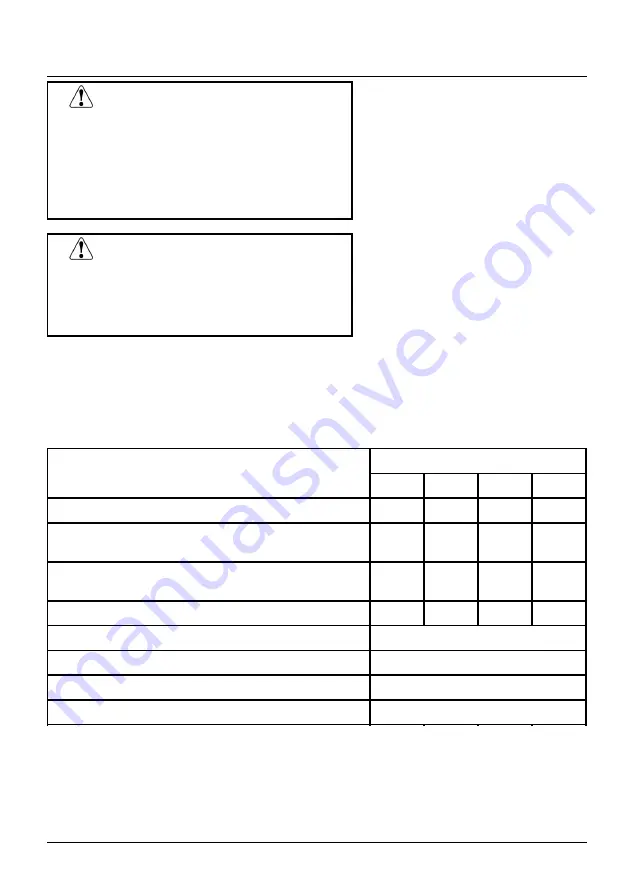
121
Technical Data
Operator's Manual GB
10.4
CAUTION
The operator has to arrange for the GÜ on
basis of determination of the used share of
the theoretical using time, respectively latest
after 10 years of use.
(See BGV D8, as well as FEM 9.755 latest
editions).
CAUTION
In the country of application, the national
regulations which are individually valid for
hoisting and pulling units, have to be fol-
lowed.
10.4 Performance Data TC1, rope ca-
pacity
Rope diameter 8 mm
Rope capacity according to DIN 15020 Grooved
drum
Rope layer
1
2
3
4
Hoisting force in kN
11.5
11
10
9.5
Rope lenght in m/layer, rope diameter 8 mm
10
12
12
13
(4*)
Total rope length in m
10
22
34
47
(38*)
Rope speed v in m/min with standard motor
42
46
50
54
Weight in kg (ca):
1)
hoist
2)
hoist + rope
1)
54
2)
64
Flow
40 l/min
Static pressure
220 MPa
Dynamic pressure
170 MPa
(*) rope length 38 m