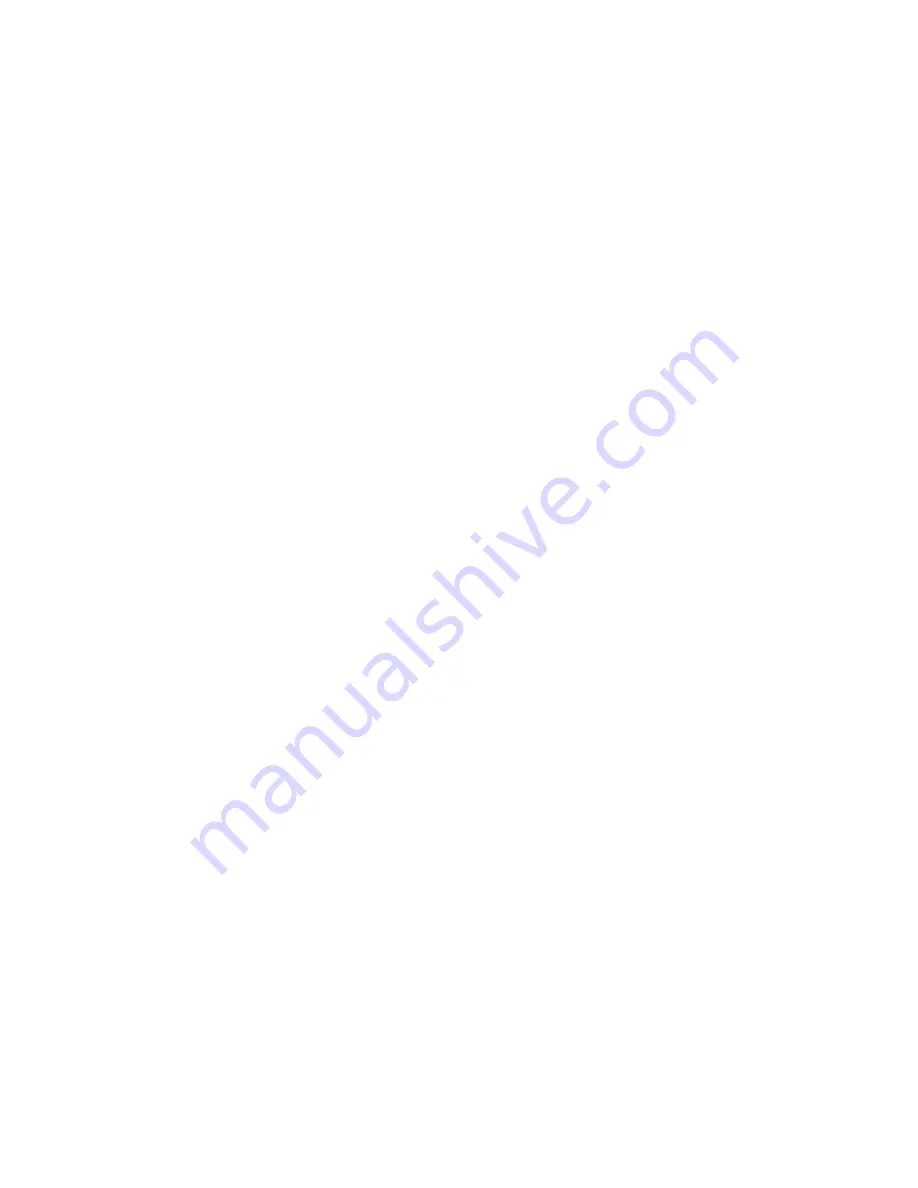
15
When servicing note that the reservoir capacitor C809 can remain charged to high voltage for some time after the a.c.
supply is removed. This can result in a shock hazard or damage to components whilst working on the receiver.
Do not try to test Q801 base emitter junction if C809 is charged, your meter will turn on the transistor which will discharge
the capacitor resulting in a collector emitter short circuit. Do not discharge C809 quickly with a screwdriver etc. The very
high current produced can damage the internal connections of the capacitor causing failure at a later date. Remember when
checking voltages to use a return path on the same side of TR802 for the Voltmeter earth to obtain the correct readings.
STANDBY OPERATION
As mentioned earlier the Startup Management of MC44608 is as follows:
The Vi pin 8 of IC800 is directly connected to the HV DC rail Vin. This high voltage current source is internally connected
to the VCC pin and thus issued to charge the VCC capacitor. The VCC capacitor charge period corresponds to the
Startup phase. When the VCC voltage reaches 13V, the high voltage 9mA current source is disabled and the device
starts working. The device enters into the switching phase.
To help increase the application safety against high voltage spike on pin
8 a small wattage 1k_series resistor is inserted
between the Vin rail and pin 8. After this start-up the IC can distinguish between the different modes of operation using the
following technique:
MODE TRANSITION
The LW latch is the memory of the working status at the end of every switching sequence. Two different cases must be
considered for the logic at the termination of the SWITCHING PHASE:
1. No Over Current was observed
2. An Over Current was observed
These two cases correspond to the two signals NOC in case of No Over Current and OC in case of Over Current.
The effective working status at the end of the ON time memorized in LW corresponds to Q=1 for no over current, and Q=0
for over current.
To enter the standby mode secondary side is reconfigured using D889 loop, this starts with the microprocessor s pin
47
becomes high; as the standby port becomes high Q503 conducts and Q802 becomes off then D889 conducts and the
high voltage output value becomes lower than the NORMAL mode regulated value. The shunt regulator IC118 is fully OFF.
In the SMPS standby mode all the SMPS outputs are lowered except for the low voltage output that supply the wakeup
circuit located at the isolated side of the power supply. In that mode the secondary regulation is performed by the Zener
diode (D801) connected in parallel to the TL431. The secondary reconfiguration status can be detected on the SMPS
primary side by measuring the voltage level at pin4 of TR802.
In the SMPS standby mode the 3 distinct phases are:
The SWITCHING PHASE: Similar to the Overload mode. The current sense clamping level is reduced. When VCC
crosses the current sense section, the C.S. clamping level depends on the power to be delivered to the load during the
SMPS standby mode. Every switching sequence ON/OFF is terminated by an OC as long as the secondary Zener diode
voltage has not been reached. When the Zener voltage is reached the ON cycle is terminated by a true PWM action.
The proper SWITCHING PHASE termination must correspond to a NOC condition. The LW latch stores this NOC status.
The LATCHED OFF PHASE: The MODE latch is set.
The STARTUP PHASE is similar to the Overload Mode. The MODE latch remains in its set status (Q=1).
The SWITCHING PHASE: The Standby signal is validated and the 200uA is sourced out of the Current Sense pin 2.
SMPS SWITCH OFF
When the mains is switched OFF, so long as the electrolytic bulk capacitor provides energy to the SMPS the controller
remains in the switching phase. Then the peak current reaches its maximum peak value, the switching frequency
decreases and all the secondary voltages are reduced. The VCC voltage is also reduced. When VCC is less than 6,5V,
the SMPS stops working.
MICROPROCESSOR IC501
IC 501 controls all the functions of the receiver operated by the remote control and the front panel customer controls.
It produces the on screen graphics, operates tuning, customers controls and engineering controls, and also incorporates
all of the Teletext functions. It also controls the video processor, the audio processor, and the tuner. The circuits just
mentioned are controlled via the I²C bus. Also IC501 controls the video source switching, vertical position adjustment and
the vertical linearity adjustment via its ports.
An external 8K EEprom is used by the micro. The EEprom comes fully programmed. The main clock oscillator is 4.0MHz
crystal X501 on pins 50 and 51. Reset is provided on pin 2 via Q504. On switching on pin 2 becomes high and the controller
gets reset which stays valid till a low signal comes on that pin.
CONTROLS
Command information from the infra red remote controller is fed through the sensor IC502 to pin 1 of the microprocessor.
Operation of the customer front panel keys is detected by pin 8 that is an ADC (analogue to digital converter). Pressing a
switch will connect the 5V to the ground through a particular resistor that determines the value of the voltage on pin8 at that
instant. This obtained value is comprehended by the micro and the corresponding operation is performed. Refer to the
following table:
Summary of Contents for CG2026S
Page 26: ...Block Flow Chart 25 ...
Page 27: ...Power Supply 26 ...
Page 28: ...Micro Controller 27 ...
Page 29: ...Video Circuit 28 ...
Page 30: ...Stereo Circuit 29 ...
Page 31: ...Audio Video Connector 30 ...
Page 32: ...Deflection Circuit 31 ...
Page 33: ...CRT Circuit 32 ...
Page 34: ...C21F65 CRT Board ...
Page 35: ...HITACHI No 0110 Video Controller 33 ...
Page 36: ...HITACHI No 0110 SMPS Circuit 34 ...
Page 37: ...HITACHI No 0110 Micro Controller 35 ...
Page 38: ...HITACHI No 0110 Audio Video Circuit 36 ...
Page 39: ...HITACHI No 0110 Deflection Circuit 37 ...
Page 40: ...HITACHI No 0110 Stereo Circuit 38 ...
Page 41: ...14 13 11 9 6 8 7 3 4 2 5 1 39 ...