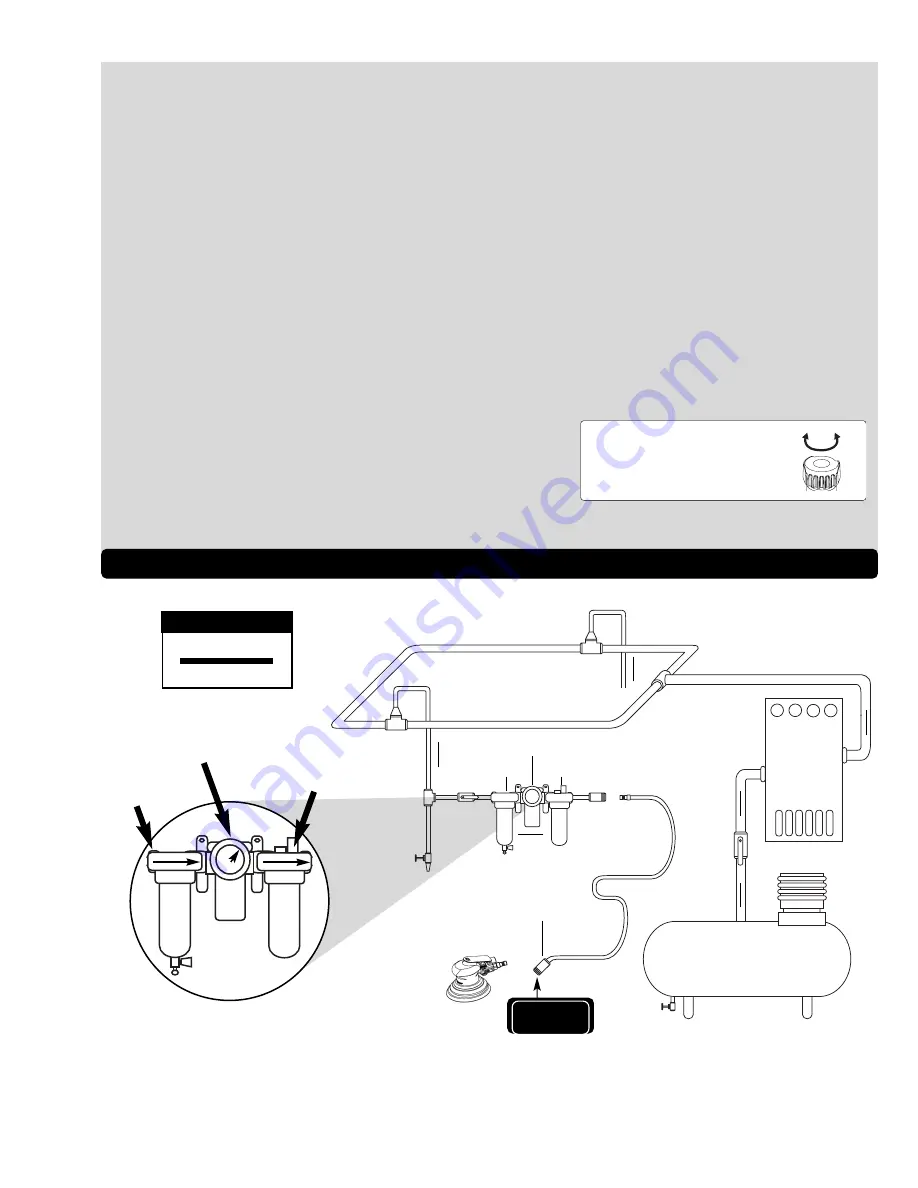
To Tool Station
Closed Loop Pipe System
(Sloped in the direction of air flow)
Ball
Valve
Ball
Valve
Filter
Coupler
Regulator
Lubricator
Air Flow
Drain
Valve
Drain
Valve
Air Tool
Air Compressor
and Receiver
Drain
Valve
Air Hose
Air Flow
Refrigerated
Air Dryer
2
Filter
Regulator
Lubricator
90 PSIG
(6.2 Bar)
SAFETY INSTRUCTIONS (continued)
• Do not use grinding wheels or cut-off wheels.
• Use only recommended accessories.
• Follow tool specifications before choosing size and type of accessory.
• Only use recommended fittings and air line sizes. Air supply hoses and air hose assemblies must have a minimum working pressure rating of 150 PSIG (10 bars, g) or 150
percent of the maximum pressure produced in the system, whichever is higher. (See Tool Machine Specifications Table.)
• This tool is rear exhaust. Exhaust may contain lubricants, vane material, bearing grease, and other materials flushed through the tool.
OPERATING INSTRUCTIONS
Warning:
Always wear eye protection. Operator of tool is responsible for following: accepted eye, face, respiratory, hearing and body protection.
Caution:
Hand, wrist and arm injury may result from repetitive work, motion and overexposure to vibration.
• Keep hand and clothing away from working end of the air tool.
• Working end of the air tool has potential hazard of cutting.
Operation:
Be sure that any loose clothing, hair and all jewelry is properly restrained.
• Secure inlet bushing on air tool with a wrench before attempting to install the air fitting to avoid damaging housing assembly.
• Check tool RPM (speed) with tachometer with air pressure set at 90 PSIG while the tool is running. If tool is operating at a higher speed than the RPM marked on the tool
housing, or operating improperly, the tool must be serviced and corrected before use.
• With power source connected at the air tool relieve hose of air pressure and disconnect tool from air supply when changing recommended accessories.
Caution:
Tool RPM must never exceed abrasive/accessory RPM rating.
• Connect air tool to power source. Be careful NOT to depress throttle lever in the process.
Do not expose air tool to inlet pressure above 90 PSIG or (6.2 Bars).
Caution:
After installing the accessory, before testing or use and/or after assembling tool, the HiVac Dynorbital-Spirit® must be started at a reduced speed to check for good
balance. Gradually increase tool speed. DO NOT USE if tool vibration is excessive. Correct cause, and retest to insure safe operation.
• Release the throttle lever in case of an interruption of the energy supply.
• Ensure that self-fixing accessories are mounted concentrically.
• Make sure that work area is uncluttered, and visitors are at a safe range from the tools and debris.
• Potentially explosive atmospheres can be caused by dust and fumes resulting from sanding or grinding.
• Always use dust extraction or suppression systems which are suitable for the material being processed.
• Use a vise or clamping device to hold work piece firmly in place.
• Do not apply excessive force on tool or apply “rough” treatment to it.
• Always work with a firm footing, posture and proper lighting.
Report to your supervisor any condition of the tool, accessories, or operation you consider unsafe.
Air System
1
DROP/MIN.
20
SCFM
LUBRICATOR SETTING
•
Ideally the air supply should be free of moisture.
To facilitate removing moisture from air supply, the
installation of a refrigerated air dryer after the
compressor and the use of drain valves at each
tool station is recommended.
•
Dynabrade Air Power Tools are designed to
operate at 90 PSIG (6.2 Bar/620 kPa) maximum
air pressure at the tool inlet, when the tool is
running. Use recommended regulator to control
air pressure.
➤
➤
➤
➤
➤
➤
90 PSIG MAX
(6.2 Bar)
Speed Regulator Flow Control
Maximum Flow:
Turn Clockwise.
Minimum Flow:
Turn Counter-clockwise.
+
-
Buy parts on line at https://Dynashop.co.uk/ for all things Dynabrade
Buy parts on line at https://Dynashop.co.uk/ for all things Dynabrade