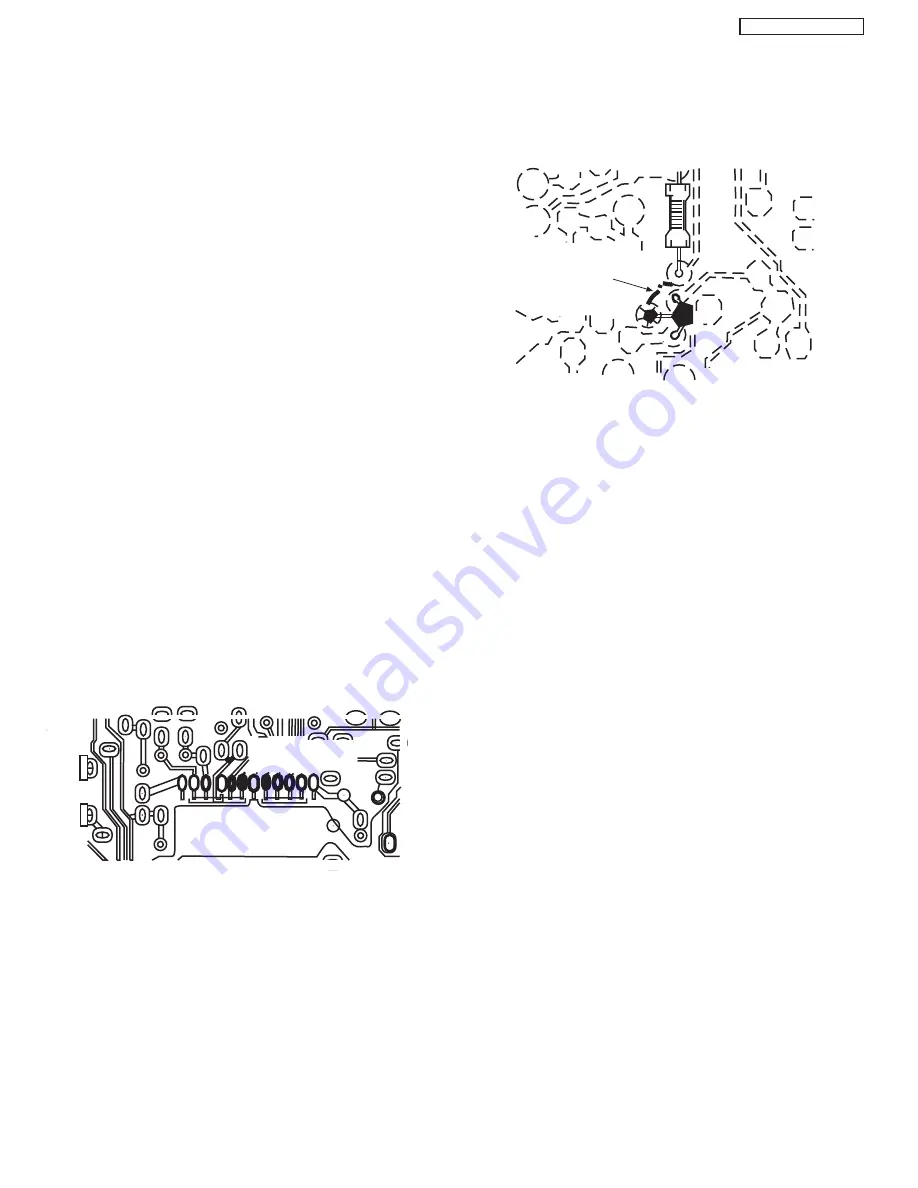
SERVICING PRECAUTIONS
Fuses and conventional Resistor Removal/Replacement
1.
Clip each fuse or resistor lead at top of circuit board hollow
stake.
2.
Securely crimp leads of replacement component around stake
1/8 inch from top.
3.
Solder the connections.
CAUTION:
Maintain original spacing between the replaced
component and adjacent components and the
circuit board, to prevent excessive component
temperatures.
Circuit Board Foil Repair
Excessive heat applied to the copper foil of any printed circuit board
will weaken the adhesive that bonds the foil to the circuit board,
causing the foil to separate from, or “lift-off” the board. The follow-
ing guidelines and procedures should be followed whenever this
condition is encountered.
In Critical Copper Pattern Areas
High component/copper pattern density and/or special voltage/cur-
rent characteristics make the spacing and integrity of copper pattern
in some circuit board areas more critical than in others. The circuit
foil in these area is designated as Critical Copper Pattern. Because
Critical Copper Pattern requires special soldering techniques to
ensure the maintenance of reliability and safety standards, contact
your Hitachi personnel.
At IC Connections
To repair defective copper pattern at IC connections, use the follow-
ing procedure to install a jumper wire on the copper pattern side of
the circuit board. (Use this technique only on IC connections.)
1.
Carefully remove the damaged copper pattern with a sharp
knife. (Remove only as much copper as absolutely necessary.)
2.
Carefully scratch away the solder resist and acrylic coating (if
used) from the end of the remaining copper pattern.
3.
Bend a small “U” in one end of a small-gauge jumper wire and
carefully crimp it around the IC pin. Solder the IC connection.
4.
Route the jumper wire along the path of the cut-away copper
pattern and let it overlap the previously scraped end of the good
copper pattern. Solder the overlapped area, and clip off any
excess jumper wire.
At Other Connections
Use the following technique to repair defective copper pattern at
connections other than IC Pins. This technique involves the instal-
lation of a jumper wire on the component side of the circuit board.
1.
Remove the defective copper pattern with a sharp knife.
Remove at least 1/4 inch of copper, to ensure hazardous condi-
tion will not exist if the jumper wire opens.
2.
Trace along the copper pattern from both wire sides of the pat-
tern break and locate the nearest component directly connected
to the affected copper pattern.
3.
Connect insulated 20-gauge jumper wire from the nearest com-
ponent on one side of the pattern break to the lead of the near-
est component on the other side. Carefully crimp and solder the
connections.
CAUTION:
Be sure the insulated jumper wire is dressed so
that it does not touch components or sharp
edges.
Frequency Synthesis (FS) Tuning Systems
1.
Always unplug the instrument AC power cord before discon-
necting or reconnecting FS tuning system cables and before
removing or inserting FS tuning system modules.
2.
The FS tuner must never be disconnected from the FS tuning
control module while the power is applied to the instrument.
3.
When troubleshooting intermittent problems that might be
caused by defective cable connection(s) to the FS tuning sys-
tem, remove the instrument AC power as soon as the defective
connector is found and finish confirming the bad connection with
a continuity test. This procedure will reduce the probability of
electrical overstress of the FS system semi-conductor compo-
nents.
CRIMP AND
SOLDER
BARE JUMPER
WIRE
Install Jumper Wire and Solder
DEFECTIVE
COPPER
REMOVED
Insulated Jumper Wire
6
LC67
Summary of Contents for 50VS69A
Page 56: ...CONNECTION DIAGRAM TABLE OF CONTENTS 55 LC67 ...
Page 57: ...LC67 56 FINAL WIRING DIAGRAM TABLE OF CONTENTS ...
Page 58: ...LC67 57 FINAL WIRING DIAGRAM TABLE OF CONTENTS ...
Page 59: ...LC67 58 FINAL WIRING DIAGRAM TABLE OF CONTENTS ...
Page 60: ...LC67 59 FINAL WIRING DIAGRAM TABLE OF CONTENTS ...
Page 69: ...FINAL ASSEMBLY GUIDE TABLE OF CONTENTS 68 LC67 ...
Page 70: ...FINAL ASSEMBLY GUIDE 69 LC67 ...
Page 71: ...FINAL ASSEMBLY GUIDE 70 LC67 ...
Page 72: ...FINAL ASSEMBLY GUIDE 71 LC67 ...
Page 73: ...FINAL ASSEMBLY GUIDE 72 LC67 ...
Page 74: ...FINAL ASSEMBLY GUIDE 73 LC67 ...
Page 75: ...FINAL ASSEMBLY GUIDE 74 LC67 ...
Page 104: ...PRINTED CIRCUIT BOARDS LC67 POWER PWB Solder side LC67 103 ...
Page 122: ......