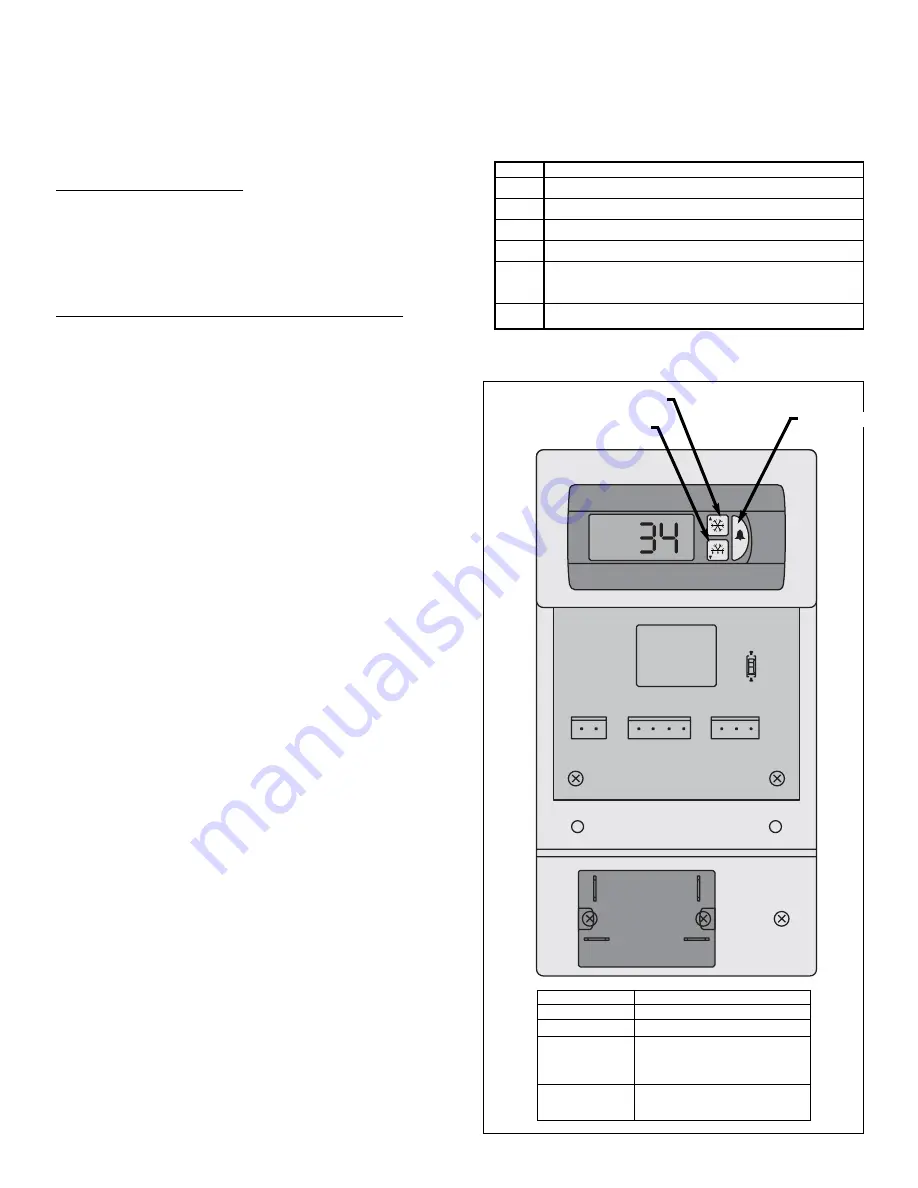
14
Alarm Operation
Indications on the Display
If the defrost, or compressor key blinks, it means that the
corresponding function is delayed by a timing routine or
inhibited. Other two-character messages may appear on
the screen to indicate changes of state or alarm condi-
tions. Values shown in Table 1.
Viewing and Changing the Temperature Setpoint
The temperature setpoint is the comparison point for the
control temperature input. To change the set point value:
1. Press the
Alarm
key for more than 5 seconds until the
setpoint is displayed and blinking.
2. Press the
Compressor
key and Defrost keys to
raise/lower the value.
3. Press the
Alarm
key again to accept the new value.
Changing Other Setpoints
There are two levels of setpoints in the ESC3. The first
level does not require a password to change (unless the
buttons are locked out). The setpoints that can be
changed in this manner are identified in Table 1 (back
side) as a USER setpoint. All other setpoint do require a
password to change and are identified in Table 2 (back
side) as an OEM setpoint. To change USER-level set-
points:
1. Press the
Alarm
key and hold it until the letters PS are
displayed.
2. Use the
Compressor
and
Defrost
key to scroll through
the codes for the different set points (see Table 1 and
Table 2).
3. When the code is displayed for the setpoint you wish to
change, press the
Alarm
key. The value for that
setpoint will be displayed.
4. Press the
Compressor
or
Defrost
key to change the
value
5. Press the
Alarm
key to go back to the code.
At this point you must press the
Alarm
key to accept the
change or press the
Compressor
or
Defrost
key to scroll
to the next USER setpoint. To accept the changes, press
and hold the
Alarm
key until the display stops flashing. To
change OEM-level setpoints, the password must be
entered. To do this press and hold the
Alarm
key until the
letters PS are displayed. When PS is displayed release
the alarm key and 0 will be displayed. Press the
Compressor
or
Defrost
keys to enter the password (22 is
the default) then press the
Alarm
key. PS will be dis-
played again. At this point, pressing the
Compressor
or
Defrost
key will scroll through the legend for all setpoints.
To change the setpoints, use the identical procedure that
is used to change a USER setpoint.
Code
Meaning
E0
Air probe has failed
E1
Defrost termination or product probe has failed
LO
Low temperature alarm
HI
High temperature alarm
Ed
Defrost timeout has occurred
(did not terminate correctly)
dF
Case is in defrost (not an alarm)
Table 1
K1
J4
J6
J5
R1
K2
1
5
4
6
120V
ac
Neutral
Fan
Compressor
120V Hot
Defrost
Amb temp
Common
Def temp
ESC3 Case Controller
Alarm Key
Defrost Key
Compressor Key
Control Input
0.39 A, 120 Vac, 60 Hz
Common Input
11.2 A, 120 Vac, 60 Hz
Fan Output
1 FLA, 6 LRA, 120 Vac, 60 Hz
Compressor Output
1.5 HP @ 120 Vac
(K2)
(external relay #841-S-1A-D
by Song Chuan)
Defrost Output
10.0 A, 120 Vac, Resistive, 60 Hz
(P/N 850-3500 only)
CONTROL SETTINGS
ESC3 Controls
Summary of Contents for 05DMA
Page 1: ...DAIRY DELI PRODUCE C A S E S MODEL O5DMA HANDBOOK INSTALLATION OPERATION P056442G Rev 10 12 04...
Page 4: ......
Page 20: ...16 WIRING DIAGRAMS MODEL O5DMA...
Page 29: ...25 NOTES...
Page 30: ...26 NOTES...