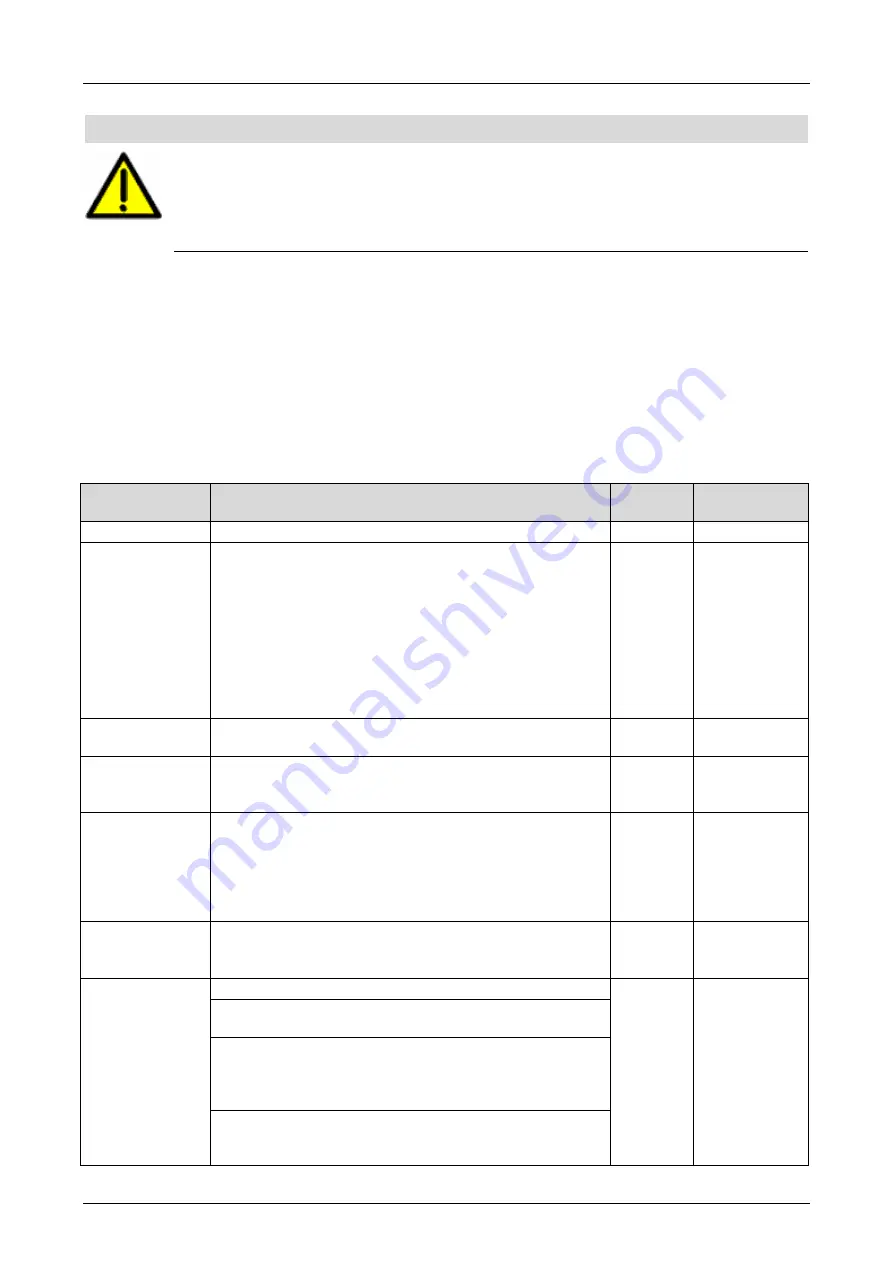
7 Start-Up
System Manual Compact Systems
Page 52 of 110
HI 800 141 E Rev. 2.02
NOTE
Damage of the device possible!
Do not exchange the terminals L+ and L-, or connect them to other terminals of the
device!
In case of a false connection, a pre-fuse blows to prevent the device from being
damaged.
7.3
Configuration with SILworX - CPU OS V7 and Higher
This chapter describes how to configure resources using SILworX for CPU OS V7
and higher
.
7.3.1
Configuring the Resource
The resource properties and the hardware output variables are changed at this level.
7.3.1.1
Resource Properties
The system parameters of the resource determine the controller behavior during operation and
can be set in SILworX, in the
Properties
dialog box of the resource.
Parameter
Description
Default
value
Setting for safe
operation
Name
Resource name
Arbitrary
System ID [SRS] System ID of the resource
1...65 535
The value assigned to the system ID must differ to the
default value, otherwise the project is not able to run!
60 000
Unique value
within the
controller
network. This
network
includes all
controllers that
can potentially
be
interconnected
Safety Time [ms] Safety time in milliseconds
20...22 500 ms
600 ms/
400 ms
1)
Application-
specific
Watchdog Time
[ms]
Watchdog time in milliseconds: 4...5000 ms for F*03
devices and modules; 8…5000 ms for standard devices
and modules
200 ms/
100 ms
1)
Application-
specific
Target Cycle
Time [ms]
Targeted or maximum cycle time, see
Target Cycle Time
Mode
, 0...7500 ms. The maximum target cycle time value
may not exceed the
watchdog time
- minimum watchdog
time; otherwise it is rejected by the PES.
If the default value 0 ms is set, the target cycle time is not
taken into account.
0 ms
Application-
specific
Target Cycle
Time Mode
Use of
Target Cycle Time [ms]
With F*03 devices/modules, all the values can be used;
with standard devices/modules, only
fixed
values!
Fixed-
tolerant
Application-
specific
Multitasking Mode Only applicable with F*03 devices/modules!
Mode 1
Application-
specific
Mode 1
The duration of a CPU cycle is based on the
required execution time of all user programs.
Mode 2
The processor provides user programs with a
higher priority the execution time not needed by
user programs with a lower priority. Operation
mode for high availability.
Mode 3
During the execution time not needed by the
user programs, the processor waits for the time
to expire, thus increasing the cycle.