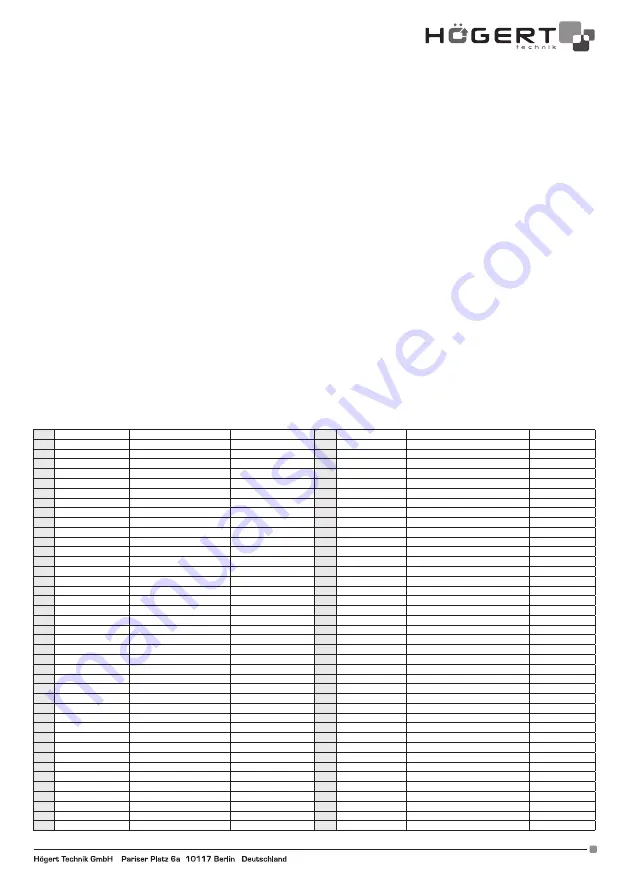
11
Adres producenta/ Adresse des Herstellers/ Manufacturer’s Address/ Адрес производителя
GTV Poland Sp. z o.o. Sp. k., ul. Przejazdowa 21, 05-800 Pruszków. www.hoegert.com
PREPARATION BEFORE USING THE DEVICE
Switch on the air compressor, have 6 to 8 Bar compressed air in preparation.
Screw off the dishing houslong screws beside the two sides of tank cover. Tilt the handles of body with the tank cover, grease injection
pump and grease pressing device to an angle of 20 to 30 degrees. To let air enter through the bottom of oil pressure rubber board. It is
convenient to pul lit out without the necessity of uninstalling any parts.
The maximum capacity of lubricant grease to be installed in grease storage tank is 12 kg. Full instalation is depending on requirement.
To prevent the buble from creating, the grease should be pressed and Surface should be planed.
The handles of cars with the cover, grease injection pump and grease pressing devices are placed vertically into the grease storage
tank. Press the rubber board tightly on the grease surface. Insert the grease inlet pipe into the bottom of the cabinet, screw on the
dishing tightening screw beside the tank cover. Install the quick replacing connector in the air source pipe.
The grease injection pump and grease injection gun are connected by the high pressure pipe. The cleaning job should be finished
during the connection. At the beginning of the grease injection pump the grease gradually filled in the pipe of plung piston pump. The
grease pressure also increasing gradually after working project. The velocity of reciprocating motion of grease injection pump decre-
ased. Till the final stop, then the inner pressure of pump reaches the equilibrium. The pressure also reaches the maximum value this
time. If trigger of grease injection pump is pulled, high pressure will inject from the gun. When the grease filled in the pipe of plunge
piston pump again. The grease pressure also reaches the maximum value and the grease injection pump stops the reciprocating
motion. The grease injection pump is thus working discontinuously.
At the time of grease injection pump stop the reciprocating motion highest grease pressure it is necessary to check all connecting
parts to ensure noleak exist.
MAINTENACE EQUIPMENT
1. The compressed air should be filtrated to keep the dirt in air from entering the air pump to abrade the air supply sliding block,
cylinder etc.
2. The compressed air should not sulpass 8 Bar, so as to prevent overloading and effect the longevity of high pressure pipe.
3. While using the high pressure pipe forcing bending and heavy loading is forbidden to prevent damage.
4. During the rest time, the quick replacing connector should be uninstalled and pull trigger of grease injection gun to emit the grease,
so as to decrease the inner grease pressure of the equipment to extend the longevity of high pressure pipe.
5. Lubricant grease should be injected into the air pump regularly.
6. In the disassembling proces, avoid the touching of each part to keep the accuracy of the disassembled parts.
7. Do not run the machine without loads while the grease is insifficent in storage tank, so as to prevent heating the plunge piston pump
to damage parts.
8. Cleaning and maintenance job should be done regularly.
GREASE INJECTOR PART LIST
1
RH2121-D-004
Air tube
42
RH1121-12
Check valve
2
RH1121-02
Air tube Nut
43
RH1121-11
Check valve gasket
3
GB3452.1-1992
O type seal ring
Ø7.5 x 2.65 mm
44
RH1121-13
Grease inlet valve seating
4
RH1121-03
Bend connector
45
RH1121-14
Overflow ring
5
RH1121-04
Cylinder cover
46
RH2121-D-005
Loading board
6
GB3452.1-1992
O type seal ring
Ø 70 x 3.1 mm
47
GB/T 859-1987
Spring gasket
Ø 6 mm
7
GB/T 6175-2000
Turret Nut
48
GB/T 6175-2000
Turret Nut
8
RH1121-07
Piston Gasket
49
RH2121-D-003
Grease inlet pipe
9
RH1121-06
Piston
50
RH1121-53
Purplr copper gasket
10
RH1121-05
Cylinder
51
RH1121-15
Grease outlet connector
11
RH1121-08/26
Piston pole module
52
GB/T 65-2000
Deck bolt
12
RH1121-09
Seal screw
53
GB/T 859-1987
Spring gasket
Ø 4 mm
13
GB3452.1-1992
O type seal ring
Ø 16 x 2.4 mm
54
RH1121-22
Damping spring
14
GB3452.1-1992
O type seal ring
Ø 20 x 1.8 mm
55
RH1121-21
Gas-supplier slide block
15
RH1121-11
Reverse valve
56
RH1121-20
Clapboard
16
RH1121-12
Valve sleeves
57
RH1121-19
Gas-supplierseatlng
17
RH1121-13
Reverse spring
58
RH1121-52
Paper gasket
18
GB3452.1-1992
O type seal ring
Ø 17 x 2.65 mm
59
RH2121-D-002
Gas supplier rover
19
RH1121-14
Slide seating
60
GB/T70.1-2000
Inside hexangular cylinder head bolt
20
RH2121-D-001
Gas supplier
61
GB3452.1-1992
O type seal ring
Ø 46 x 2.50 mm
21
RH1121-23
Pulling sheath
62
RH1121-25
Ąir·inlet connector
22
RH1121-17
Sealing gasket
63
GB3452.1-1992
O type seal ring
Ø 45.3 x 2.65 mm
23
GB3452.1-1992
O type seal ring
Ø 16 x 1.80 mm
64
RH2121-D-006
Muffler
24
GB3452.1-1992
O type seal ring
Ø 11.2 x 1.80 mm
65
RH1121-16
Learning oil caul king
25
RH1121-18
U seal ring
UN 12 x 22 x 8 mm
66
GB 894-86
Axis Cir Ciip
Ø 30 mm
26
RH1121-27
Sealing cover
67
RH1121-18
Hand butter
27
GB/T 91-2000
Dowel
Ø 3 x 20 mm
68
RH1121-19
Top cap
28
GB/T 879-2000
Dowel
Ø 3 x 15 mm
69
GB/T 5783-2000
Hexangular head stud bolt
M8 x 15 mm
29
RH1121-02
Adjust nut
70
RH1121-51
Presses Oil Spring
30
RH1121-03
Connectlng pole
71
RH1121-A-55
Presses oil disk
31
RH1121-04
Grease inlet spring
72
GB3452.1-1992
O type seal ring
Ø 35 x 2.50 mm
32
GB 308-89
Steel bali
Ø 6 mm
73
RH1121-22
Butterfly shaped nut
33
RH1121-05
Plunger piston pole
74
RH1121-30
ShacKle
34
RH1121-06
Spring seating
75
GB/T 6184-2000
Nylon Nut
35
RH2121-07/08
Loading pole module
76
GB/T 5783-2000
Hexangular head stud bolt
M6 x 16 mm
36
GB3452.1-1992
O type seal ring
Ø 24 x 2.40 mm
77
RH1121-23
Butter Tank
37
RH1121-30
Connecting pipe
78
RH1121-26
Wheels
38
GB3452.1-1992
O type seal ring
Ø 14 x 2.65 mm
79
GB 894-86
Axis Cir Ciip
Ø 16 mm
39
GB3452.1-1992
O type seal ring
Ø 20 x 2.65 mm
80
HYQ-200
Gun
40
RH1121-10
Pump body
81
RH1121-27
Spare part list
41
RH1121-25
U seal ring
UN 8 x 14 x 6 mm
82
RH1121-55
High pressure pipe