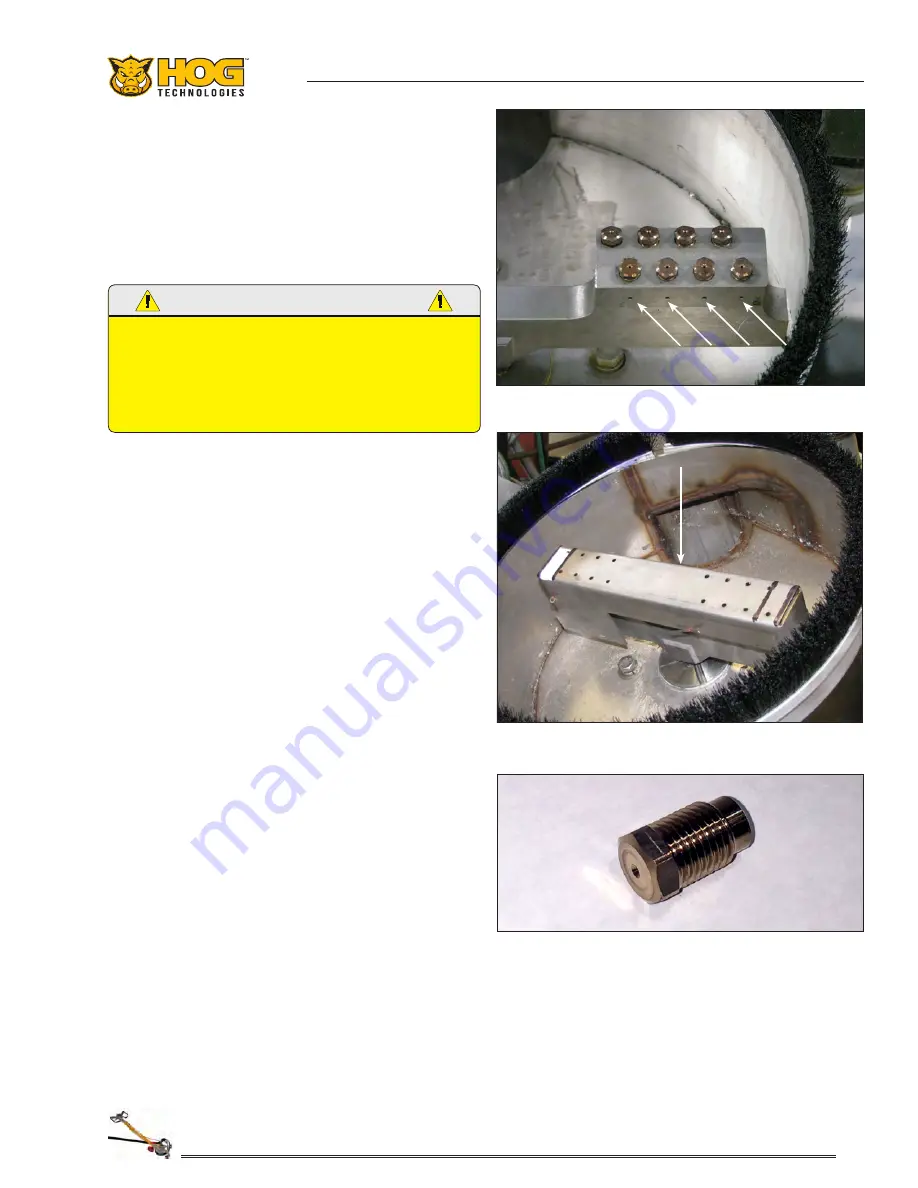
25
Section 2 - Components
threads indicates that the button seal is damaged
or not seating properly.
Leaks at the nozzle seats or thru-shaft threads
must be corrected before beginning high pressure
operations or the thru-shaft and/or spray bar will be
ruined. Should any repairs or adjustments be nec-
essary, disengage the pump to relieve all pressure
before making any required repairs or adjustments.
CAUTION
BEFORE ATTACHING THE SPRAY BAR TO THE THRu-SHAFT,
ALWAYS ENGAGE PuMP AT LOW PRESSuRE TO PuRGE THE
SYSTEM. ANY dIRT OR dEBRIS IN THE SYSTEM CAN CLOG
NOZZLE ORIFICE’S ANd CAuSE SYSTEM PRESSuRE TO
SPIKE EXCESSIvELY CAuSING dAMAGE TO COMPONENTS
OR THE RuPTuRE dISCS ON THE uHP PuMP TO BuRST.
Spray Bar Protector
Each spray bar is equipped with a spray bar pro-
tector that is held in place with one or two cotter
pins. The spray bar protector shields the nozzles
and spray bar from damage caused by debris dur-
ing blasting operations.
Be sure that the tabs of the protector face the
same way the spray bar is turning. This will ensure
that the debris contacts the protector instead of
the spray bar.
Never perform ultra-high pressure blasting opera-
tions without the spray bar protector installed as
this will dramatically shorten the life of the nozzles
and spray bar.
Nozzles
Ultra high pressure is produced by restricting
the flow of water at the nozzles on the blasting
head. Each nozzle delivers a stream of water at
extremely high pressure that is determined by
nozzle orifice size and it’s Gallon Per Minute (GPM)
flow at desired pressure. The performance ranges
from least aggressive (.005”) to most aggressive
(.015”). The condition of the nozzles is critical to
removal performance and maintaining a tight,
cohesive stream as water is forced through the
nozzles. Maximum productivity and 98% removal
without damage requires nozzles to be in excel-
lent condition. Nozzles should be inspected before
the start of each shift as part of the pre-operation
check or when the operator notices a loss in pres-
sure or a change in performance while blasting.
Typical Spray Bar, Nozzles & Weep Holes
Typical Spray Bar Protector
Spray Bar Nozzle
If visual inspection of the nozzle spray pattern
indicates that the pattern is not in the #1-4 quality
range as indicated on the Nozzle Quality Guide in
this section, the nozzle must be replaced.
Summary of Contents for HT1000SR
Page 2: ...2...
Page 6: ...6 NOTES...
Page 8: ...8 NOTES...
Page 18: ...18 NOTES...
Page 34: ...34 NOTES...
Page 76: ...76 NOTES...
Page 77: ...77 Appendix 3 Tools Spare Parts Mobile Tool System...
Page 80: ...80 NOTES...
Page 86: ...86 NOTES...
Page 89: ......