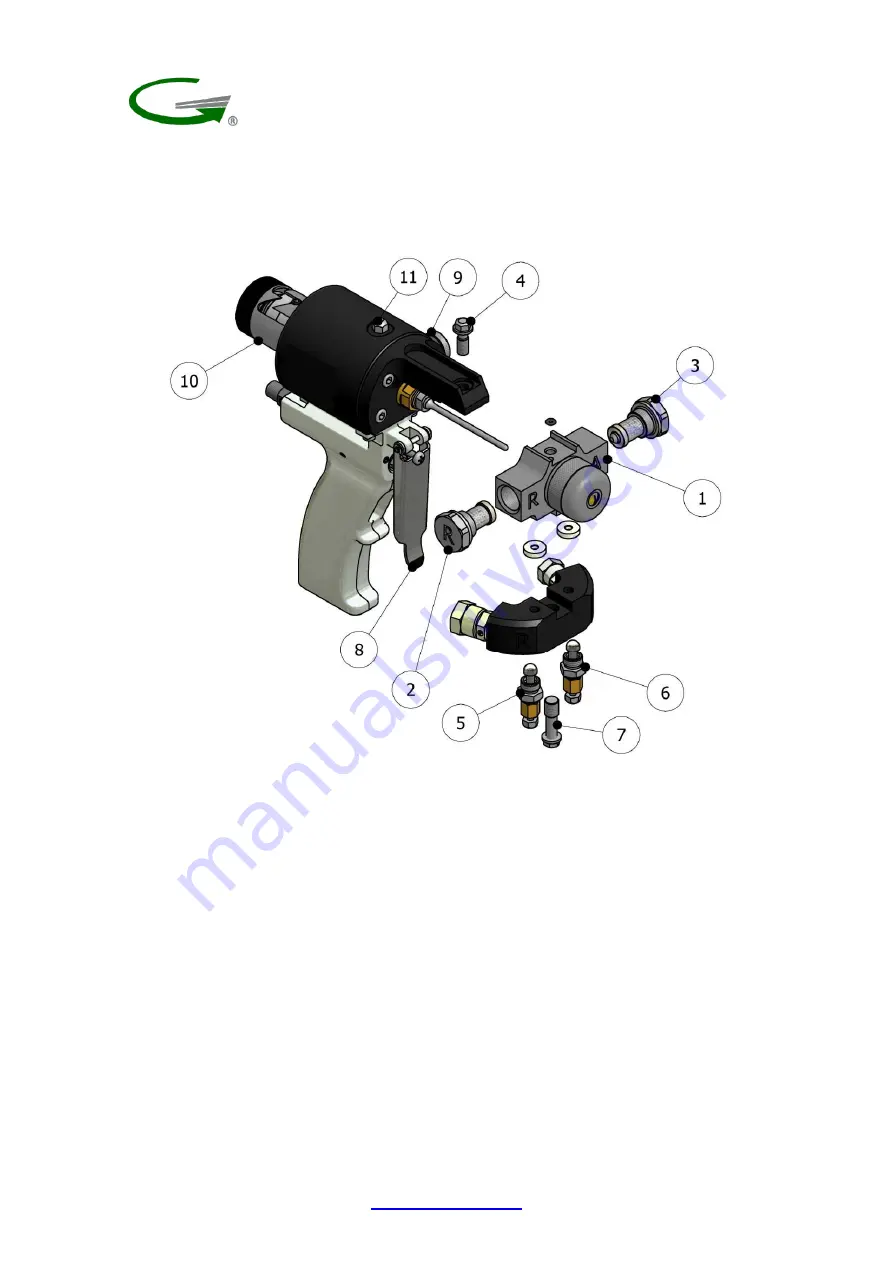
Projection Gun novaG-M
Service Manual
6/28
1.5 Issue
Figure. 1
For better knowledge of the elements of the
novaG-M
gun, the main components and their
description are shown. For a more precise identification, see the Components Manual ref. NR-
00017.
1.
Mixhead
2.
Polyol side cartridge unit
3.
Iso side cartridge unit
4.
Block fixture bolt
5.
Polyol manual valve
6.
Isocyanate manual valve
7.
Entry block fixture bolt
8.
Trigger
9.
Air flow regulator
10.
Safety device
11.
Needle adjustment nut blocking screw
GENERAL DESCRIPTION