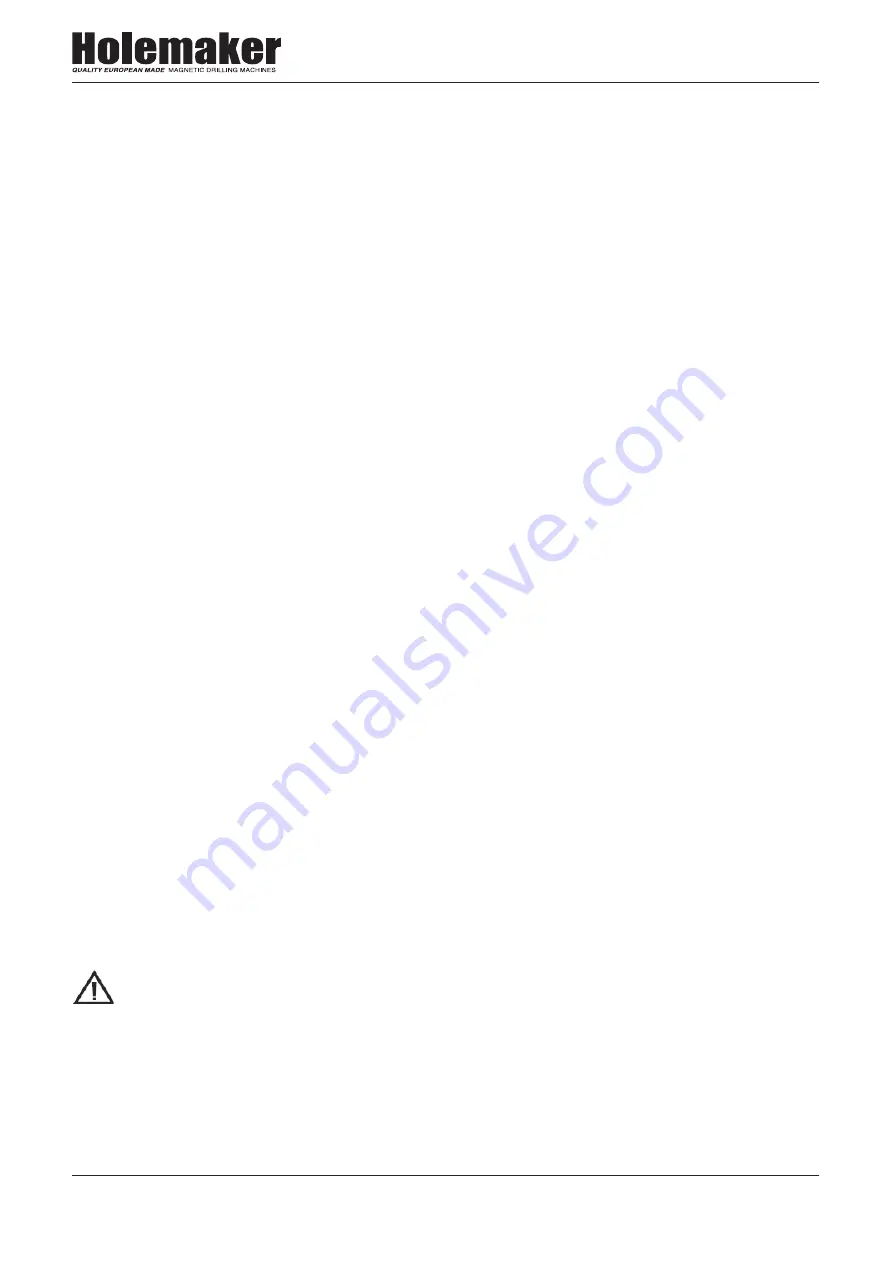
®
HMPRO200A OPERATOR’S MANUAL
14
www.holemaker.com
Select the proper annular cutter, drill bit, or screw tap based on the hole size desired. Next,
use a clean and dry cloth to wipe the spindle, arbor (drill bit, tap chuck), and cutter, and
then install the arbor (and then the cutter), drill bit, or tap chuck (and then the screw tap with
adapter) as described before.
Position the machine on a flat ferromagnetic workpiece with a thickness of at least
13 mm (0.5’’). The workpiece must be clean, without rust or paint that decrease the holding
force of the magnets. Some types of steel are non-ferromagnetic (do not conduct magnetic
flux) and the magnets are not capable to clamp onto them.
Clamp the magnets by rotating their levers to the left (2) as far as possible, and then
lock the levers in this position with the lock pin 3. The maximum holding force is achieved
when the bottom of each magnet is in full contact with the workpiece.
When working on pipes, use the 6 mm hex wrench to loosen eight screws 4, set the
magnets at the desired angle, position the machine on the pipe, tighten the screws, and
clamp the magnets.
Use the 10 mm hex wrench to loosen four screws 5, and then adjust the position of the
machine using adjustment screw 6.
Press the lever lock 7 and set the lever 8 in the horizontal (‘0’) position, and then
connect the machine to a correctly prepared air source of sufficient purity using the air fitting 9
and a hose with the inner diameter of at least 20 mm (0.8’’; and 18 mm (0.7’’) for fittings). The
air source must be equipped with an air preparation unit: a filter, regulator, and lubricator. The
flow capacity of the air preparation unit must not be less than 4000 l/min.
Rotate the spoke handles to the left to place the tool above the workpiece.
When using the annular cutter, install the cooling system by attaching the bottle
hose to the fitting (10), and then fill the bottle with a cutting fluid. Do not use pure water
as the cutting fluid. However, using emulsions formed from mixing water and drilling oil
is satisfactory. Next, rotate the handle 11, and move it up-down several times to build a
pressure inside the bottle. Then, check the operation of the cooling system. To do this, open
the valve 12, and then rotate the spoke handles to the left to initially apply pressure on the
pilot pin, which should result in the fluid filling the system and flowing from the inside of the
cutter.
2.6. Drilling
Set the second gear, and then press the lever lock and set the lever to the lower position
to start the motor. Slowly rotate the spoke handles to the left to bring the tool close to the
workpiece, and begin drilling.
When using annular cutters, drill holes in one pass.
When the annular cutter goes through the material, the slug core is expelled from the
cutter with a significant force.
When using drill bits, drill large holes in two passes. Drill a first hole using a drill bit with
a diameter smaller than the diameter of the hole size desired, and then drill again using the bit
with diameter equal to the hole size desired.
When drilling holes deeper than 50 mm (2’’), retract the tool above the workpiece