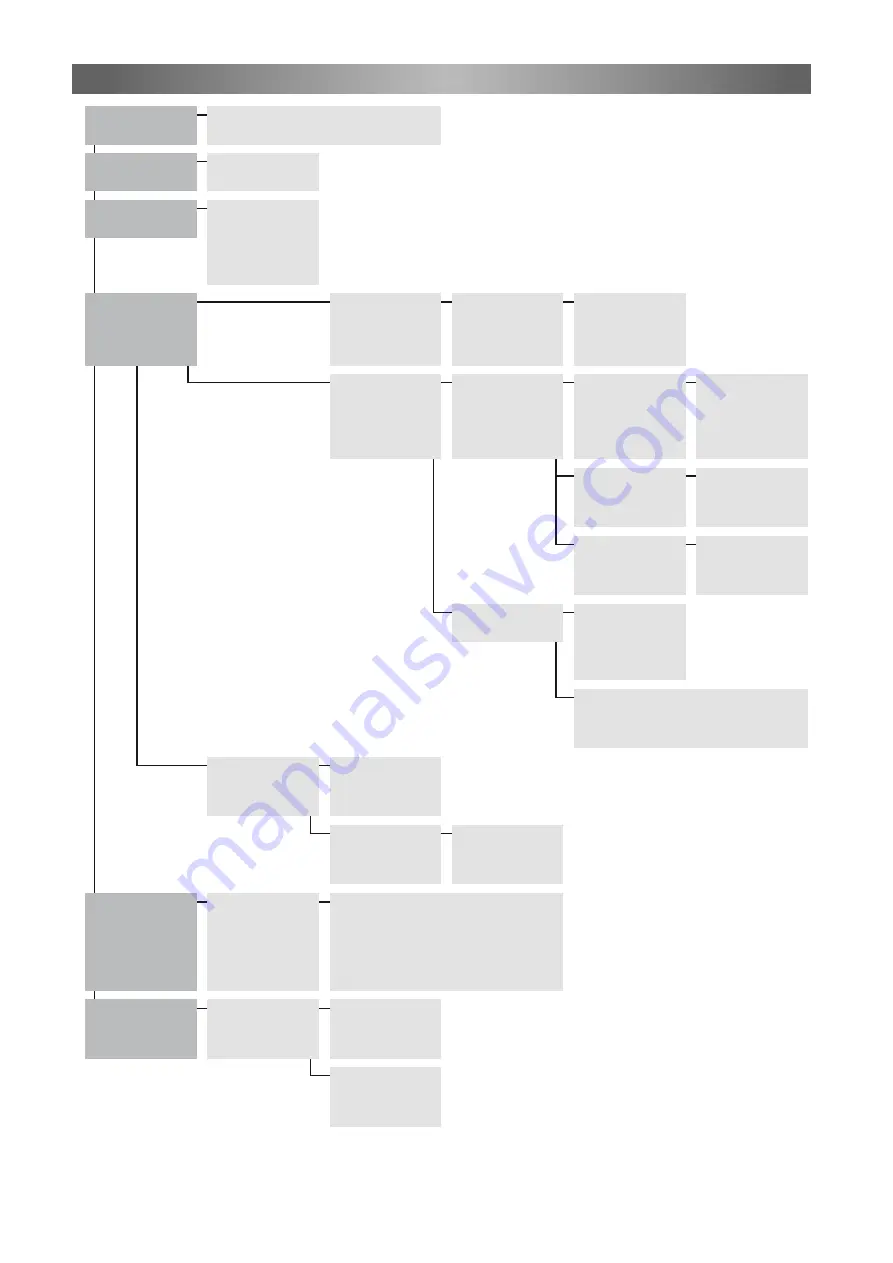
14
Trouble shooting
by qualified personnel
The machine
does not work.
The canister(s) is / are
empty.
The fluid is viscous.
The water does not
reach the brush(es)
when the machine is
switched on.
The detergent /
disinfec tant of the
hand washing station
is not output at all
or with insufficient
quantity only when
using the station.
The turnstile does not
enable access.
The power supply is interrupted or one of the components
failed. Please consult qualified specialists.
Change the canister.
Try to drawn in clear
water. When the ma-
chine operates correctly,
dilute the fluid upstream
of the canister and/or
change the nozzle.
Is there a valve installed
upstream to the
machine?
Check in the system
setting how big the
output quantity is and
change it.
Check if the hygiene
station enables hand
cleaning.
Check whether the valve
for setting the water
quantity is not fully
open.
(*) Remove the
hose from the check
valve of the dosing
system. Place your finger
to feel if there is any
negative pressure.
In the affirmative, open
the valve installed up-
stream to the machine.
Inspect if there is any foreign matter in the feeding line
blocking the flow. Test the faultless function of the two
spray nozzles and sensors.
In the affirmative, get
the turnstile tested for
mechanical function by
qualified personnel.
In the negative, the
solenoid valve does not
open.
In the negative, disinfect
the hands properly
according to instruction.
In order to check
this, close the valve
completely and check
whether the fluid is
drawn in.
Sucking effect present.
Sucking effect absent.
Get the solenoid valve
replaced by a qualified
specialist, if required.
If the cleaning fluid is
not drawn in, proceed
to (*).
Make sure that the
suction hose or suction
filter is not clogged by
depositions.
Make sure that the
suction hose is free of
damage.
Check whether the
existing nozzle is not
clogged.
Dismount the check valve. Check the
two O-ring seals of the cone and spring (if required,
replace the complete dosing flap).
Remove any clogging
or replace the parts.
Do not forget to fit the
filter on to the inlet of
the hose.
In the affirmative,
change the hose. Do not
forget to fit the filter on
to the inlet of the hose.
If the nozzle is clogged,
eliminate such clogging
or replace the nozzle.
Dismantle the nozzle and
clean the nozzle of the
dosing system because
depositions may have
built up.