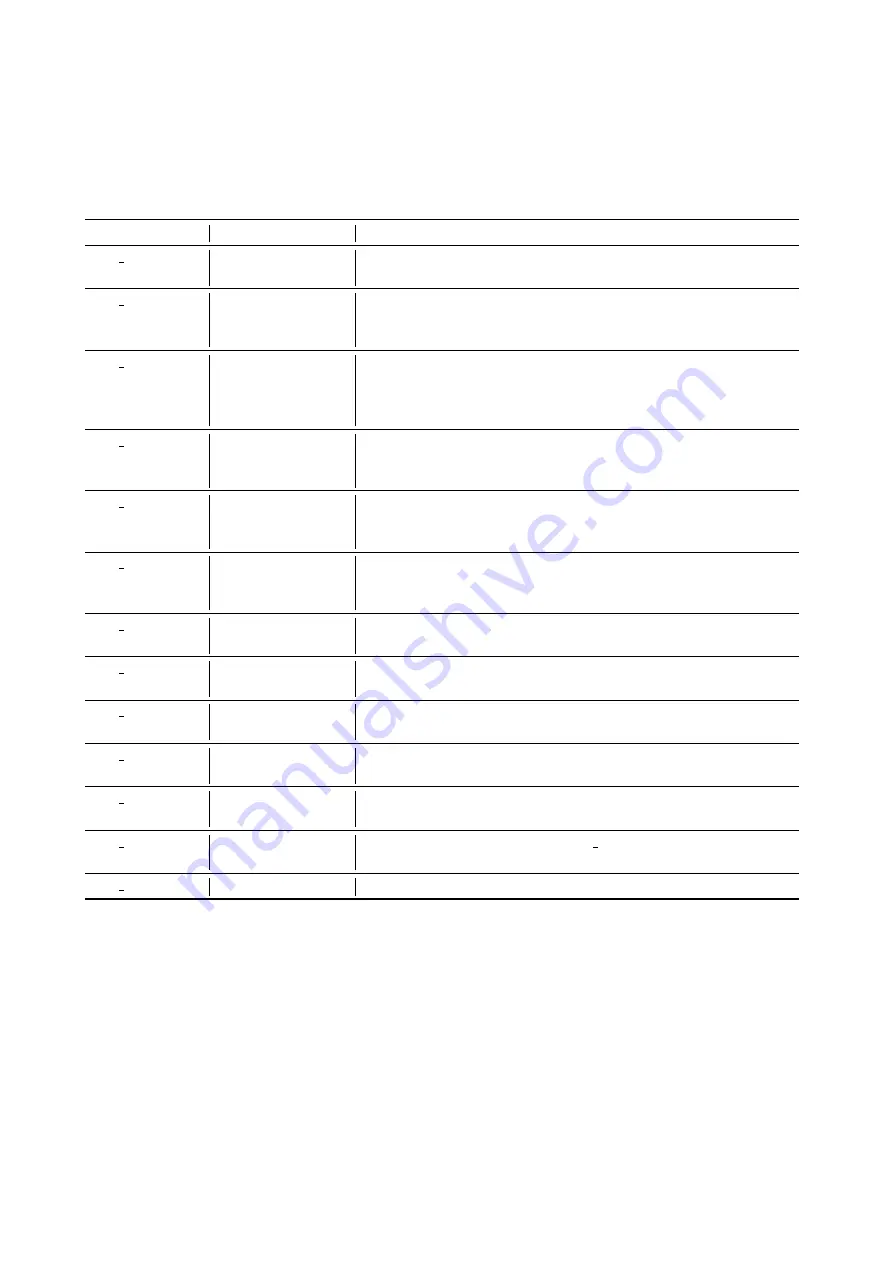
3.3
Alarm & Warning Table
3.3.1
General Alarms
Id Alarm
Meaning
Solution
AL 1
General
EEPROM failure
Detected an Error in the internal memory of the card. Turn off
and on again. If the error persists, replace the card.
AL 2
General
Key-off failure
Return on the key signal. Turn off the machine, wait at least 2
seconds, and then turn it on again. If the problem persists, replace
the key block.
AL 3
General
Undervoltage
Detected supply voltage less than 15V (even instantly). Check
the batteries and their connection and the connection between
the batteries and the main card. If the error persists, replace the
card.
AL 4
General
Overvoltage
Detected supply voltage more than 35V (even instantly). Check
the batteries and their connection and the connection between the
batteries and the main card. If the error persists, replace the card.
AL 6
General
Keyboard
Communication
No communication between display and main board. Check the
connection between the cards. If the problem persists, replace the
main card or the display card.
AL 7
General
Communication
HFM
Lack of communication between the BB and the main card. Check
the connection between the cards. If the problem persists, replace
the main card or the BB.
AL 8
General
Communication 1
Internal error in the main card BUS data, turn off and on again.
If the problem persists, replace the main card.
AL 9
General
Communication 2
Internal error in the main card BUS data, turn off and on again.
If the problem persists, replace the main card.
AL 10
General
Insert Tag
One of the enabled TAGs is not inserted. Enter one of the enabled
TAGs in the Slot.
AL 11
General
Invalid Tag
The inserted TAG is not enabled. Enter one of the enabled TAGs
in the Slot.
AL 12
General
Update in
progress. . .
The machine is updating the parameter list. Wait for the end of
the operation.
AL 13
General
Restart
the Machine
After updating the parameters (AL 12) indicates that is necessary
to restart the machine.
AL 14
General
Recovery Full
The Recovery Tank is Full (Warning W2). Drain it.
41
Summary of Contents for 108538
Page 1: ...SERVICE MANUAL TRIDENT R30SC R28SC Version AA Date August 5 2019 Document Number 100x...
Page 4: ...Part I Product Introduction 4...
Page 10: ...1 6 Machine Dimensions 1 6 1 R30SC 10...
Page 11: ...1 6 2 R28SC 11...
Page 15: ...Part II Anomalies Resolution Guide 15...
Page 24: ...Part III Functional Groups 24...
Page 26: ...3 2 Location of Electrical Components 3 2 1 R30SC R28SC Plus 26...
Page 28: ...3 2 3 R30SC Base 28...
Page 64: ...4 6 Related electrical circuit 4 6 1 R30SC Base 64...
Page 66: ...4 6 2 R30SC PLUS 66...
Page 76: ...5 6 Related electrical circuit 5 6 1 R28SC PLUS 76...
Page 84: ...6 6 Related electrical circuit 6 6 1 R28SC Base 84...
Page 86: ...6 6 2 R30SC R28SC PLUS 86...
Page 94: ...7 5 Related electrical circuit 7 5 1 R30SC Base 94...
Page 96: ...7 5 2 R30SC R28SC PLUS 96...
Page 104: ...8 5 Related electrical circuit 8 5 1 R30SC Base 104...
Page 106: ...8 5 2 R30SC R28SC PLUS 106...
Page 112: ...Part IV Accessories and Add On 112...